Showing 13–24 of 29 results
-
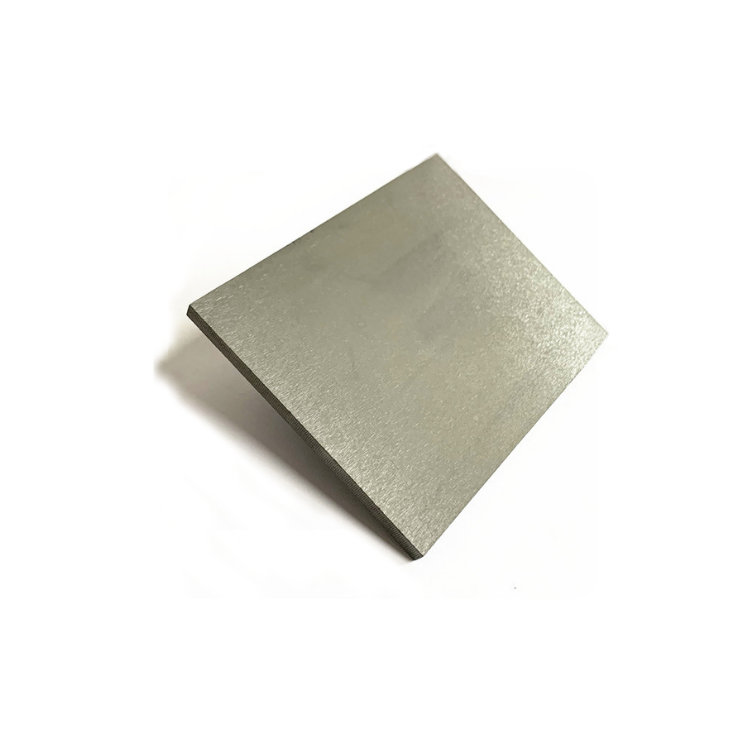
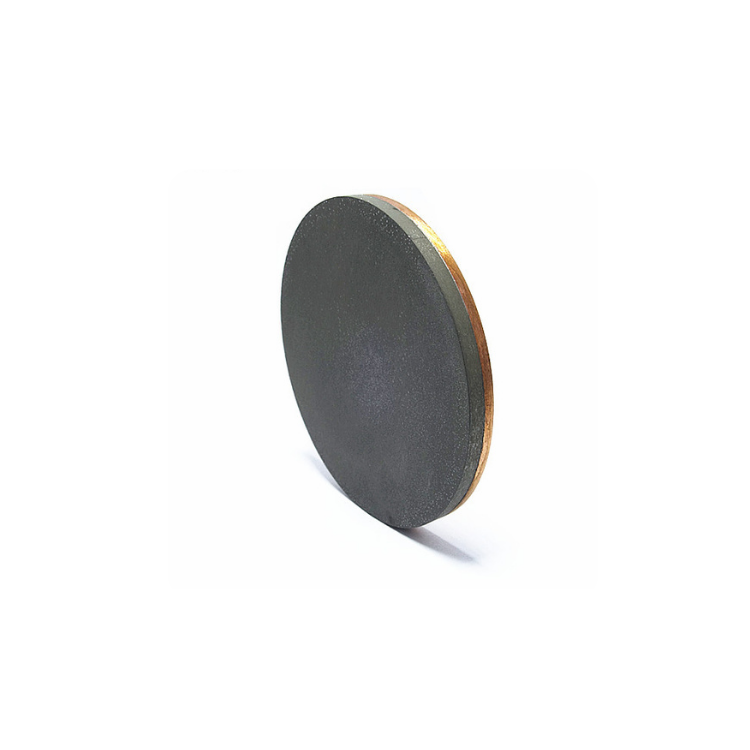
- High purity: Ensures superior film quality with minimal contamination.
- Outstanding hardness: Provides durability for mechanical applications.
- Thermal stability: Ideal for high-temperature environments.
- Customizable dimensions: Available in a variety of sizes, shapes, and thicknesses to meet specific project requirements.
