Showing 13–24 of 41 results
-
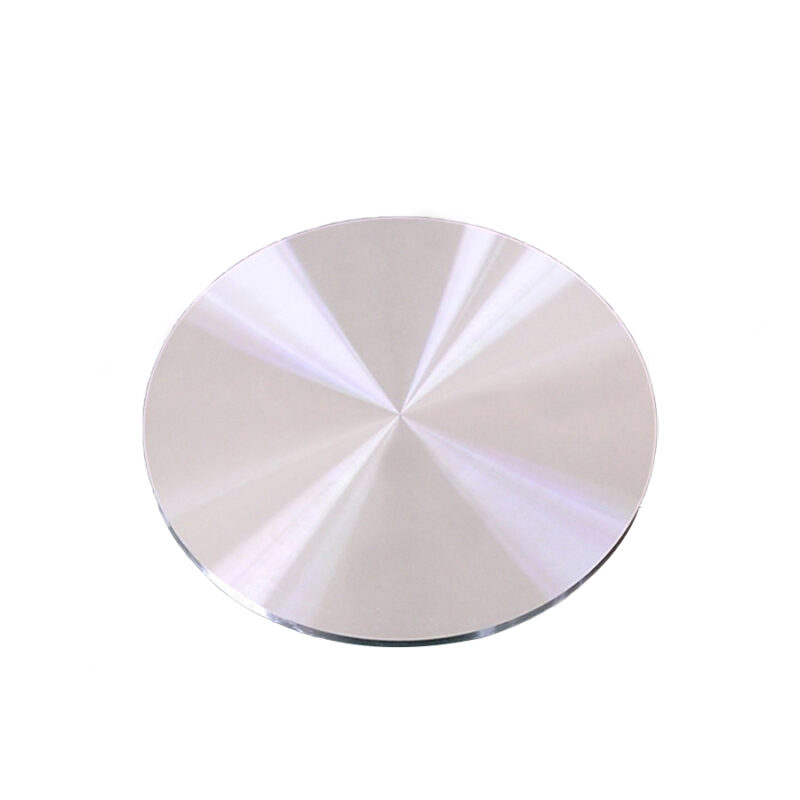
- High Solar Absorption Efficiency: CuIn alloy thin films exhibit excellent light absorption properties, contributing to the high efficiency of CIGS solar cells in converting solar energy into electricity.
- Bandgap Tunability: CuIn alloys enable tuning of the material’s bandgap to optimize its performance for specific photovoltaic applications.
- Lightweight and Flexible: CuIn-based thin-film solar panels are lightweight and flexible, making them suitable for both rigid and flexible solar panel designs.
- Thermal and Chemical Stability: The CuIn alloy demonstrates good thermal and chemical stability, ensuring durability in outdoor and harsh environmental conditions, which is essential for long-lasting solar cells.
- Customizable Composition: The ratio of copper to indium in the alloy can be adjusted to meet specific application requirements, ensuring tailored properties for different solar and electronic devices.
-
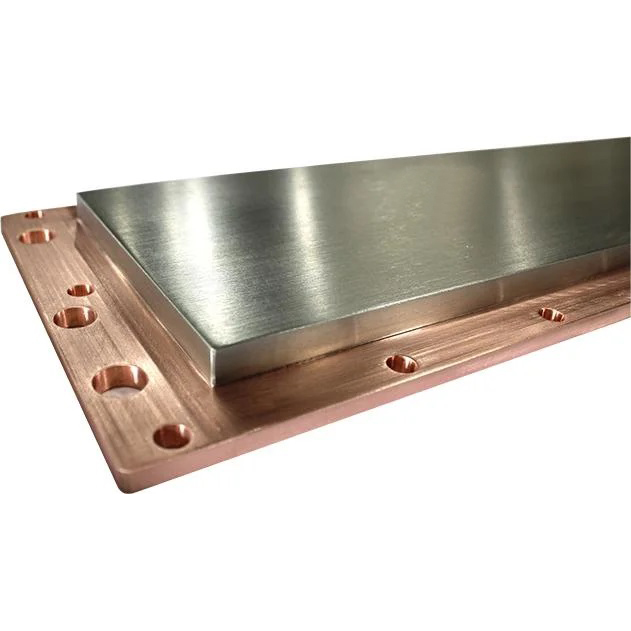
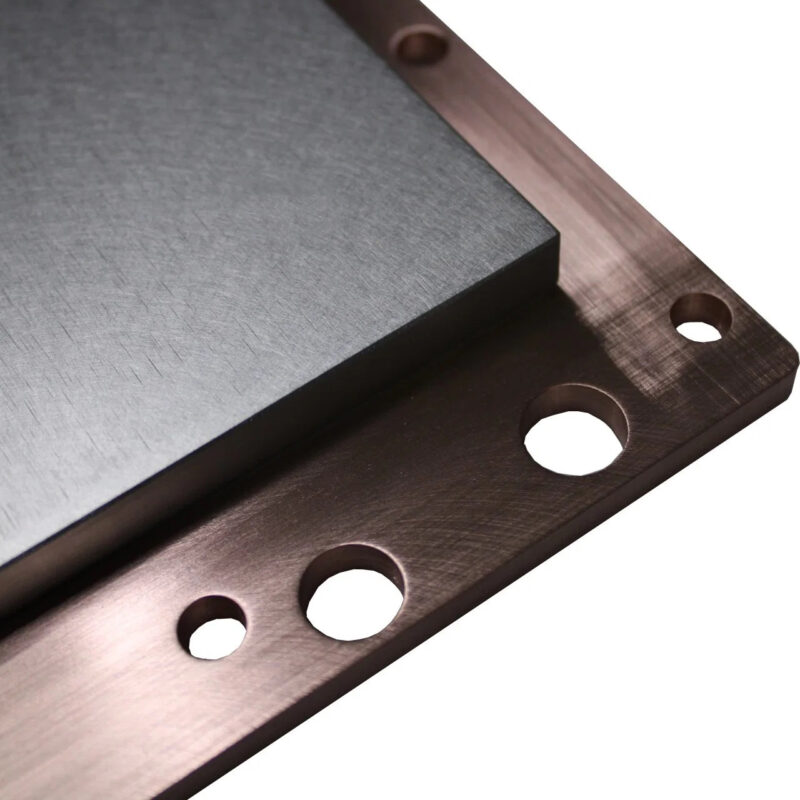
- Excellent Electrical and Thermal Conductivity: The copper base ensures superior electrical and thermal conductivity, making it ideal for electronic applications.
