Showing 13–19 of 19 results
-
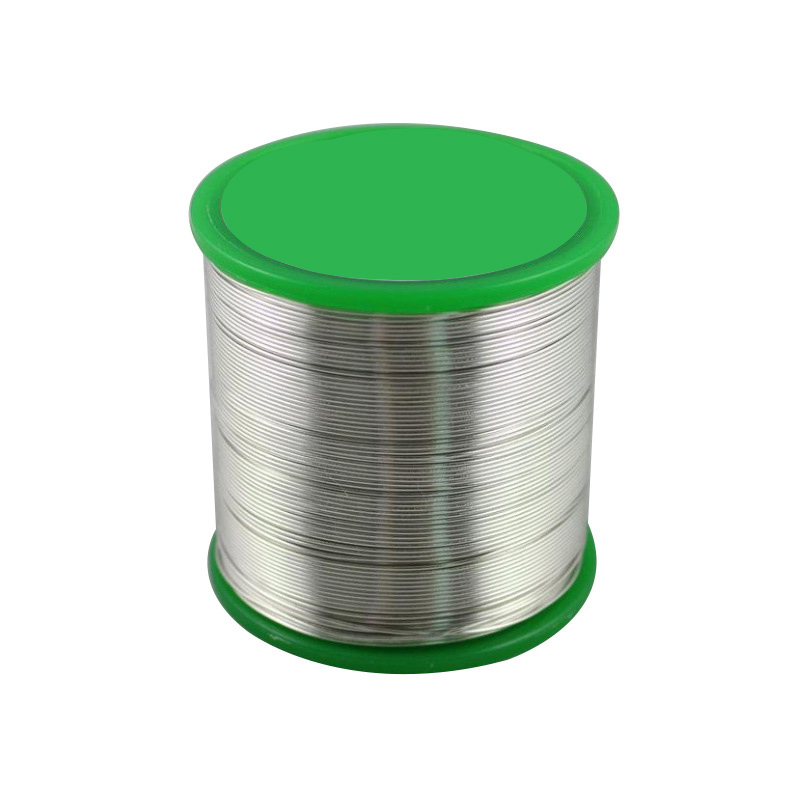
- Low Melting Point: Tin wire has a relatively low melting point (232°C), making it ideal for soldering applications where a soft, low-temperature process is required.
- Excellent Solderability: Due to its low melting point and excellent flow characteristics, tin wire is widely used in electronic soldering, creating strong, reliable joints.
- Corrosion Resistance: Tin wire is highly resistant to corrosion and oxidation, especially in humid or saline environments, ensuring longevity and performance.
- Non-toxic: Unlike lead-based solders, tin wire is non-toxic, making it an environmentally friendly and safe alternative for various applications, especially in food and medical devices.
- Malleability and Ductility: Tin wire is relatively soft and ductile, which allows it to be easily shaped and manipulated without cracking or breaking.
- Conductivity: While not as conductive as copper or silver, tin still offers sufficient electrical conductivity for most standard applications.
- Customizability: Tin wire can be customized in different diameters, grades of purity, and surface finishes to suit specific requirements.
