Showing 1–12 of 35 results
-
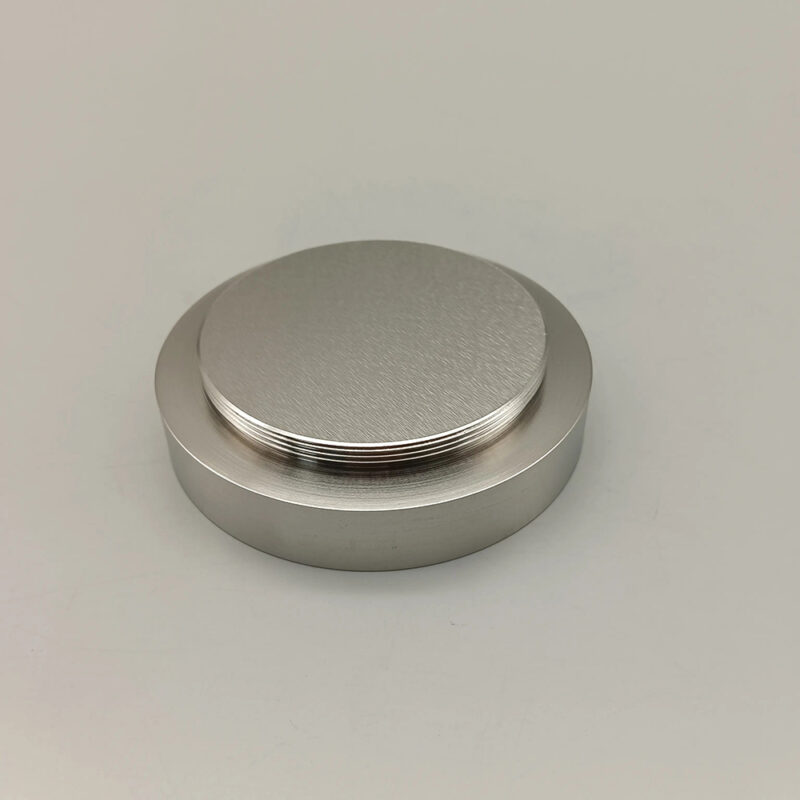
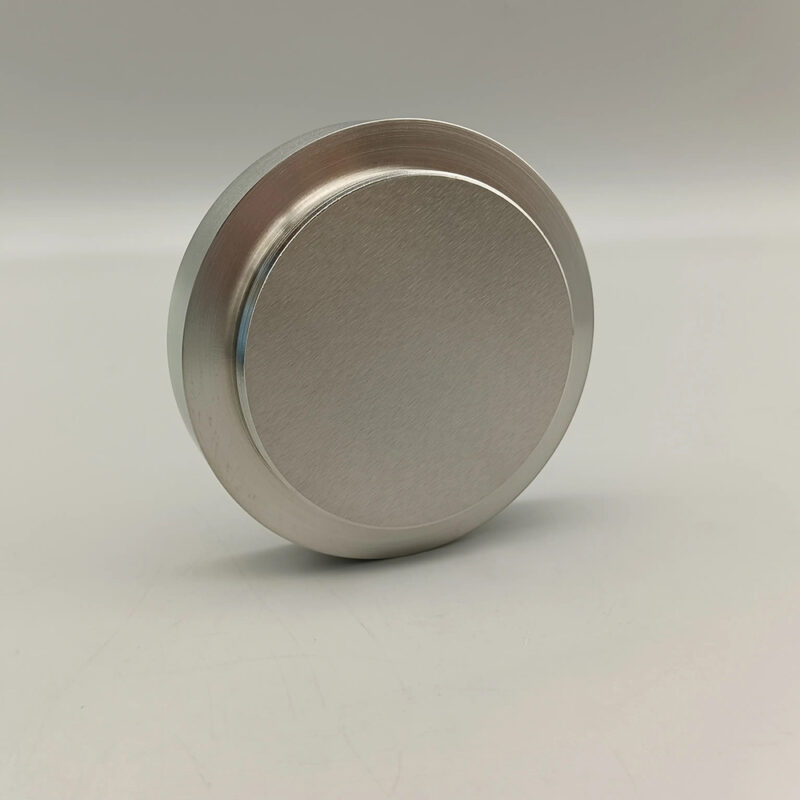
- High Mechanical Strength: The combination of aluminum, chromium, cobalt, iron, and nickel in the alloy imparts excellent mechanical strength, making it ideal for thin films that require toughness and resistance to mechanical stress.