- Corrosion Resistance: The addition of nickel and titanium enhances the alloy’s resistance to corrosion, ensuring the longevity of thin films in harsh environments.
- High Strength and Durability: Titanium adds mechanical strength to the alloy, while nickel contributes to its hardness and wear resistance, making it suitable for demanding applications.
- Thermal Stability: CuNiTi alloys maintain their properties at elevated temperatures, making them ideal for high-temperature processes and environments.
- Customizable Properties: The ratio of copper, nickel, and titanium can be adjusted to tailor the alloy’s specific properties for a wide range of applications.
-
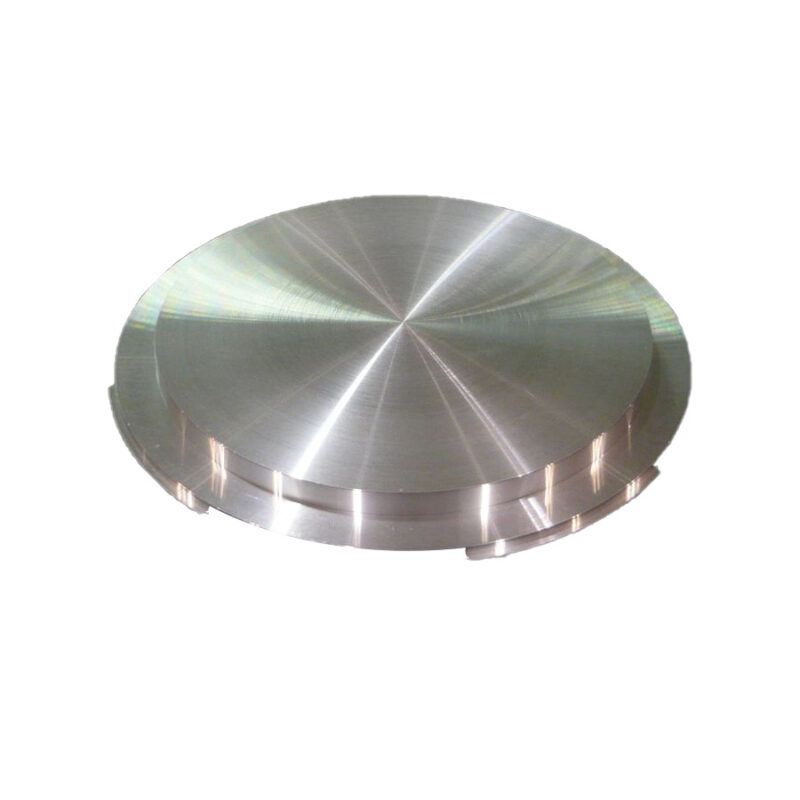
- High Entropy Alloy: The near-equal combination of five elements offers unique mechanical and thermal properties, including high strength, excellent wear resistance, and thermal stability.
- Corrosion Resistance: The alloy’s thin films offer exceptional resistance to oxidation and corrosion, even in harsh environments.
- Magnetic Properties: FeCoCrNiMn alloy sputtering targets produce films with strong magnetic properties, ideal for magnetic and electronic devices.
- Customizable Size and Shape: FeCoCrNiMn alloy sputtering targets are available in discs, plates, or custom shapes to meet the requirements of different deposition systems.
-
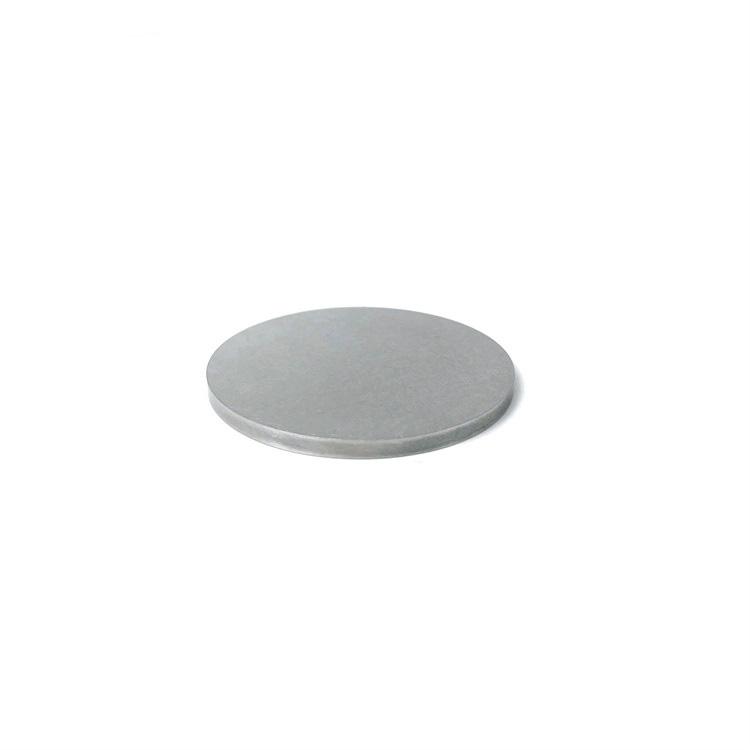
- High Magnetic Saturation: The FeCoTa alloy offers excellent magnetic properties, including high magnetic saturation and low coercivity, making it ideal for use in data storage devices and other applications requiring strong and stable magnetic fields.