-
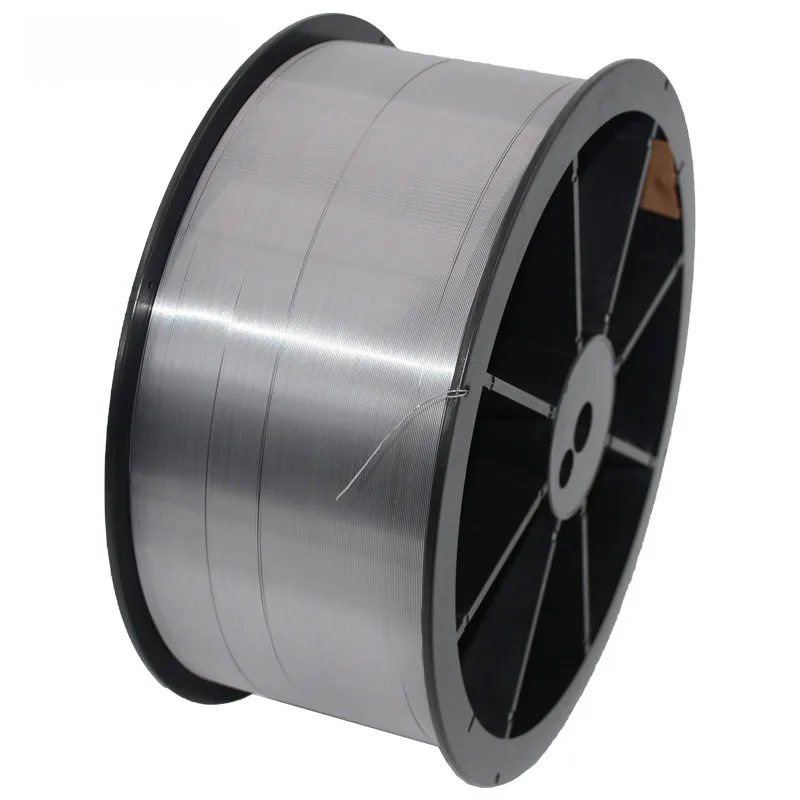
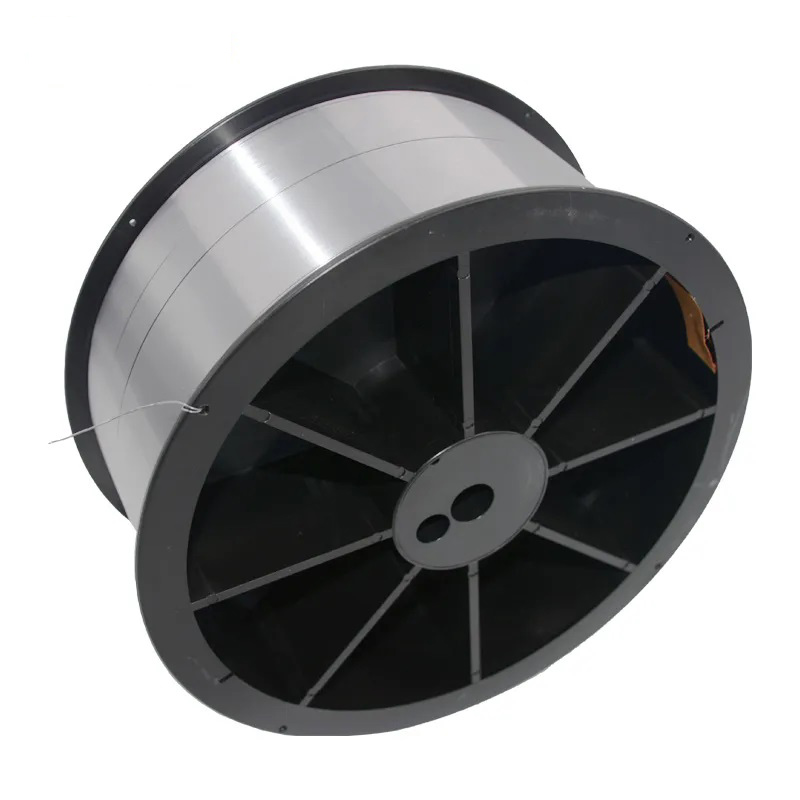
- High Melting Point: Tantalum has a melting point of approximately 3,020°C (5,468°F), which makes it an excellent material for high-temperature applications. This high melting point ensures that tantalum wires can perform effectively in environments where other materials would degrade or melt.
- Excellent Corrosion Resistance: One of the most remarkable properties of tantalum wires is their exceptional resistance to corrosion. Tantalum forms a protective oxide layer on its surface, which prevents corrosion even in highly acidic or alkaline environments. This makes tantalum wires ideal for use in the chemical industry and in environments where exposure to corrosive substances is common.
- Biocompatibility: Tantalum is biocompatible, meaning it does not cause any harm or rejection when implanted into the human body. This property makes tantalum wires ideal for use in medical applications such as implants, surgical devices, and electrodes.
- High Strength and Ductility: Despite its high melting point, tantalum wires maintain high mechanical strength and are highly ductile. This makes them easy to work with in manufacturing processes like wire drawing, while still providing durability under mechanical stress.
- Electrical Conductivity: Tantalum wires have good electrical conductivity, which makes them suitable for use in capacitors, resistors, and other electronic components that require stable and reliable performance.