- High deposition efficiency: Optimized for uniform thin-film production.
-
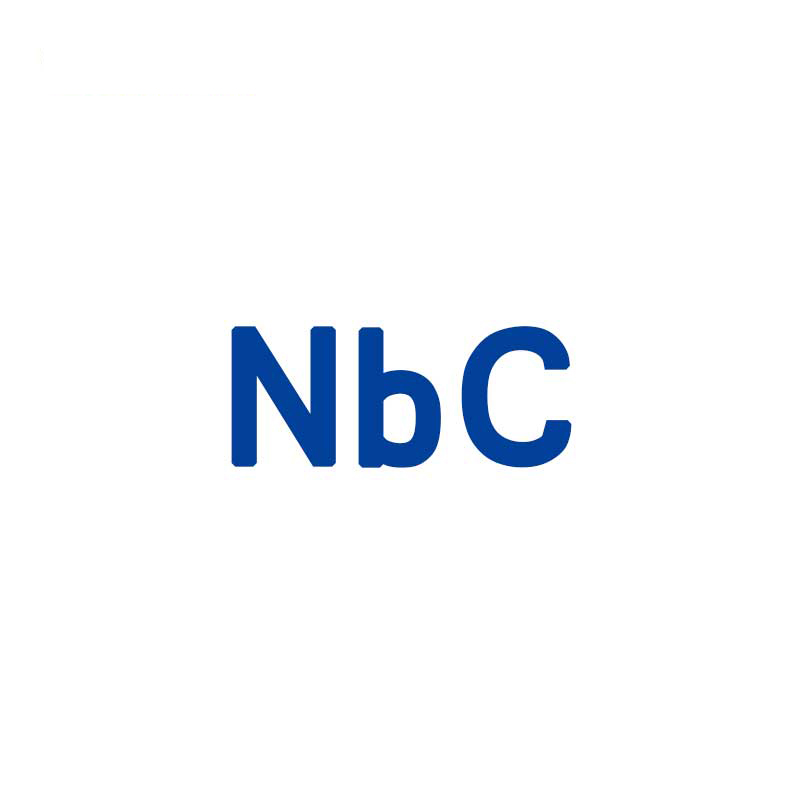
- High Hardness: Ensures durability and wear resistance in coatings.
- Thermal Stability: Withstands high-temperature processes without degradation.
- Corrosion Resistance: Provides protection in harsh environments.
- Customizable: Available in various sizes, purities, and configurations to meet specific requirements.
-
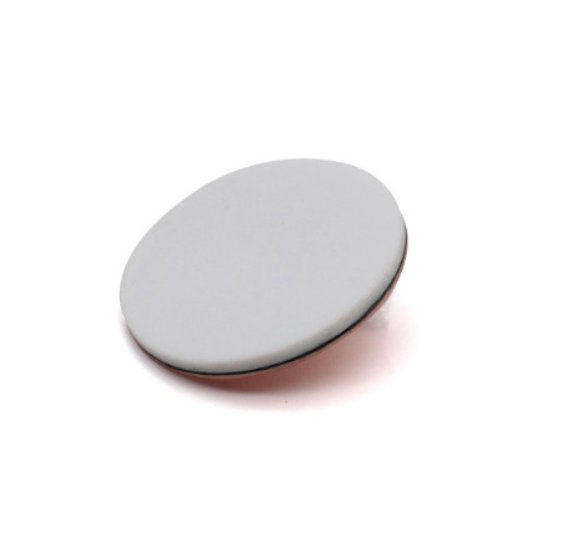
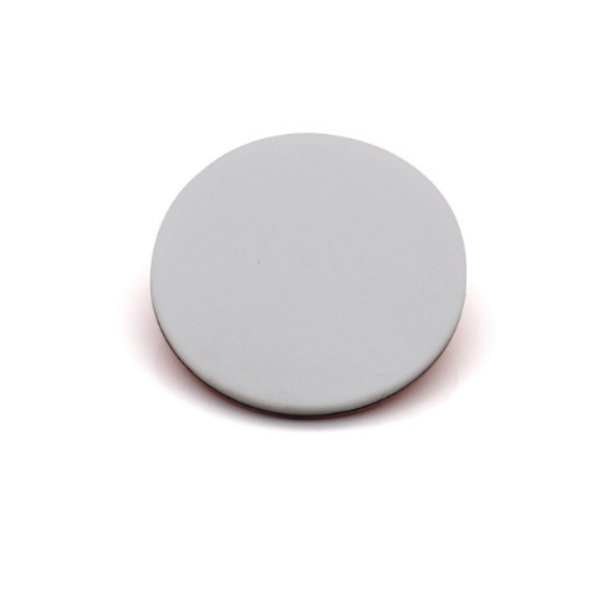
- Chemical Resistance: PTFE is highly resistant to a wide range of chemicals, including acids, bases, and solvents, making it ideal for corrosive applications.
