Showing 1–12 of 30 results
-
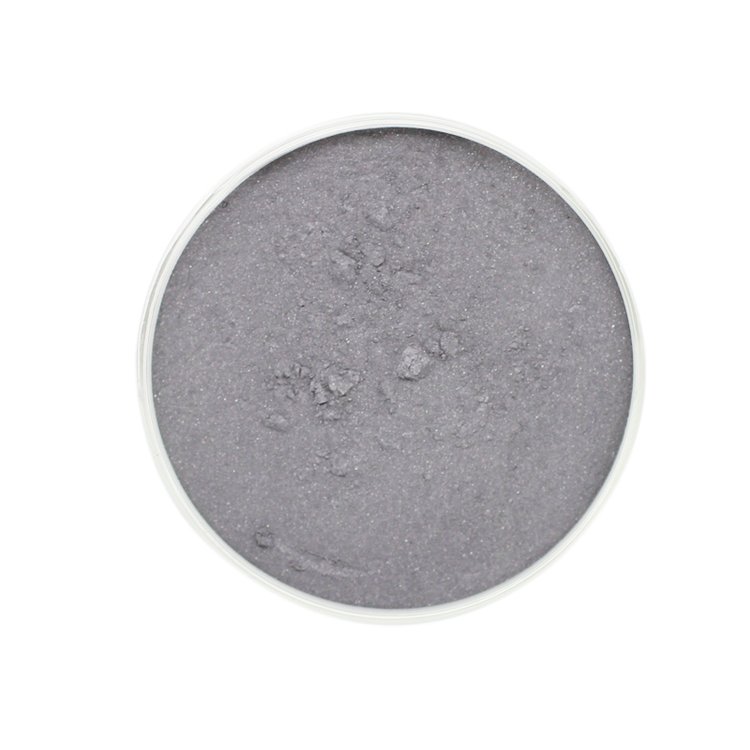
- Extreme Hardness: Mohs hardness of 9.5, second only to diamond and cubic boron nitride.
- Low Density: Lightweight material ideal for aerospace and defense applications.
- High Thermal Stability: Exceptional performance at high temperatures.
- Chemical Inertness: Resistant to most acids and alkalis.
- Superior Wear Resistance: Ideal for abrasive and protective applications.
- Customizable Particle Sizes: Nano (<100 nm) and micro (1–50 µm) grades available or customized.
-
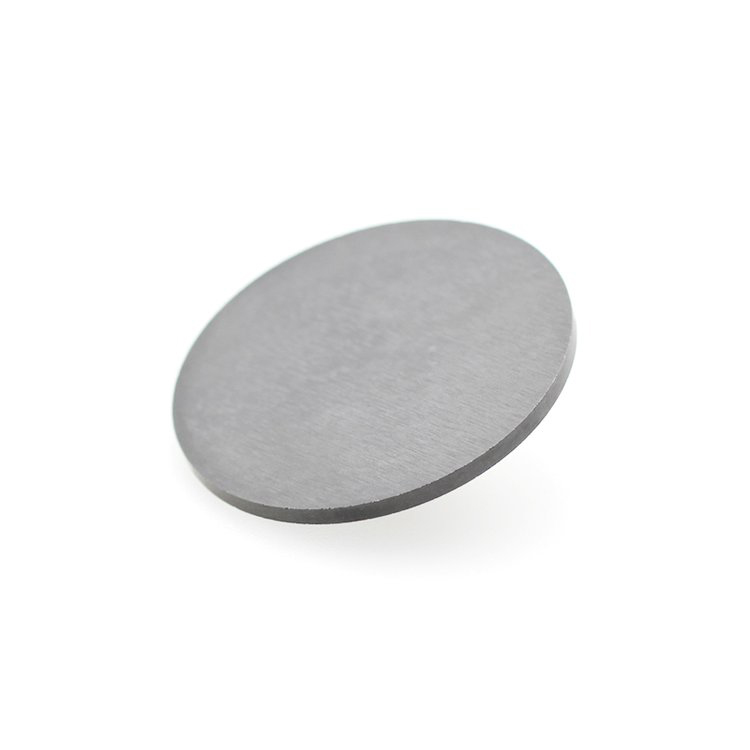