- Superior Corrosion Resistance: Chromium and nickel contribute to the alloy’s outstanding corrosion resistance, allowing thin films to perform well in corrosive environments, such as in aerospace and marine applications.
- Thermal Stability: AlCrCoFeNi alloy thin films retain their structural properties at elevated temperatures, making them suitable for high-temperature environments, such as in engines and turbines.
- Wear Resistance: Cobalt and chromium enhance the wear resistance of the alloy, making it ideal for hard coatings in industrial tools and machinery parts.
- High-Entropy Alloy Properties: As a high-entropy alloy, AlCrCoFeNi offers a unique combination of properties that cannot be achieved with traditional alloys, including high strength, toughness, and resistance to oxidation and corrosion.
-
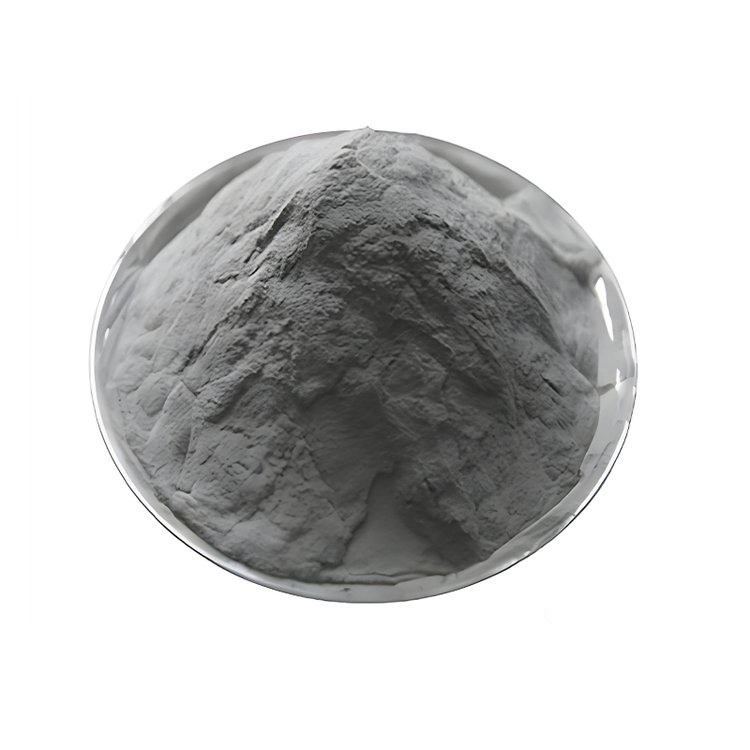
- High Strength-to-Weight Ratio: Combines lightweight characteristics with robust mechanical properties.
- Excellent Wear Resistance: Ensures durability in high-stress environments.
- Corrosion and Oxidation Resistance: Performs reliably in extreme chemical or thermal conditions.
- Uniform Microstructure: Enhances performance consistency across applications.
- Wide Applicability: Suitable for 3D printing, surface coatings, and high-performance components.