- Thermal Stability: Tantalum wires maintain stability across a broad range of temperatures, from cryogenic levels to extremely high temperatures. This makes them ideal for applications that demand excellent thermal properties.
-
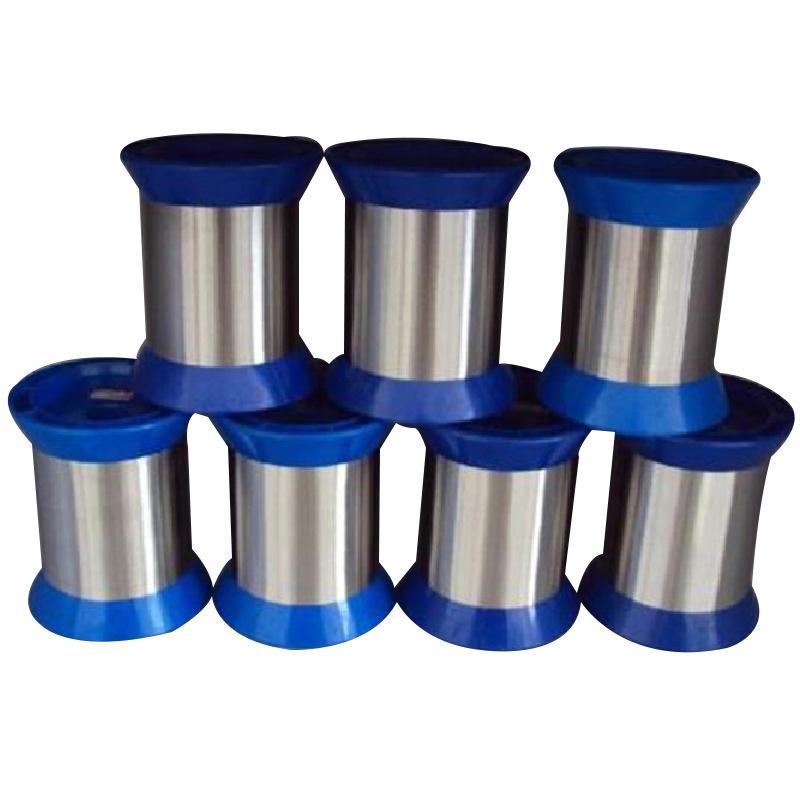
- Durability in Extreme Conditions: Titanium wire retains its properties in extreme temperatures and corrosive environments, ensuring reliable performance.
- Lightweight Design: The low density of titanium wire reduces the weight of structures and components, crucial for aerospace and automotive industries.
- Environmentally Friendly: Titanium is non-toxic and fully recyclable, making it a sustainable material choice.
- Customizability: Titanium wire can be manufactured in various diameters, grades, and finishes to meet specific industry requirements.
- Superior Surface Finish: The wire can be polished or coated to enhance its performance and appearance in specialized applications.
-
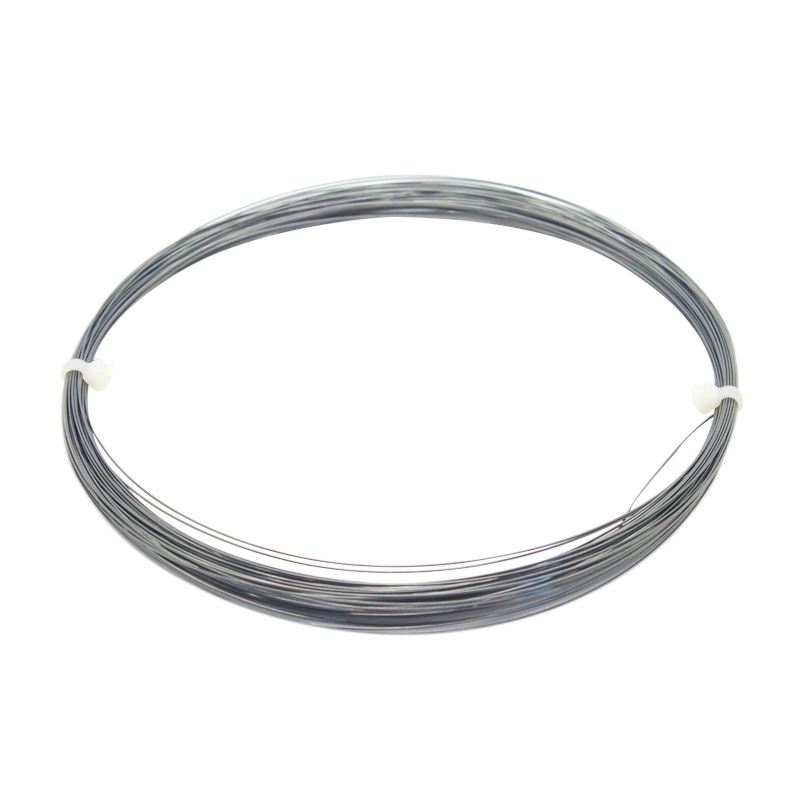
- High Strength and Toughness: Vanadium wire has remarkable strength and toughness, which makes it ideal for applications requiring high endurance and resistance to mechanical stress.