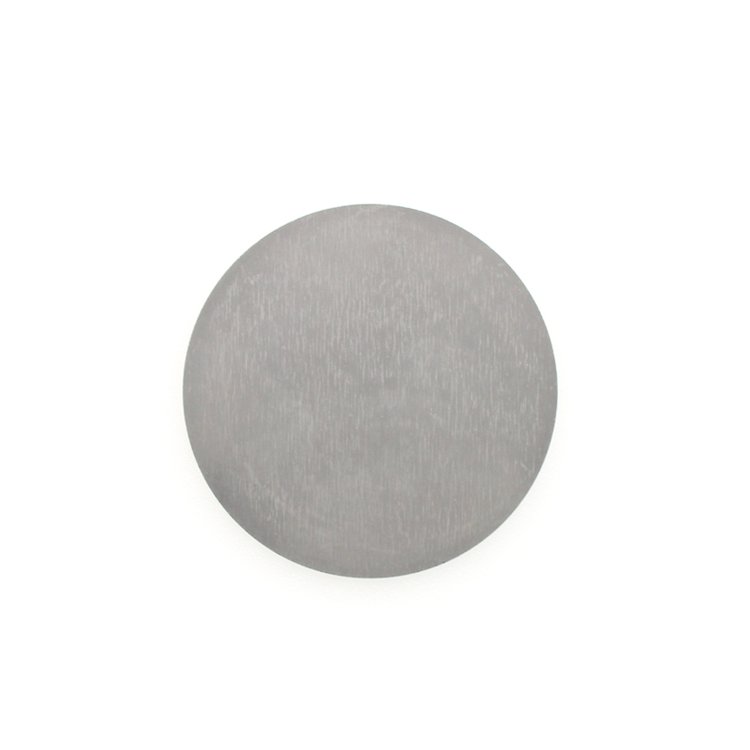
- Exceptional Hardness: High resistance to wear and abrasion.
- Chemical Stability: Resistant to acids and alkalis, ensuring longevity in extreme environments.
- Lightweight: Facilitates applications where low weight is critical.
- High Purity: Delivers superior film quality and consistency.
-
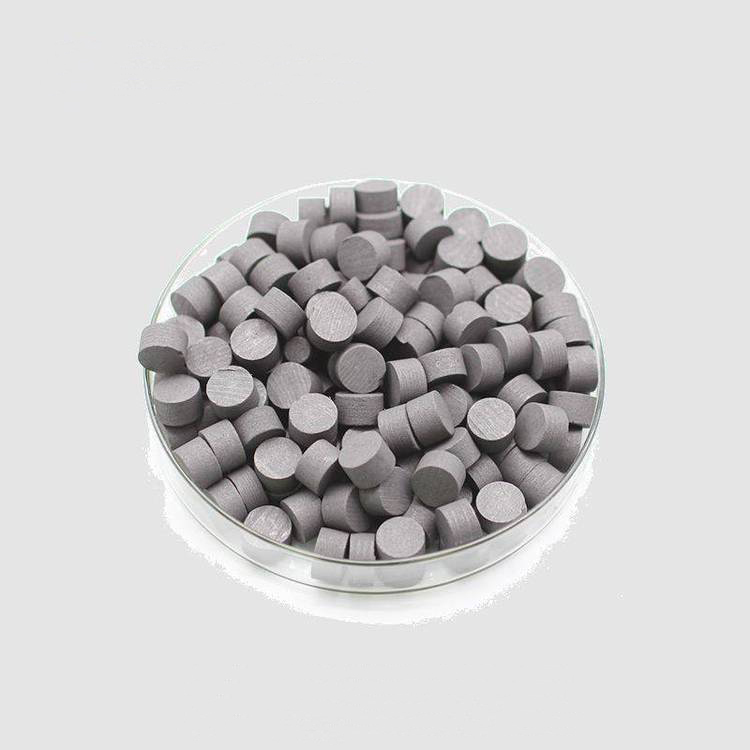
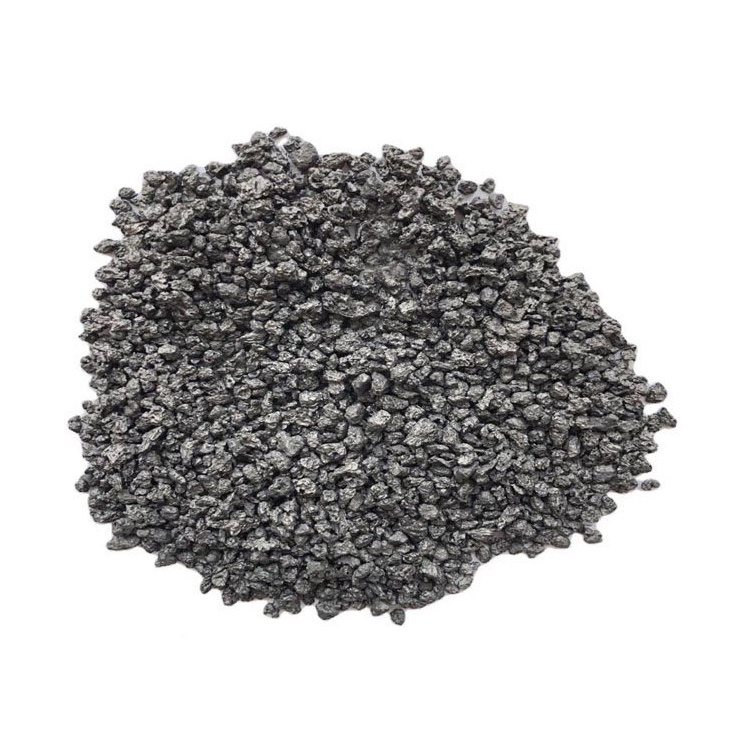
- High Hardness: Carbon, especially in its diamond-like form, is extremely hard and wear-resistant, making it suitable for protective coatings.