- Non-Stick Surface: The material’s low surface energy allows for the production of coatings that resist adhesion, which is beneficial in various applications.
- Electrical Insulation: Excellent dielectric properties make it a great choice for insulating electrical components.
- High Temperature Resistance: PTFE can withstand a broad temperature range, maintaining its performance even at high temperatures.
- Durable Coatings: PTFE sputtering targets produce uniform and durable coatings with low friction and high wear resistance.
-
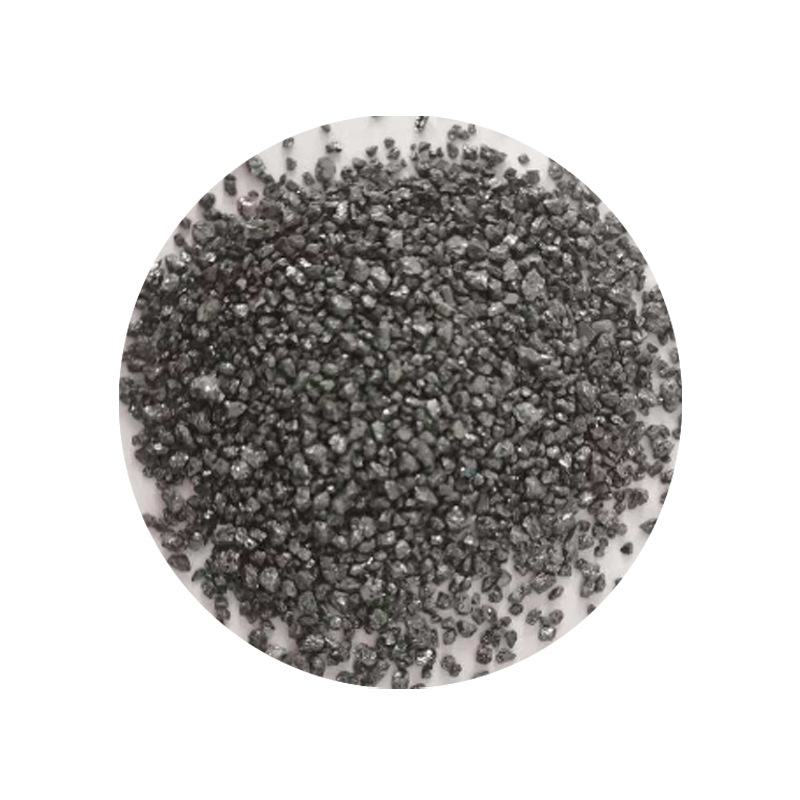
- High Hardness: SiC is one of the hardest materials available, making it ideal for protective coatings and abrasive applications.
- High Thermal Conductivity: SiC efficiently dissipates heat, making it suitable for high-temperature coatings in optical and electronic devices.
- Chemical Stability: SiC is highly resistant to corrosion and oxidation, which is beneficial for coatings in harsh environments.
- Wide Bandgap: In electronics, SiC thin films enable higher efficiency in power management and thermal resistance.