- Thermal Stability: The addition of tantalum enhances the alloy’s thermal stability, allowing FeCoTa thin films to perform reliably in high-temperature environments, such as aerospace and power electronics.
- Wear Resistance: Tantalum in the alloy also contributes to increased wear resistance, ensuring that the thin films maintain their integrity under mechanical stress and prolonging their lifespan.
- Corrosion Resistance: The alloy exhibits good resistance to corrosion, making it suitable for applications in harsh or outdoor environments.
- Customizable Composition: The ratio of Fe, Co, and Ta can be adjusted to optimize magnetic and physical properties for specific applications.
-
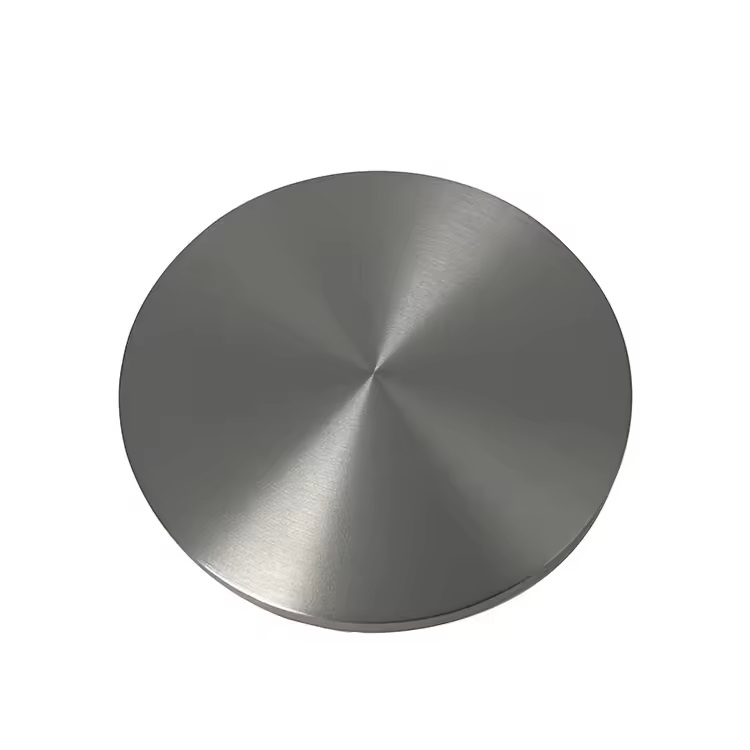
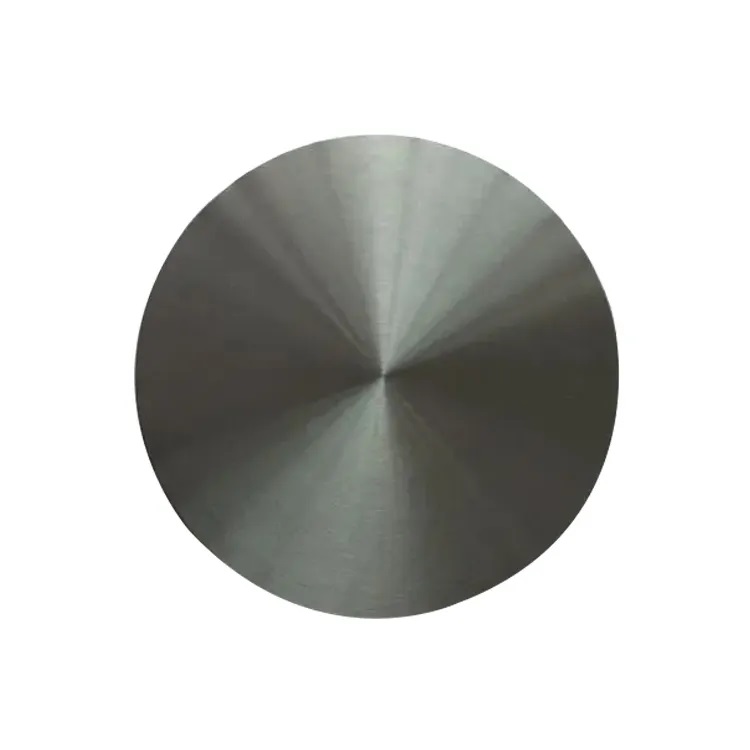
- Corrosion Resistance: The high chromium content in FeCr alloys provides excellent resistance to corrosion, making the alloy ideal for environments exposed to moisture, chemicals, or harsh conditions.
- Magnetic Properties: FeCr alloys offer stable magnetic properties, making them suitable for use in various magnetic storage and electronic devices.
- High-Temperature Stability: FeCr thin films maintain their mechanical strength and performance even at elevated temperatures, making them useful for applications in energy, aerospace, and other industries requiring heat-resistant coatings.
- Wear Resistance: The wear resistance of FeCr thin films ensures long-lasting durability for coated components, reducing wear and tear in mechanical systems and industrial tools.
- Customizable Composition: The ratio of iron to chromium can be adjusted to optimize the properties such as corrosion resistance, magnetic performance, or wear resistance, based on the application’s specific requirements.