- High Melting Point: Sublimation point of carbon is around 3,650°C, allowing its use in high-temperature deposition processes.
- Good Electrical Conductivity: Carbon is conductive, making it suitable for electronic applications.
- Chemically Inert: Carbon’s chemical stability ensures it remains durable in corrosive environments, enhancing the lifespan of coated materials.
- Low Coefficient of Friction: Diamond-like carbon (DLC) films offer excellent lubricity and are used to reduce wear in mechanical systems.
-
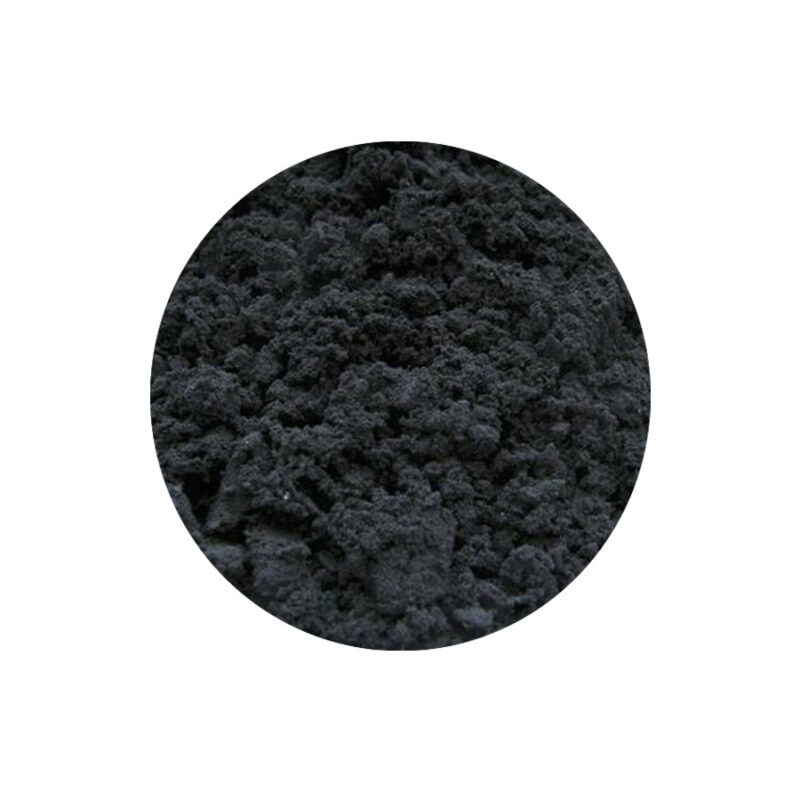
- High Electrical Conductivity: Especially in the form of graphite, carbon powder is widely used in applications requiring good electrical conduction.
- Thermal Stability: Carbon is highly resistant to heat and can withstand extreme temperatures, making it ideal for refractory and high-temperature applications.
- Lubrication: Graphite powder acts as a dry lubricant, reducing wear and friction between moving parts under high temperature conditions.
- Chemical Inertness: Carbon is resistant to many chemicals, which makes it suitable for use in harsh environments where it will not react or degrade easily.
- Adsorption: Activated carbon has exceptional adsorption capabilities, making it effective in filtration and environmental clean-up applications.
- Reinforcement: Carbon black provides strength and durability when added to materials such as rubber and plastics.