-
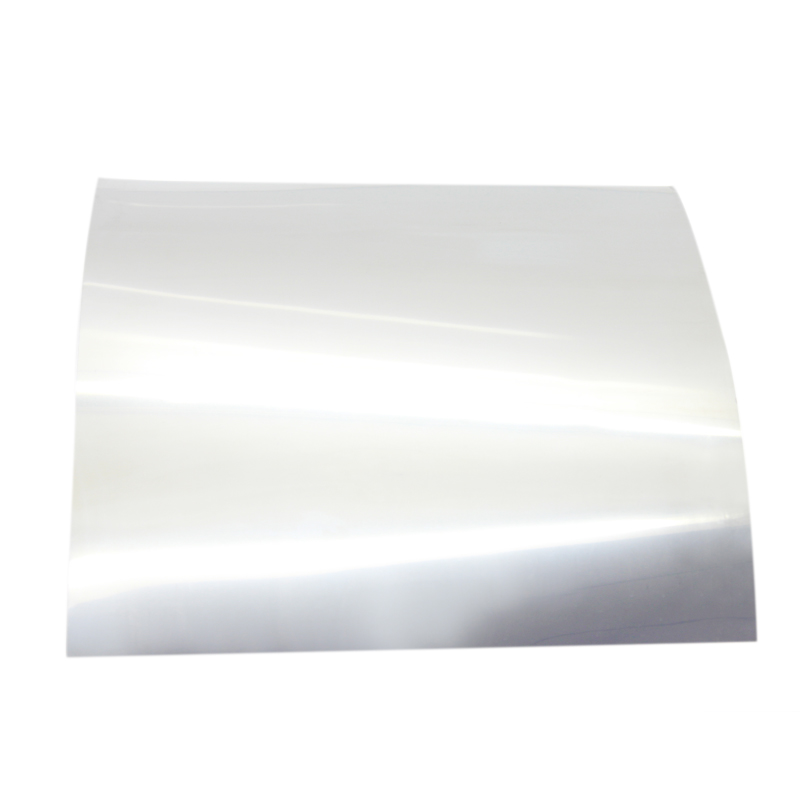
- Magnetic Properties: Cobalt is ferromagnetic, meaning it can retain magnetization, making cobalt foil ideal for applications requiring strong and stable magnetic fields. It is often used in magnetic recording media, electric motors, and magnetic shields.
- Corrosion Resistance: Cobalt foil offers excellent resistance to corrosion, especially in harsh environments such as high humidity, acidic conditions, and exposure to alkalis. This makes it a suitable material for use in chemical processing and marine environments.
- High Strength and Durability: Cobalt has a high tensile strength and is resistant to wear and tear. The durability of cobalt foil makes it a reliable choice for high-stress applications, including components exposed to high mechanical loads.
- High Melting Point: Cobalt has a relatively high melting point of 1,495°C (2,723°F), making cobalt foil suitable for high-temperature environments such as those found in aerospace, electronics, and industrial applications.
- Thermal Stability: Cobalt foil exhibits excellent thermal stability, retaining its strength and performance under a wide range of temperature conditions. It is often used in applications where materials are exposed to high temperatures and fluctuating thermal environments.
- Biocompatibility: Cobalt is biocompatible, making cobalt foil suitable for use in certain medical and dental applications. It is used in implants, prosthetics, and other devices where contact with the human body is required.