-
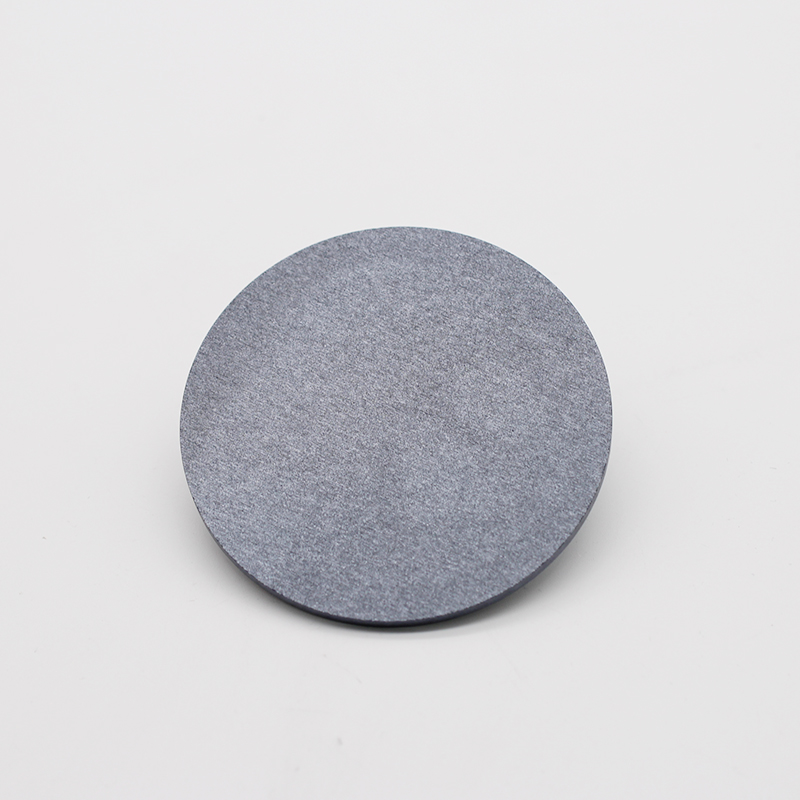
- High Magnetostriction: FeGa alloys exhibit superior magnetostrictive properties, providing enhanced performance in functional films.
- Customizable Compositions: Available in various iron-gallium ratios to meet specific application requirements.
- High Purity: Ensures consistent and reliable thin-film deposition with minimal contamination.
- Excellent Magnetic Properties: Combines strength and magnetic responsiveness for advanced thin-film applications.
- Durable and Stable: Provides robust and long-lasting performance in challenging environments.
-
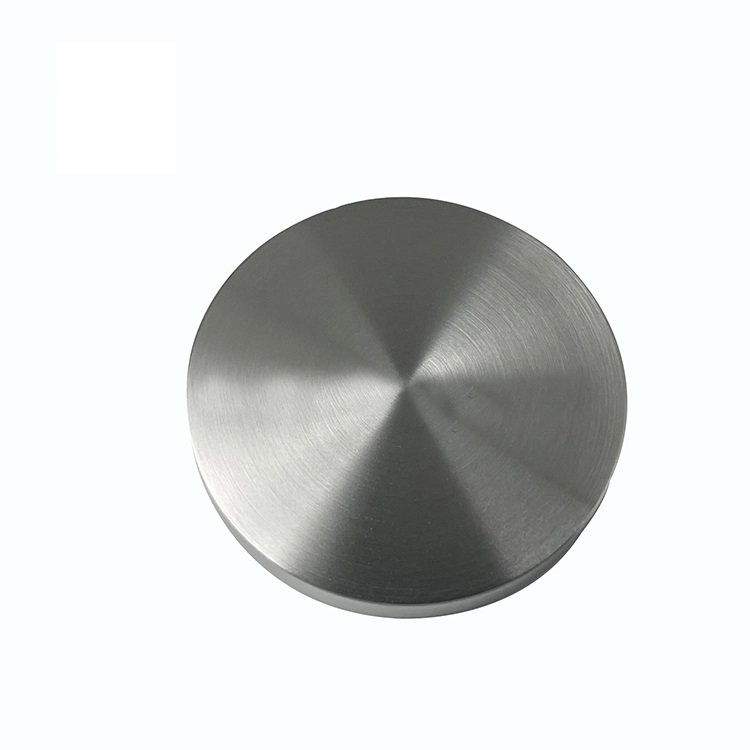
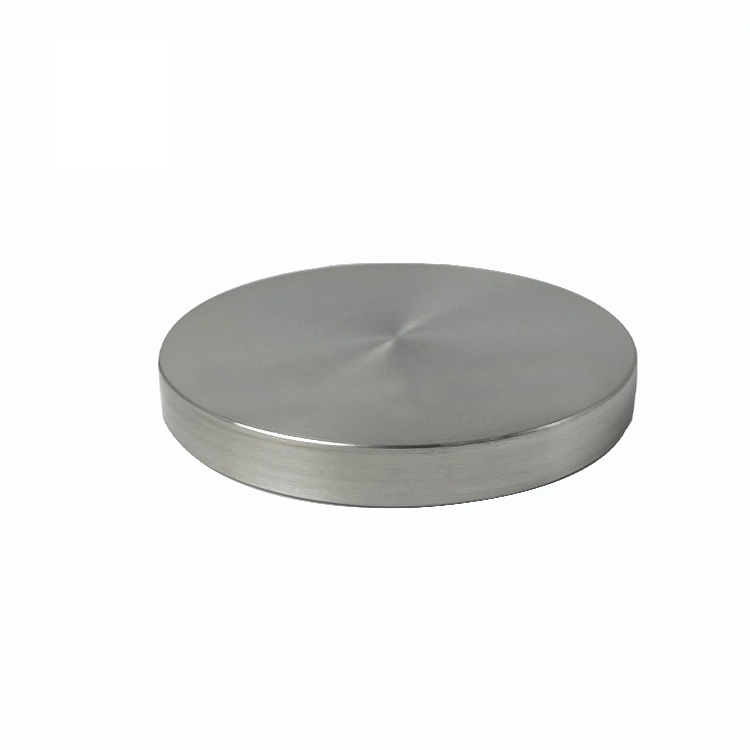
- Magnetic Stability: FeHf alloys offer stable magnetic properties that make them suitable for use in a variety of magnetic devices, especially in high-temperature or harsh environments.