-
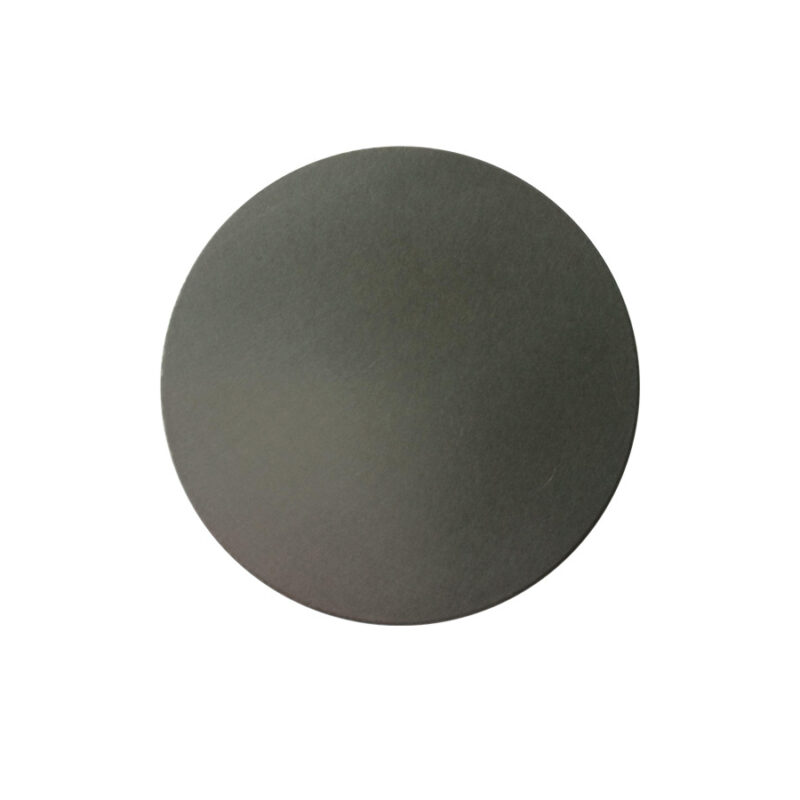
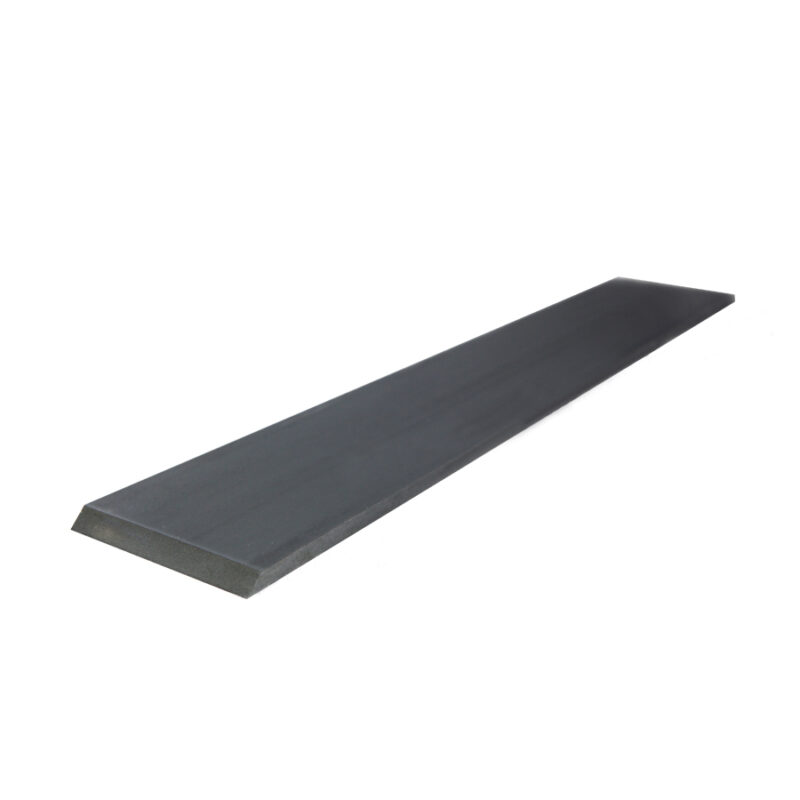
- Purity: Graphite sputtering targets are available in high purity (typically 99.9% or higher) to ensure optimal film quality, especially in semiconductor and energy storage applications.
- High Conductivity: Graphite offers excellent electrical conductivity, making it suitable for thin films in electronic components.
- Thermal Stability: Graphite can withstand high temperatures, making it ideal for applications in high-heat environments.
- Chemical Resistance: Graphite is resistant to many chemicals, enabling its use in corrosive environments and protective coatings.
- Customizable Size and Shape: Available in various forms, such as discs, plates, and custom shapes to fit specific deposition systems.