-
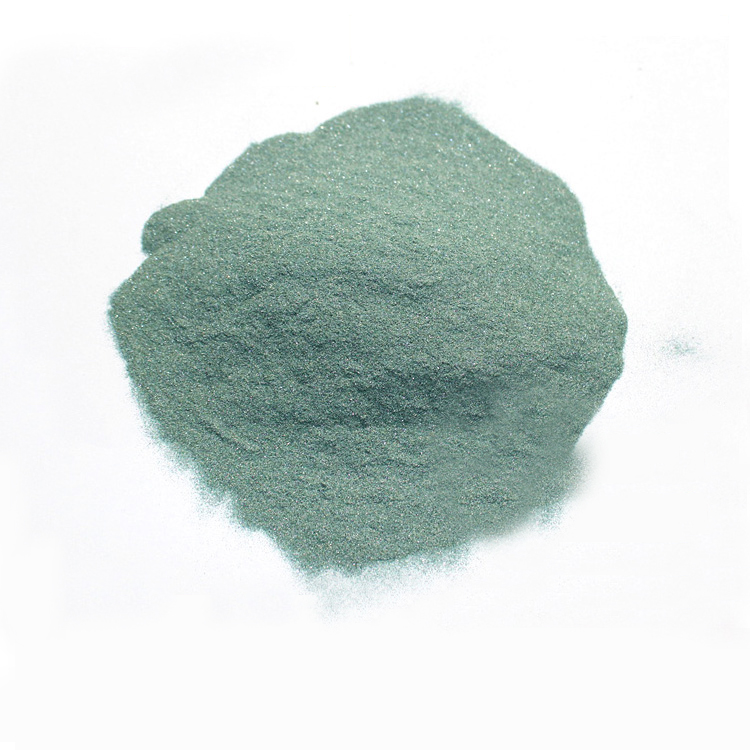
- Exceptional Hardness: Mohs hardness of 9.2, ideal for abrasives and wear-resistant applications.
- Thermal Resistance: Stable in high-temperature environments up to 2,700°C.
- High Thermal Conductivity: Efficient heat transfer for thermal management.
- Chemical Inertness: Resistant to corrosion and oxidation in harsh conditions.
- Customizable Particle Sizes: Nano and micron sizes for specialized applications.
- Eco-friendly: Minimal environmental impact during use.
-
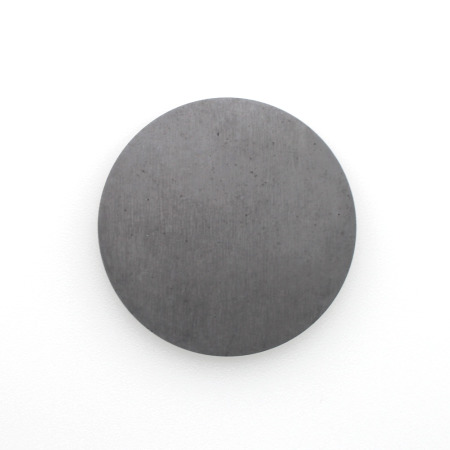
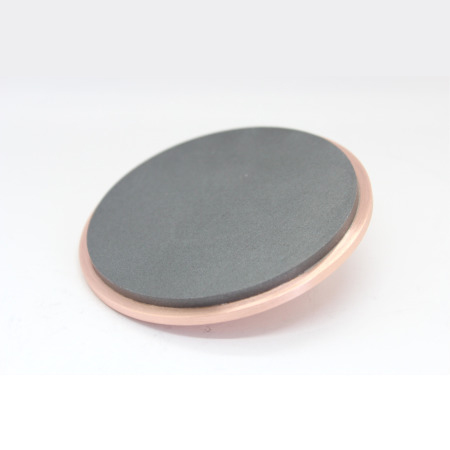
- Exceptional Hardness: Ideal for durable, wear-resistant coatings.
- High Thermal Stability: Performs well under extreme temperatures.
- Wide Bandgap Properties: Suitable for high-power and high-frequency applications.
- Chemical Resistance: Resilient to corrosive environments.