- Oxidation Resistance: The addition of hafnium significantly improves the alloy’s resistance to oxidation, making FeHf thin films suitable for applications exposed to elevated temperatures and oxidative conditions.
- High Strength: FeHf alloy thin films provide excellent mechanical strength, ensuring long-term durability and reliability in high-stress environments.
- Thermal Stability: FeHf alloys maintain their structural integrity and performance even at high temperatures, making them ideal for applications in electronics, aerospace, and industrial settings.
- Corrosion Resistance: The alloy’s resistance to corrosion allows it to perform well in harsh environments, protecting components from degradation due to moisture, chemicals, and other corrosive elements.
-
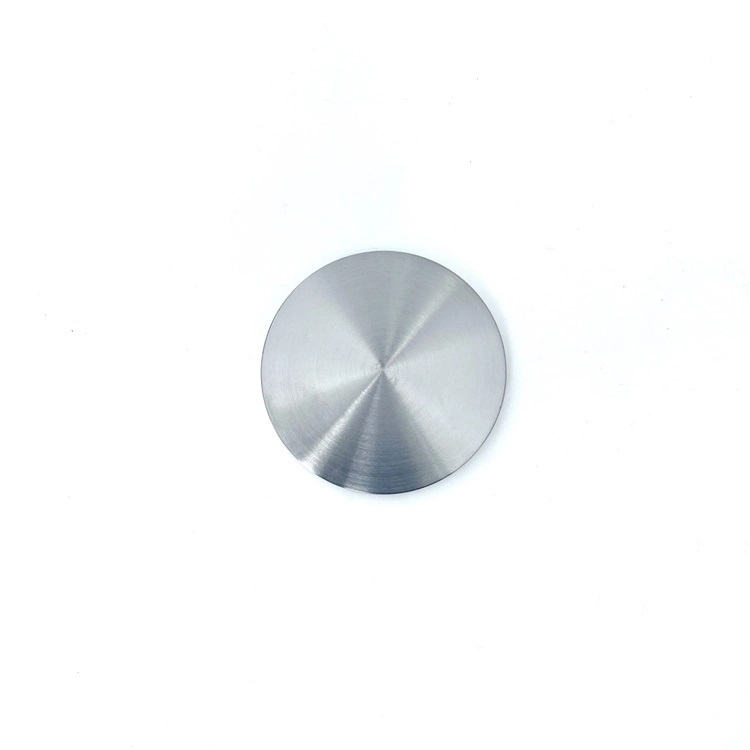
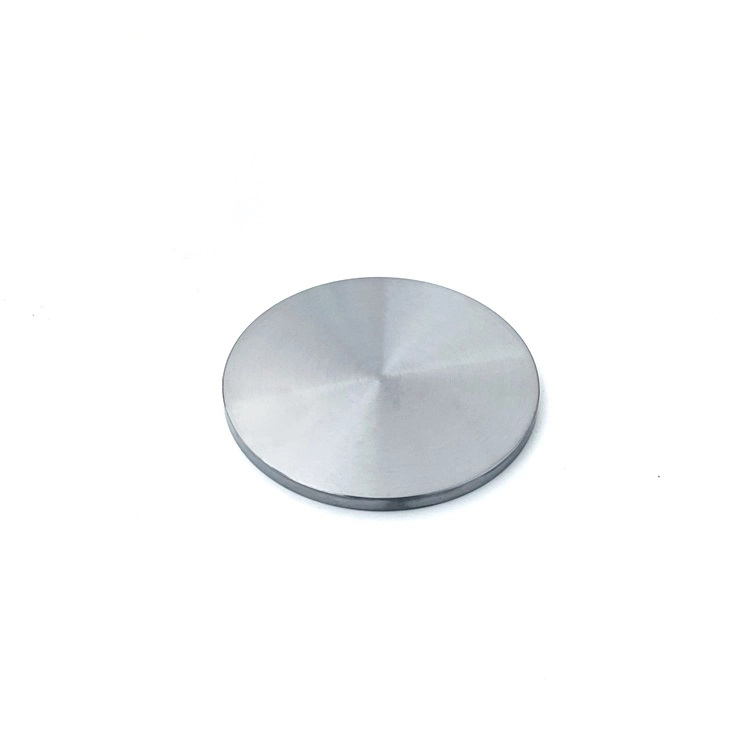
- Magnetic Properties: FeMn alloys exhibit useful magnetic properties, including antiferromagnetism, which makes them suitable for use in a variety of magnetic devices, sensors, and memory technologies.
- Corrosion Resistance: The alloy provides excellent resistance to corrosion, making it ideal for use in environments exposed to moisture, chemicals, and other corrosive agents.
- Wear Resistance: FeMn alloy thin films enhance the wear resistance of components, making them more durable under mechanical stress and wear, especially in industrial and mechanical applications.
- Customizable Composition: The ratio of iron to manganese can be adjusted to tailor the magnetic, mechanical, and corrosion-resistant properties of the thin films for specific applications.