-
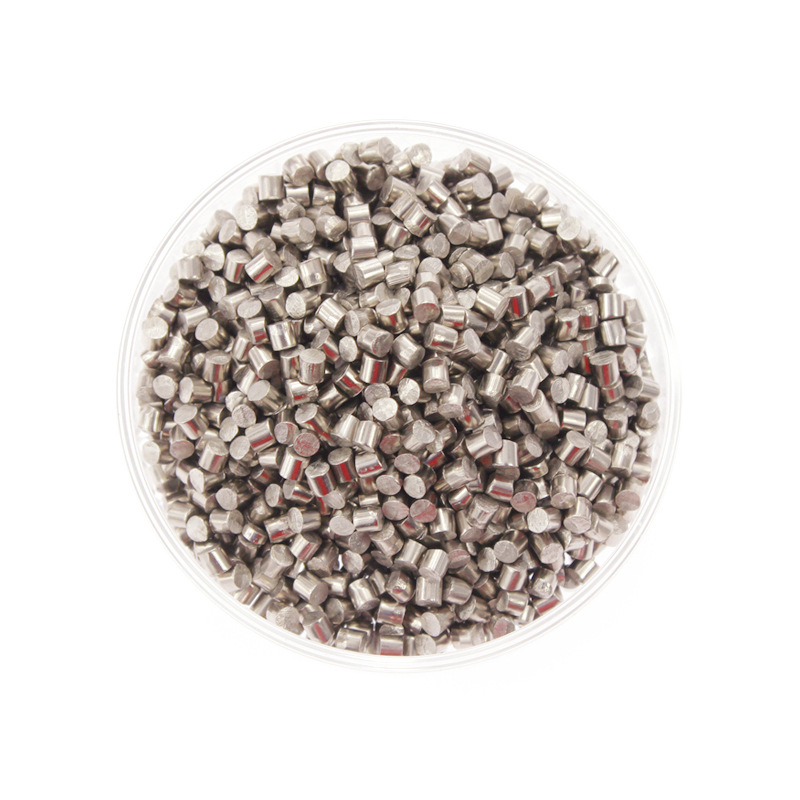
- High Magnetic Properties: Cobalt is known for its strong magnetic characteristics, making it suitable for magnetic thin films and data storage applications.
- Corrosion Resistance: Cobalt provides excellent resistance to oxidation and corrosion, particularly in harsh chemical or environmental conditions.
- High Melting Point: With a melting point of 1,495°C, cobalt is suitable for high-temperature applications, including aerospace and automotive industries.
- Wear Resistance: Cobalt thin films are highly resistant to wear and tear, making them ideal for protective coatings in demanding environments.
- Electrical Conductivity: Cobalt has good electrical conductivity, making it useful in microelectronics as a contact material or diffusion barrier.
-
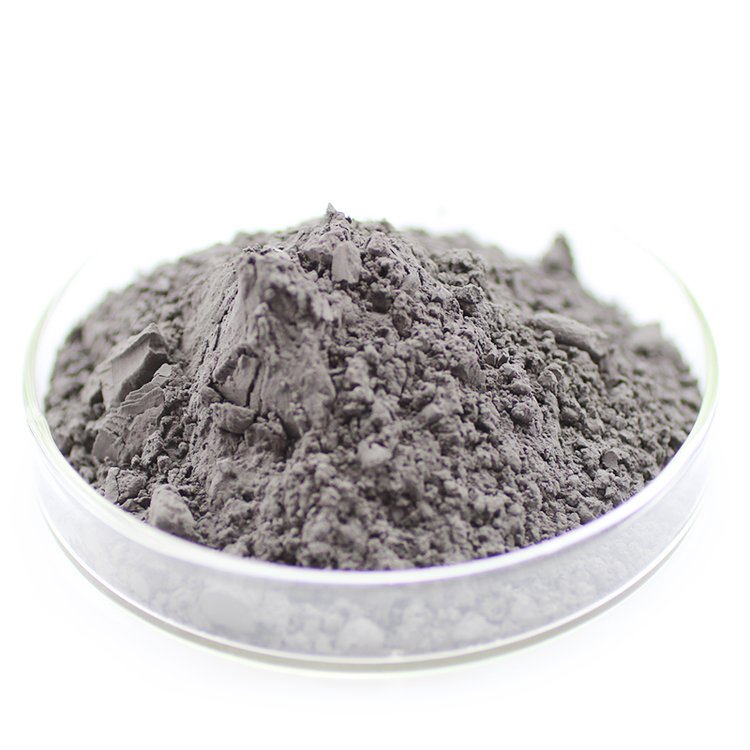
- High Purity: Ensures optimal performance in advanced applications.
- Magnetic Properties: Excellent ferromagnetic behavior for magnet manufacturing.