- Corrosion Resistance: Vanadium is highly resistant to corrosion, making it suitable for use in harsh environments, including high-temperature and corrosive applications.
- High Melting Point: Vanadium wire has a high melting point of approximately 1910°C, allowing it to maintain its structural integrity under extreme temperature conditions.
- Good Thermal Conductivity: Vanadium wire exhibits good thermal conductivity, which helps in heat dissipation, especially in high-temperature environments.
- Ductility and Malleability: While strong and durable, vanadium wire remains ductile, which allows it to be easily processed and shaped for a wide range of applications.
- Magnetic Properties: Vanadium has relatively low magnetic susceptibility, which is beneficial in specific industrial and scientific applications that require minimal magnetic interference.
-
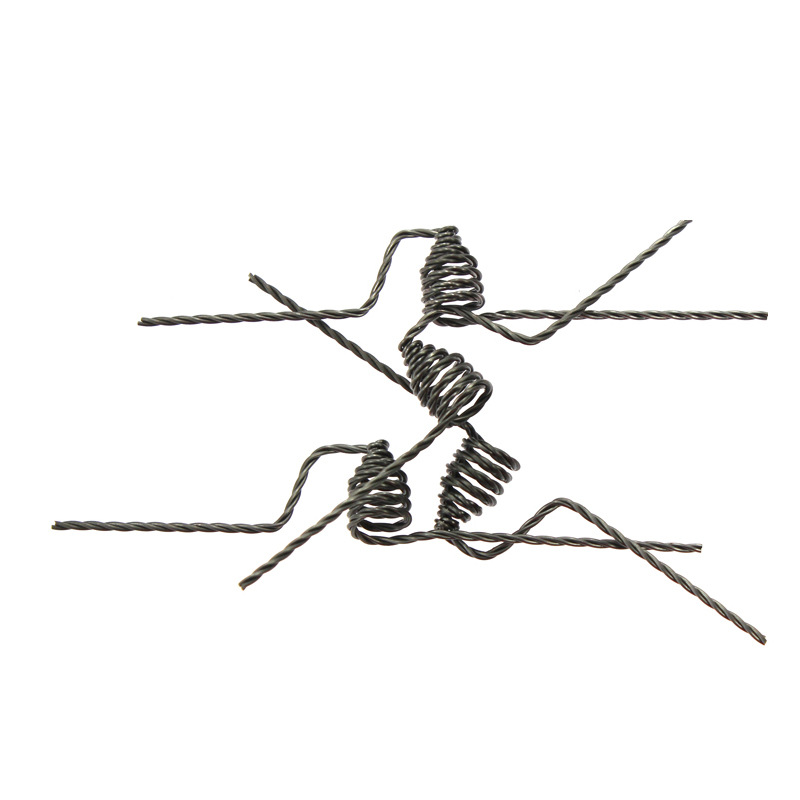
- High Melting Point: Tungsten has one of the highest melting points of any metal, at approximately 3,422°C (6,192°F). This property allows tungsten wire baskets to perform exceptionally well in high-temperature environments, such as in furnaces, aerospace applications, and high-energy industrial processes.
- Excellent Thermal Conductivity: Tungsten’s high thermal conductivity ensures that tungsten wire baskets distribute heat evenly, making them ideal for applications that require precise temperature control or rapid heat dissipation.