- High Strength: FeMn thin films exhibit high mechanical strength, making them ideal for applications where both durability and protection are required, especially in harsh environments.
-
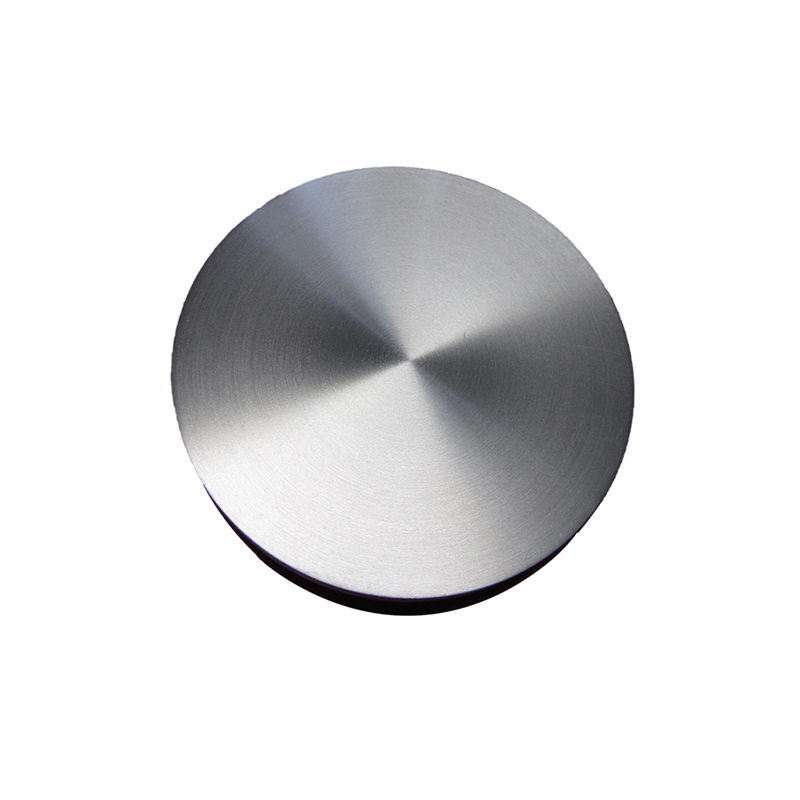
- Antiferromagnetic Properties: IrMn alloy thin films exhibit strong antiferromagnetic behavior, which is essential for magnetic pinning in spintronic devices and memory storage.
- High Corrosion Resistance: Iridium provides excellent corrosion resistance, ensuring the durability and longevity of the deposited thin films, even in harsh environments.
- Thermal Stability: IrMn alloy films are thermally stable, making them ideal for high-temperature applications in electronic and magnetic devices.
- Customizable Size and Shape: IrMn sputtering targets are available in various sizes and shapes, including discs, plates, and custom geometries, to suit a wide range of deposition systems.
-
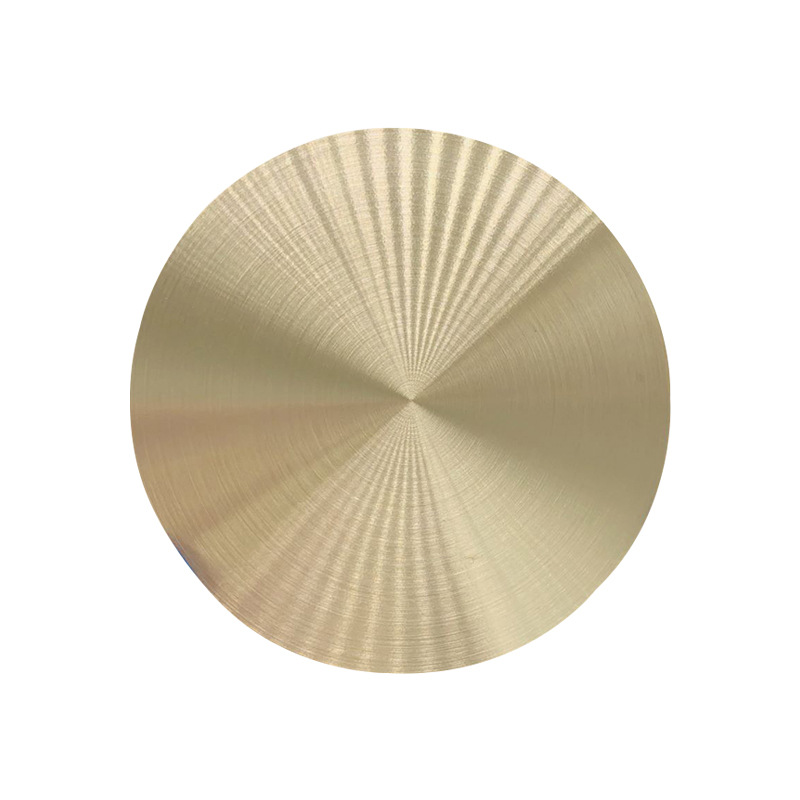
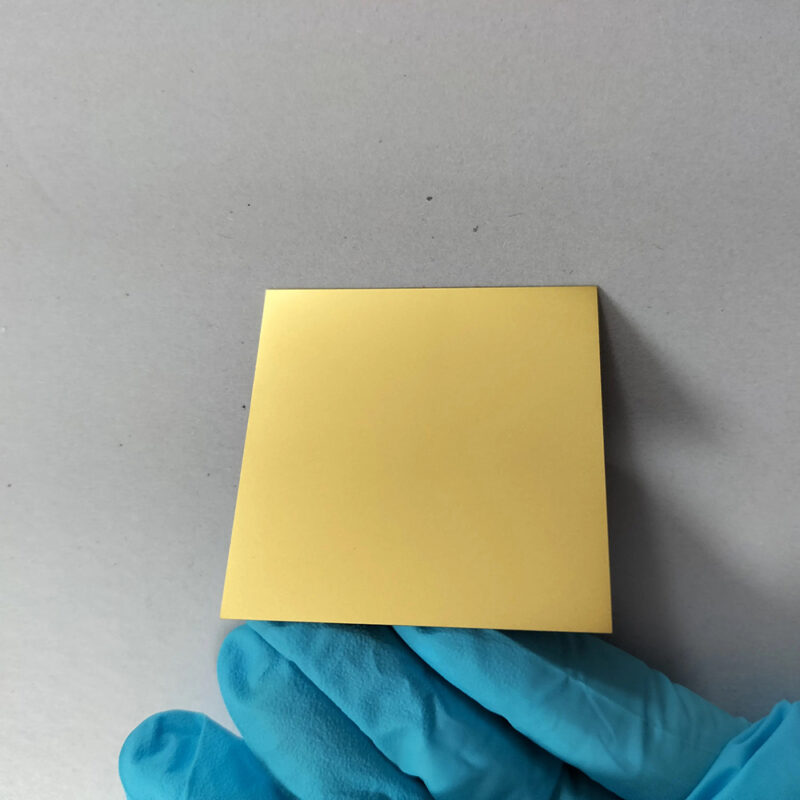
- High Thermal Conductivity: Copper’s excellent thermal conductivity ensures effective heat dissipation in thin-film coatings, crucial for applications in electronics and thermal management systems.