- Corrosion Resistance: Superior resistance to oxidation and harsh environments.
- Thermal Stability: Reliable performance at elevated temperatures.
- Customizable Particle Sizes: Nano to micrometer options for diverse applications.
- Versatile Applications: Suitable for batteries, alloys, magnets, and catalysis.
-
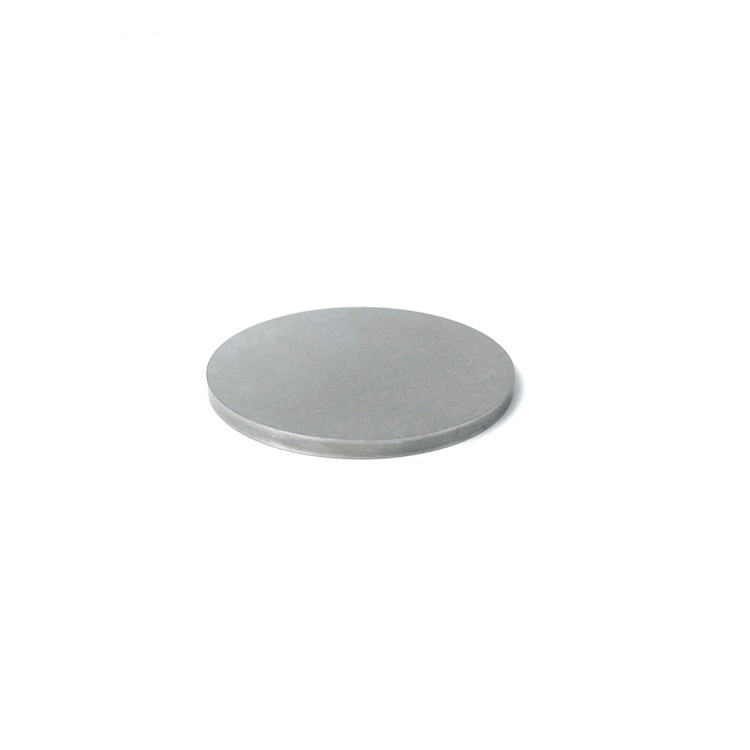

- Purity: Cobalt sputtering targets are typically available in high purity levels, such as 99.95% (3N5) or higher, ensuring the deposition of high-quality, consistent films.
- Shapes and Sizes: These targets are available in various forms, including discs, plates, and custom shapes, to suit different sputtering systems and specific application requirements.
-
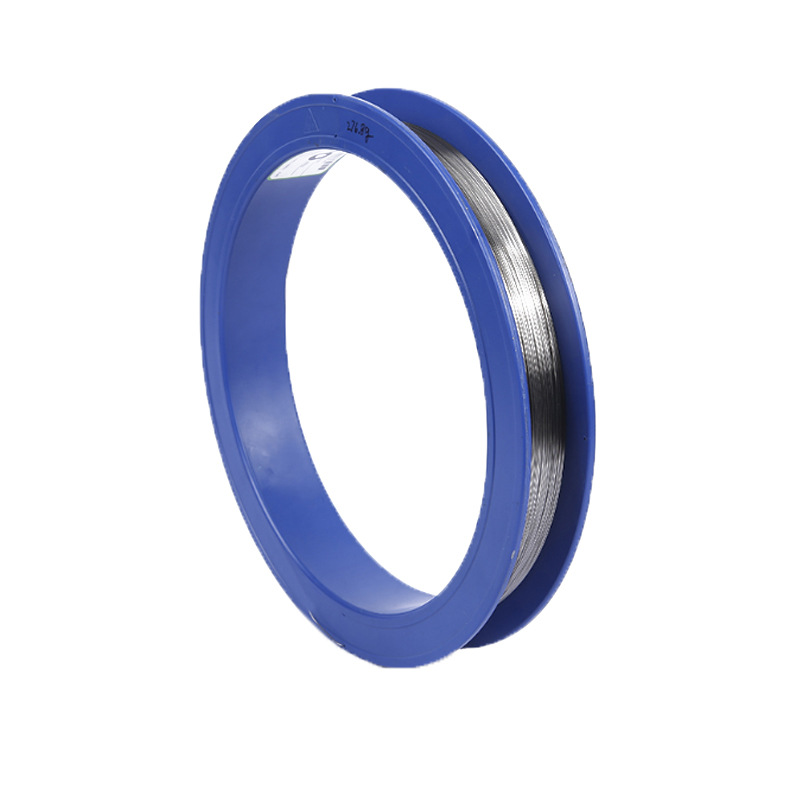
- Magnetic Excellence: Superior magnetic saturation and coercivity make cobalt wire ideal for permanent magnets and magnetic sensors.