-
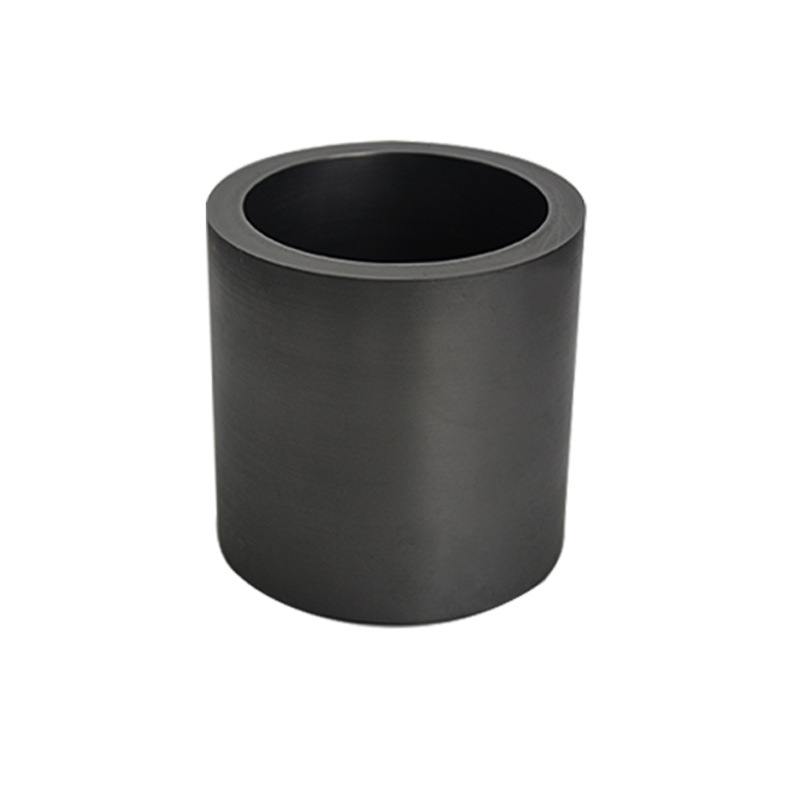
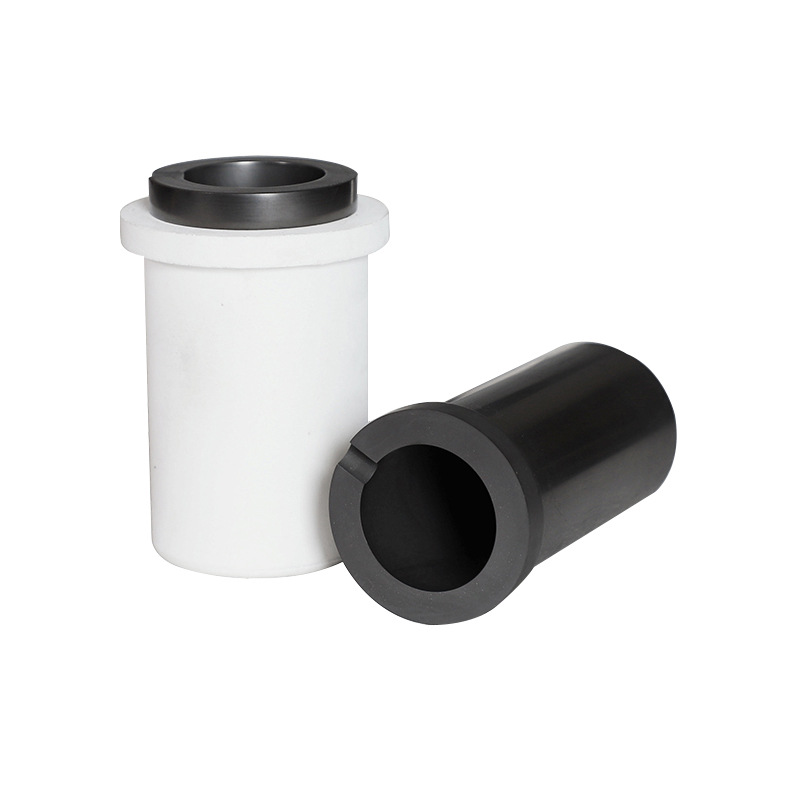
- Outstanding thermal and chemical stability at high temperatures
- Excellent thermal conductivity for uniform heating
- Resistant to thermal shock and capable of rapid temperature changes
- Low reactivity and non-wetting with most metals, minimizing contamination
- Available in a range of shapes and sizes to accommodate various industrial needs
-
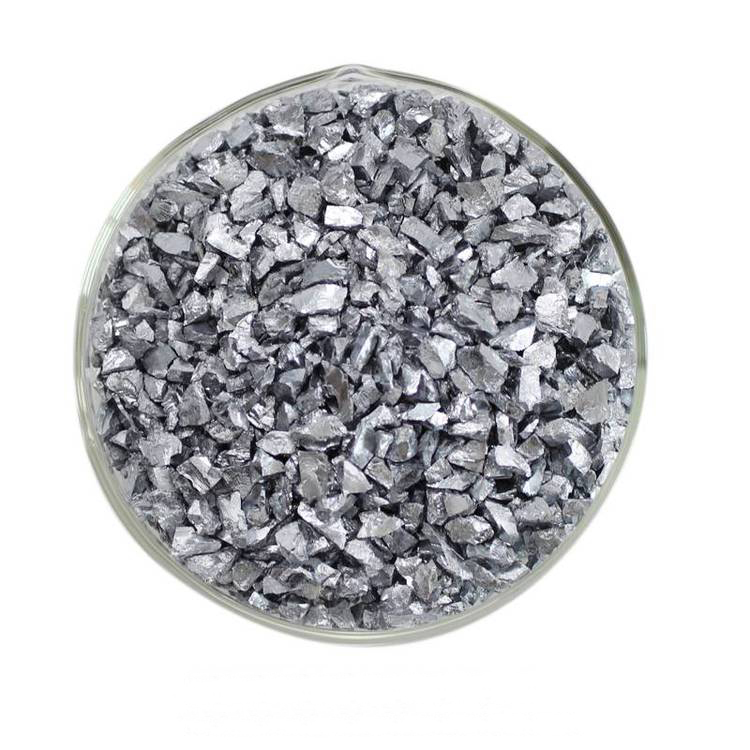
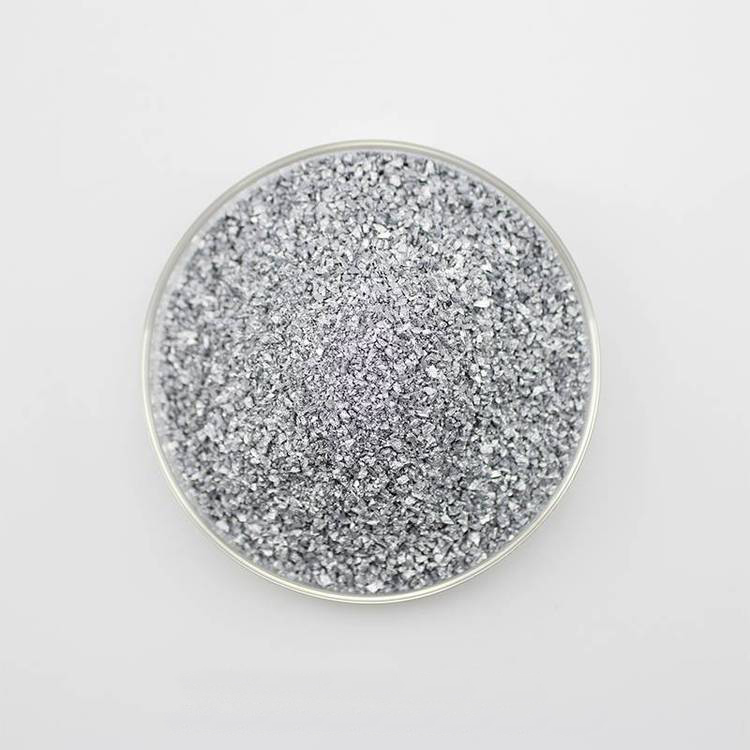
- High purity (≥99.5%).
- Exceptional hardness and wear resistance.
- Superior thermal and chemical stability.
- Consistent pellet size for uniform performance.
- Customizable specifications for diverse industrial applications.
-
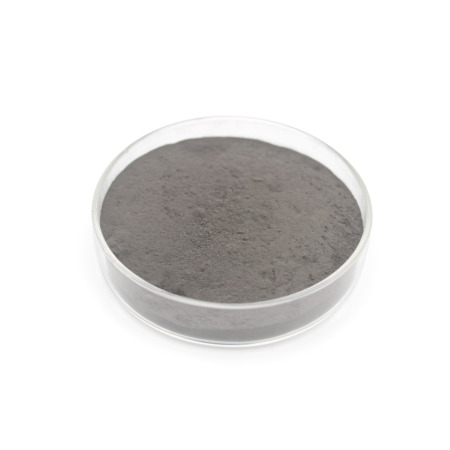
- High Hardness: Cr3C2 offers excellent wear resistance and high hardness, making it ideal for abrasive applications.
- High Thermal Stability: With a melting point of 2,480°C, it retains its strength and properties even at elevated temperatures.
- Corrosion Resistance: Chromium carbide is highly resistant to oxidation and corrosion, ideal for harsh, high-temperature environments.