- Mechanical Strength: Molybdenum contributes strength and rigidity to the MoCu alloy, ensuring mechanical stability in high-temperature and high-stress applications.
- Corrosion Resistance: The MoCu alloy provides good resistance to corrosion, making it suitable for use in environments where materials are exposed to moisture, chemicals, or harsh conditions.
- Low Thermal Expansion: The alloy’s combination of molybdenum and copper results in low thermal expansion, reducing the risk of film cracking or damage under thermal stress.
- Customizable Composition: The ratio of molybdenum to copper can be tailored to optimize the thermal, electrical, and mechanical properties to meet specific application requirements.
-
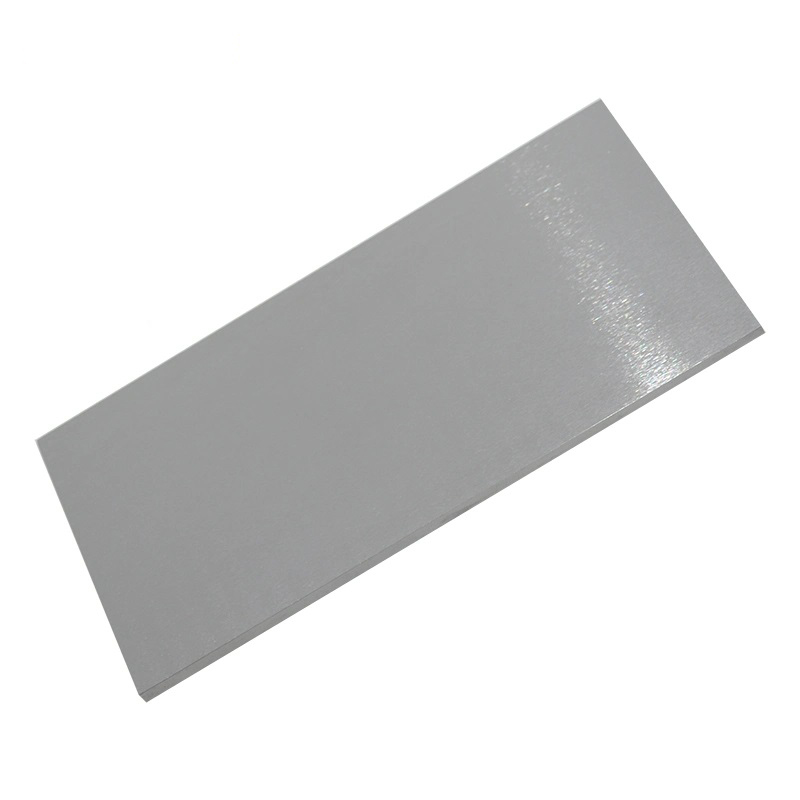
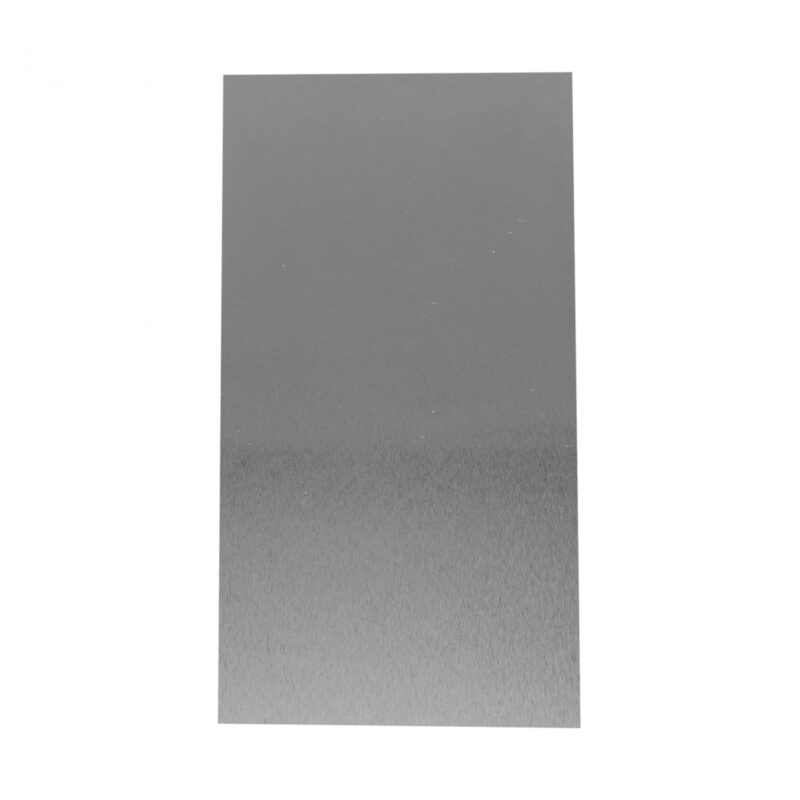
- High Thermal Stability: The MoLa alloy has excellent resistance to deformation and oxidation at high temperatures, ensuring reliability in demanding thermal environments.