- Corrosion and Oxidation Resistance: Tungsten wire baskets exhibit excellent resistance to corrosion and oxidation, especially in environments with high temperatures and reactive gases. This makes them suitable for use in aggressive chemical environments where other metals may degrade.
- Mechanical Strength: Tungsten is known for its high mechanical strength and durability. Tungsten wire baskets can maintain structural integrity under high stress and heavy loads, making them suitable for industrial applications where strength and resilience are paramount.
- Density and Durability: Tungsten is a dense metal, which contributes to its durability and robustness. Tungsten wire baskets are strong yet stable, capable of supporting significant weights without deforming or losing their shape.
- Biocompatibility: Tungsten is biocompatible, making it suitable for use in medical applications. Although tungsten wire baskets are not commonly used in direct contact with biological tissues, their use in medical environments (e.g., sterilization or medical devices) requires biocompatibility.
-
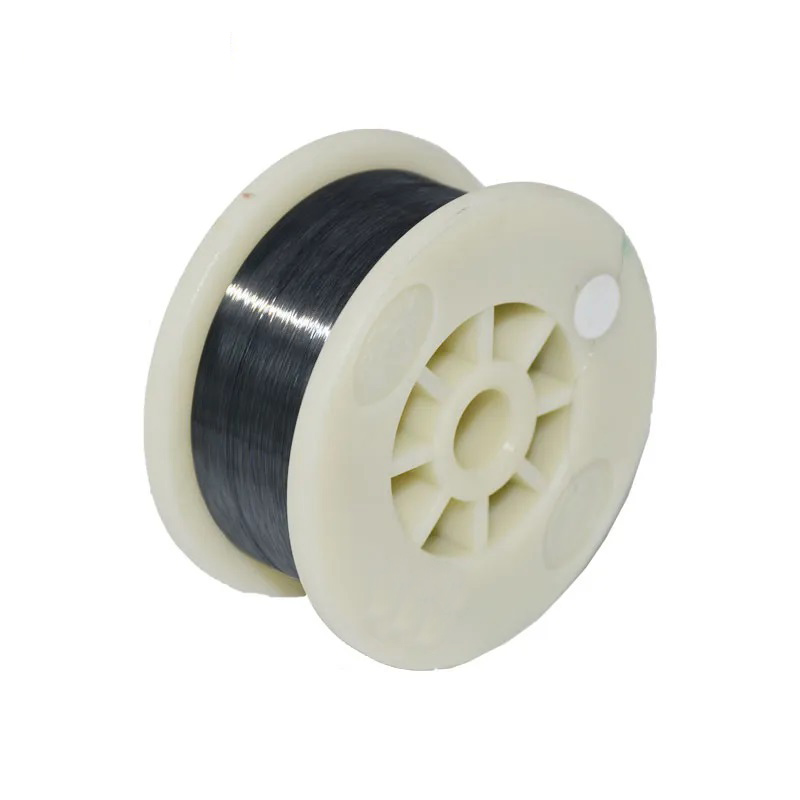
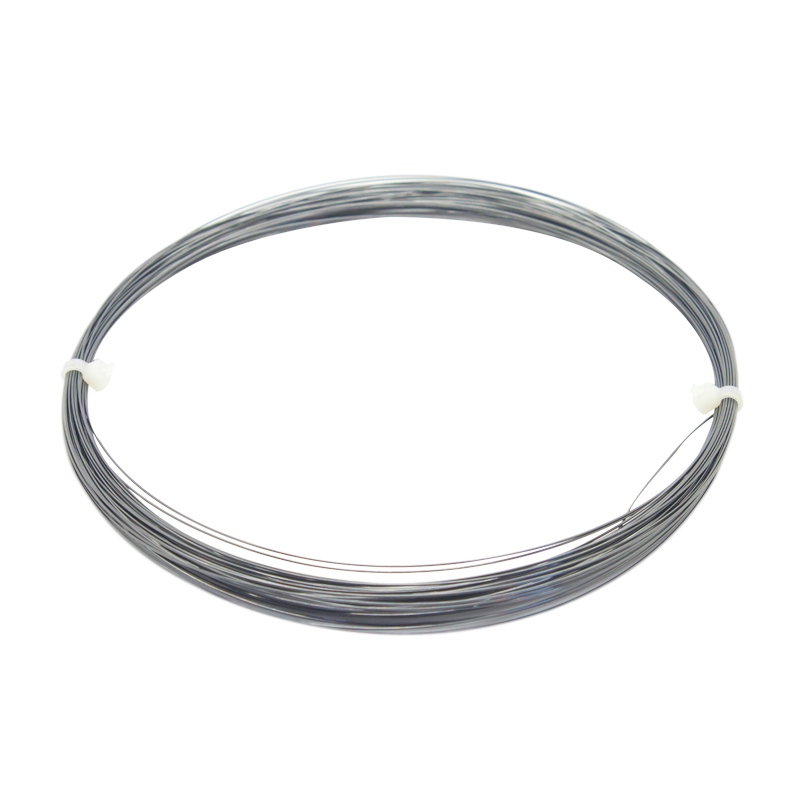
- High Melting Point: With a melting point of 3422°C, tungsten wire is ideal for applications involving extreme heat.