- Customizable Configurations: Available in various sizes, purities, and bonding options.
-
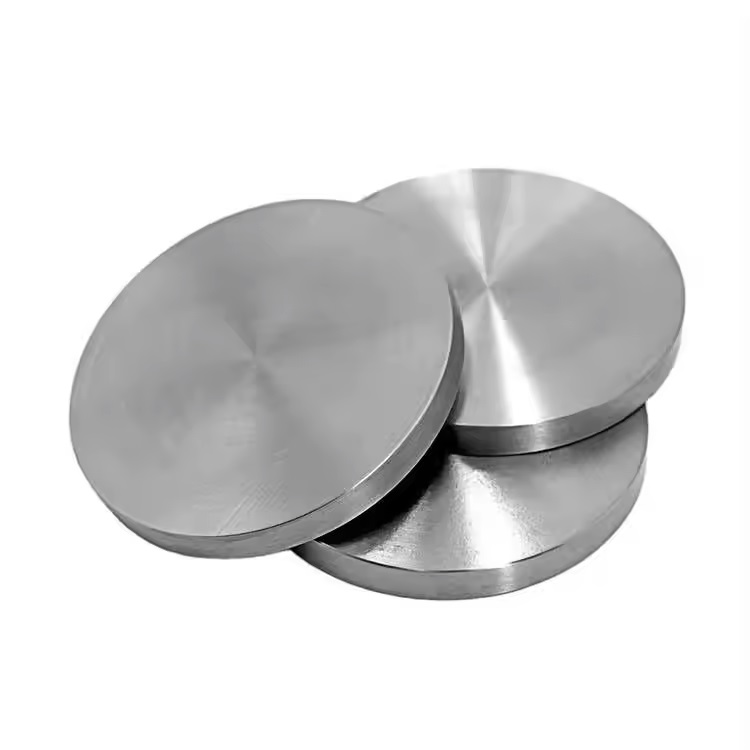
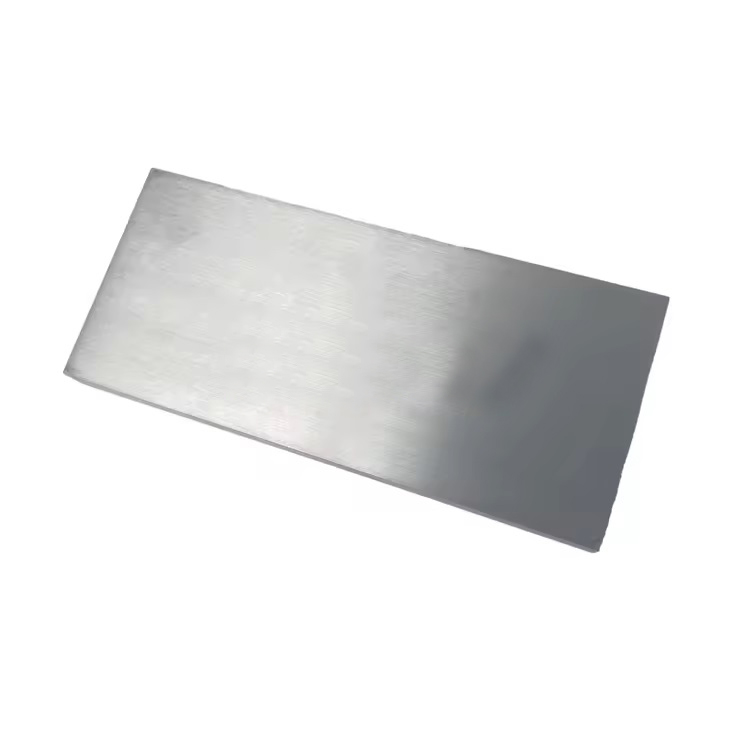
- Extreme Hardness: TaC coatings provide excellent hardness, making them ideal for cutting tools, wear-resistant coatings, and surfaces exposed to high friction.
- High Melting Point: With a melting point exceeding 3880°C, TaC is one of the most heat-resistant materials, suitable for high-temperature applications in aerospace and industrial processes.