- Excellent Wear Resistance: Offers superior resistance to friction and abrasion, ideal for applications where surfaces experience intense wear.
- Versatile Applications: Used in coatings, composite materials, and hardfacing to improve the longevity and durability of components.
-
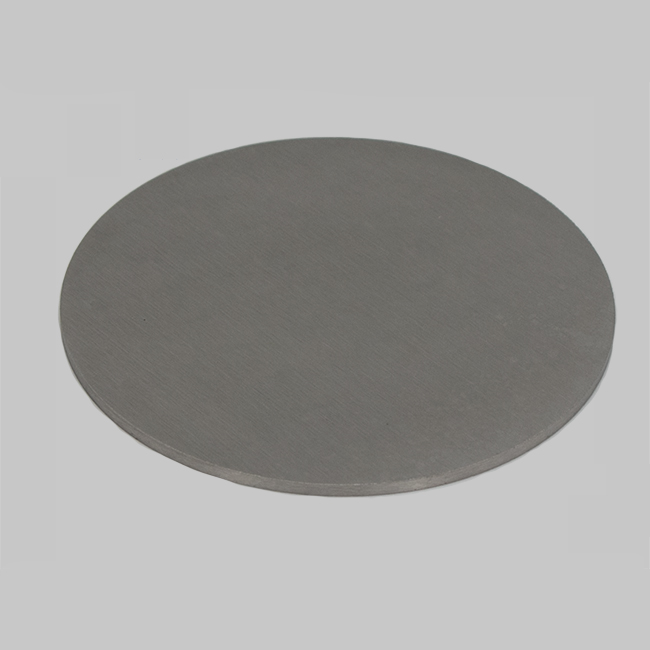
- Exceptional Hardness: Ensures long-lasting and wear-resistant coatings.
- High Corrosion Resistance: Protects against oxidation and chemical exposure.
- Thermal Stability: Reliable performance in high-temperature conditions.
- High Purity: Supports defect-free deposition for critical applications.
- Versatile Applications: Applicable in multiple industries, including aerospace and automotive.
-
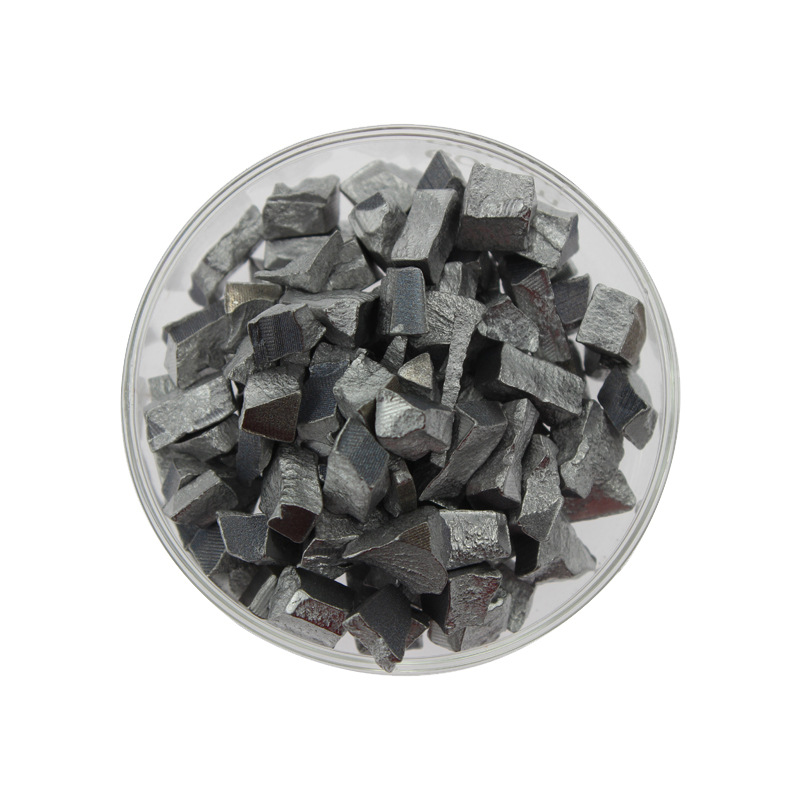
- High Hardness: Provides excellent wear resistance, making it suitable for demanding applications.
- Thermal Stability: Maintains structural integrity under high-temperature conditions.
- Customizable Composition: The carbon content can be adjusted to optimize properties for specific applications.