- Exceptional Strength: Maintains high tensile strength even at elevated temperatures.
- High Density: One of the densest metals, offering robustness and durability in demanding conditions.
- Excellent Conductivity: Provides efficient thermal and electrical conductivity for industrial and electronic applications.
- Corrosion and Oxidation Resistance: Resists chemical and environmental degradation, enhancing durability.
- Low Thermal Expansion: Maintains dimensional stability under temperature fluctuations.
- Customizability: Available in various diameters, purities, and finishes to meet diverse requirements.
-
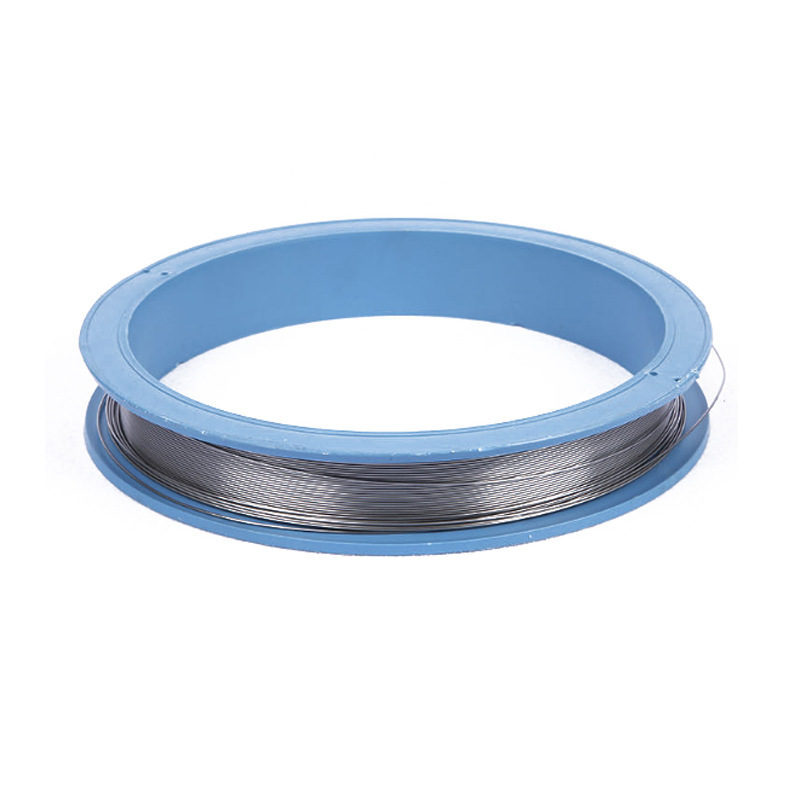
- Efficient Corrosion Protection: Widely used for anti-corrosion coatings, zinc wire prolongs the lifespan of steel and other metals in harsh environments.
- Ease of Application: Zinc wire is easily applied using thermal spray techniques or galvanizing, offering uniform and durable coatings.
- Cost-Effectiveness: Zinc wire provides a cost-effective solution for protecting structures and components compared to other anti-corrosion methods.
- Customizability: Available in various diameters and purity levels, zinc wire can be tailored to meet specific industrial needs.
- Eco-Friendly: Zinc coatings are recyclable and environmentally safe, adhering to sustainable manufacturing practices.
- Excellent Bonding Properties: Zinc wire adheres well to a variety of substrates, ensuring long-lasting and reliable coatings.