- Corrosion Resistance: TaC films offer robust resistance to chemicals, making them ideal for protective coatings in chemically aggressive environments.
- Electrical Conductivity: TaC has good electrical conductivity, which is advantageous in certain electronic and semiconductor applications.
- Oxidation Resistance: The oxidation resistance of TaC enhances its performance in environments where exposure to high temperatures and reactive gases is common.
-
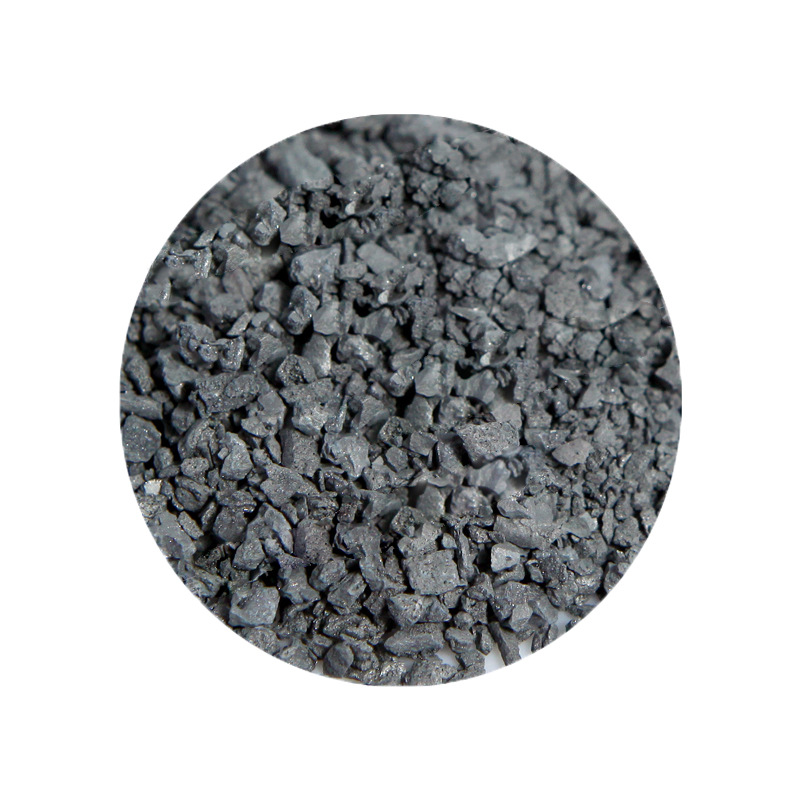
- High Hardness: TiC is extremely hard, making it useful for coatings that require high wear resistance.
- Thermal Stability: TiC can withstand high temperatures, making it ideal for high-temperature deposition and coating processes.
- Corrosion Resistance: TiC coatings provide excellent resistance to oxidation and chemical corrosion, enhancing component longevity in harsh environments.
- Electrical Conductivity: As a conductive ceramic, TiC is suitable for applications requiring both mechanical strength and electrical conductivity.
-
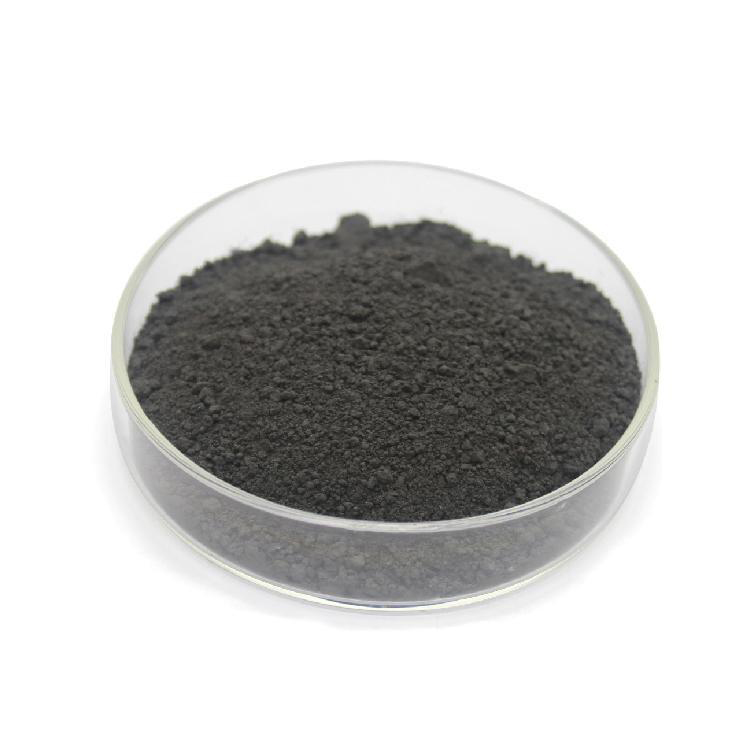
- High Hardness: Ideal for cutting and abrasive applications.