- Enhanced Ductility: The addition of lanthanum oxide improves the ductility of molybdenum, making the alloy easier to process and form into thin films without compromising its strength.
- Oxidation Resistance: MoLa exhibits outstanding resistance to oxidation, especially at elevated temperatures, providing long-term stability and durability.
- Improved Machinability: The lanthanum content enhances the machinability of molybdenum, allowing for more precise fabrication of sputtering targets and thin-film coatings.
-
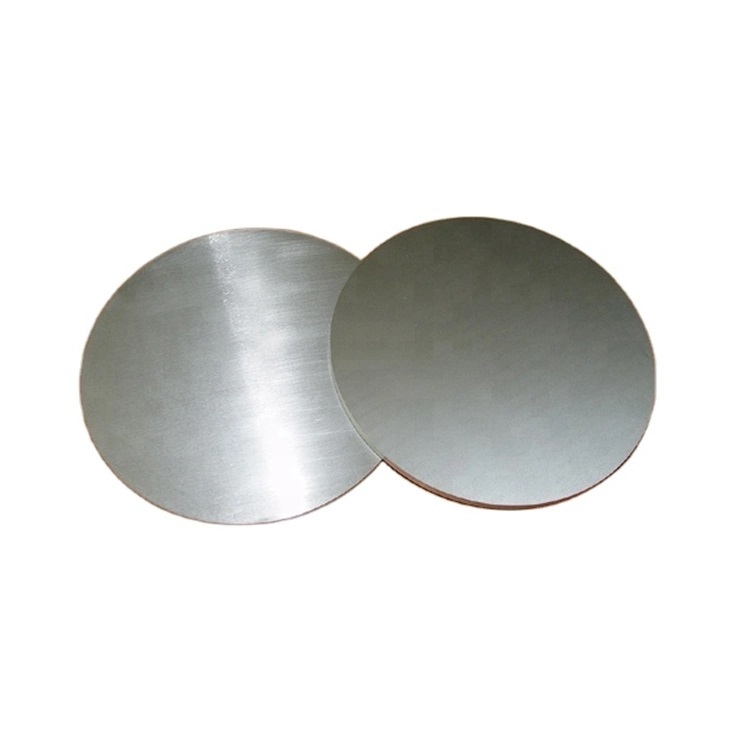
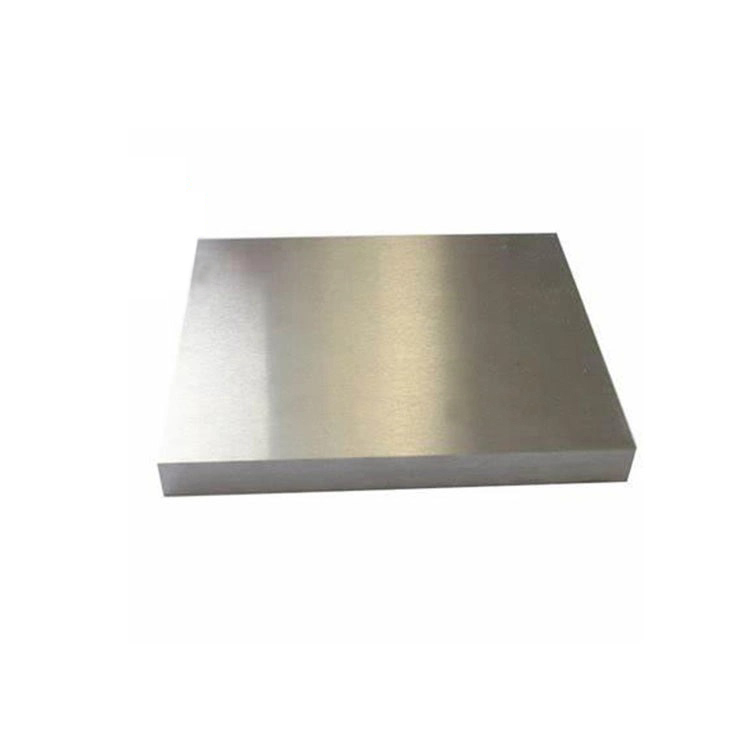
- High Mechanical Strength: The combination of molybdenum and niobium results in an alloy with high tensile strength, making it suitable for demanding structural applications.
- Thermal Stability: MoNb alloys maintain their mechanical properties at elevated temperatures, making them ideal for high-temperature applications, such as coatings for turbine components.
- Corrosion Resistance: The alloy exhibits excellent resistance to oxidation and corrosion, ensuring long-term performance in harsh environments.
- Low Density: Compared to pure molybdenum, the addition of niobium reduces the density of the alloy, enhancing its performance in weight-sensitive applications.
- Customizable Composition: The molybdenum-to-niobium ratio can be tailored to optimize the properties of the alloy for specific applications, whether enhancing strength, thermal stability, or corrosion resistance.