-
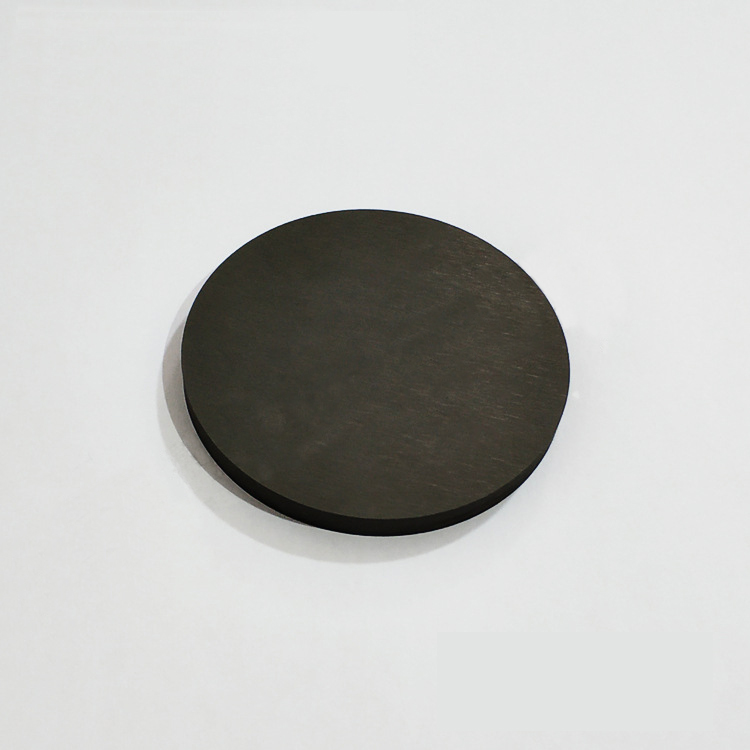
- High Purity: Available in purities of 99.5% or higher to ensure optimal film quality.
- Thermal Stability: Exceptional resistance to high temperatures and thermal stress.
- Mechanical Strength: High hardness and excellent wear resistance.
- Oxidation Resistance: Stable in extreme environments.
-
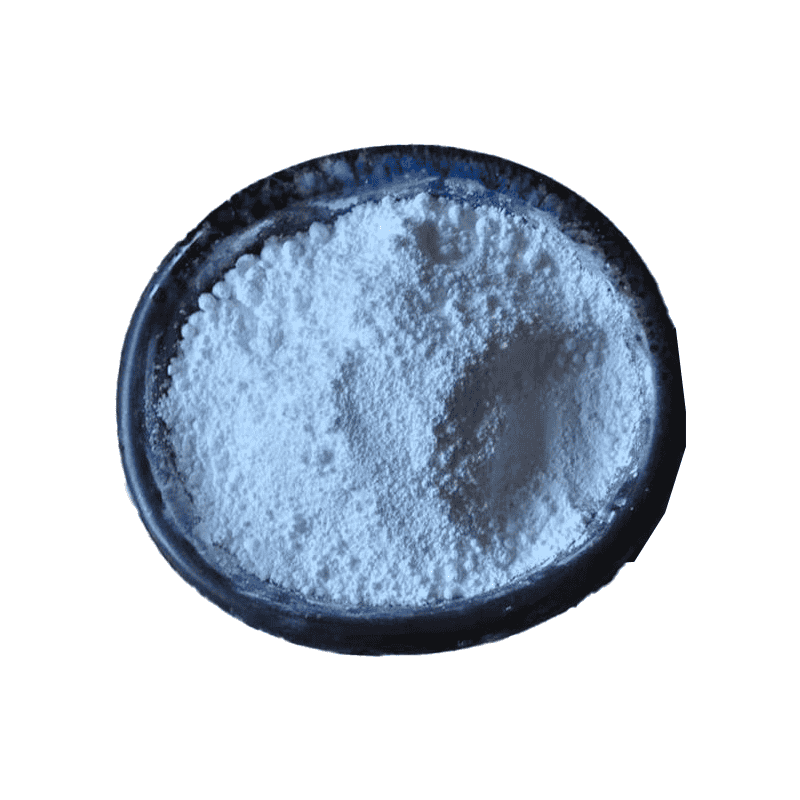
- High-Temperature Strength: Retains superior mechanical properties at elevated temperatures, ensuring long-term reliability in harsh conditions.
- Oxidation and Corrosion Resistance: Exceptional resistance to oxidation and corrosion, even in extreme high-temperature environments.
- Excellent Castability: Ideal for casting applications due to its excellent moldability and resistance to thermal fatigue.
- Versatile Manufacturing: Compatible with additive manufacturing, powder metallurgy, and traditional casting methods.
- High-Precision Components: Suitable for applications that require high-performance parts with precision and minimal defects.