- Superior Thermal Stability: Maintains integrity at elevated temperatures.
- Excellent Wear Resistance: Prolongs the life of coatings and components.
- Chemical Inertness: Resists corrosion in harsh chemical environments.
- Conductive Properties: Suitable for electrical and thermal applications.
- Customizable Particle Size: Available in nano and micron forms to meet specific application needs.
-
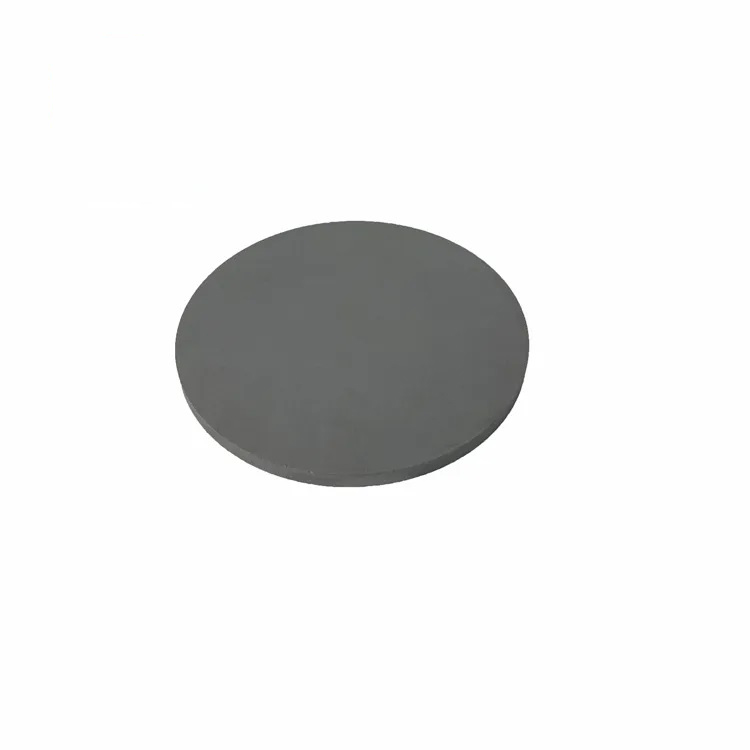
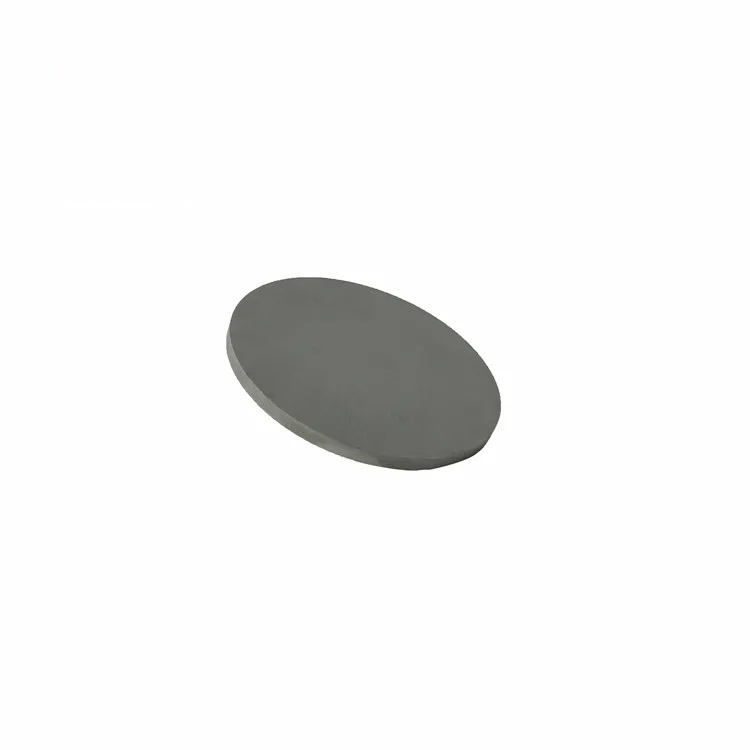
- High Hardness: TiC coatings provide excellent hardness, making them suitable for wear-resistant applications like cutting tools and dies.
- Corrosion Resistance: TiC films resist oxidation and corrosion, providing a protective barrier in harsh environments, including high-temperature applications.
- Thermal Stability: TiC has high thermal stability, making it ideal for coatings in high-temperature operations such as aerospace and automotive components.
- Electrical Conductivity: TiC exhibits good electrical conductivity, making it suitable for certain electronic and semiconductor applications where conductivity is critical.
- Chemical Resistance: TiC coatings offer chemical resistance, providing protective layers against corrosive agents and harsh chemicals.
-
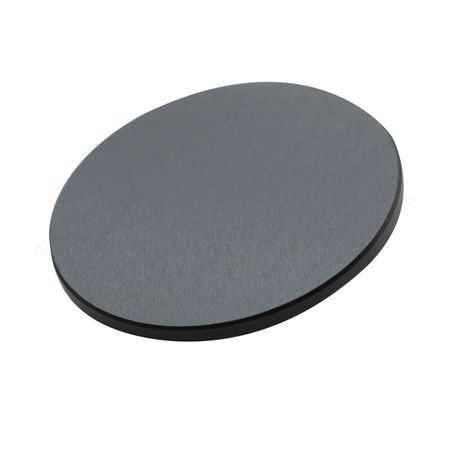
- Exceptional Hardness: Provides outstanding resistance to abrasion and wear.
- Chemical Stability: Maintains performance in harsh and reactive environments.
- High Thermal Conductivity: Efficiently dissipates heat in critical applications.
- Uniform Deposition: Ensures consistent film quality with minimal defects.
- Customizable Options: Available in various sizes and purities for specialized applications.
-
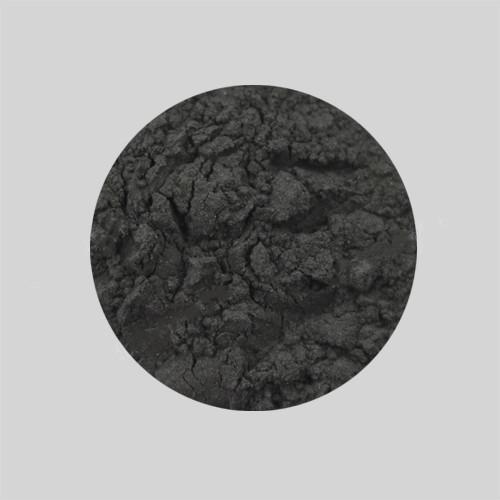
- High Hardness: Vanadium Carbide is one of the hardest materials, providing outstanding wear resistance.
- High Melting Point: Boasts a high melting point of approximately 2,750°C, making it suitable for extreme temperature environments.
- Chemical Stability: Excellent resistance to corrosion and oxidation, ensuring longevity and durability in harsh environments.
- Wear Resistance: Ideal for applications involving high friction and wear.
- Customizable Particle Size: Available in various grades and particle sizes to meet specific customer needs.