- High Temperature Performance: Retains mechanical and magnetic properties at elevated temperatures, suitable for high-heat applications.
- Long Service Life: Outstanding wear resistance and corrosion protection ensure durability and longevity.
- Versatility: Available in various diameters, purities, and forms to suit diverse industrial and scientific needs.
- Customizability: Can be tailored for specific applications, including custom lengths, coatings, and alloys.
- Environmentally Stable: Resists degradation in extreme environments, such as marine or chemically aggressive settings.
-
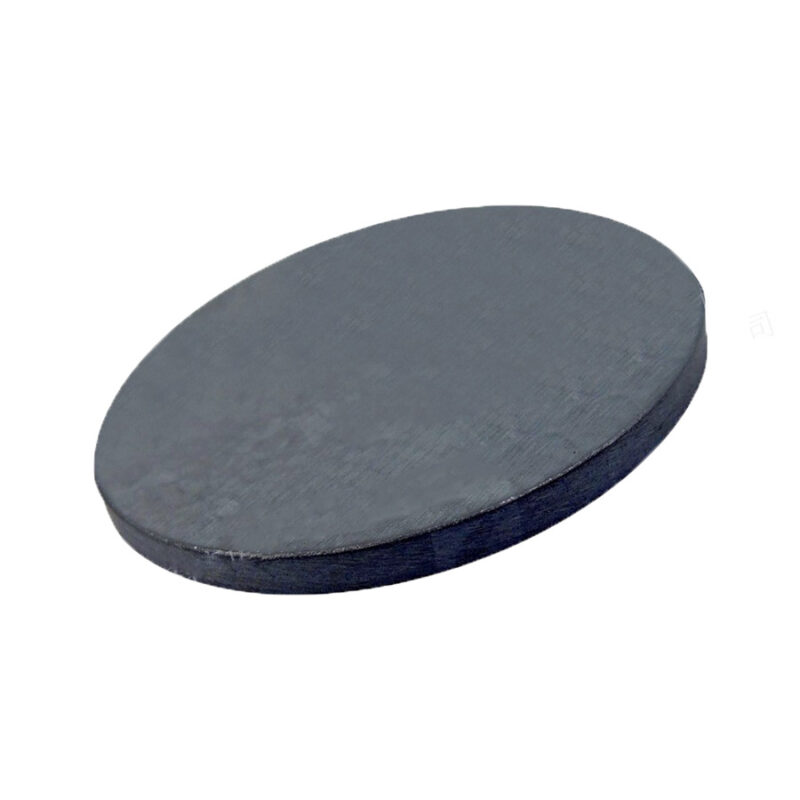
- High Catalytic Activity: Co₂O₃ is well known for its excellent catalytic properties, making it suitable for applications requiring enhanced oxidation reactions.
- Magnetic Properties: With significant magnetic behavior, Co₂O₃ is valuable in magnetic and spintronic devices.
- Electrical Conductivity: Co₂O₃ has good electrical conductivity, making it useful for battery and electronic applications.
- Environmental Stability: Co₂O₃ exhibits stability under various environmental conditions, ensuring the longevity of the thin films produced.
-
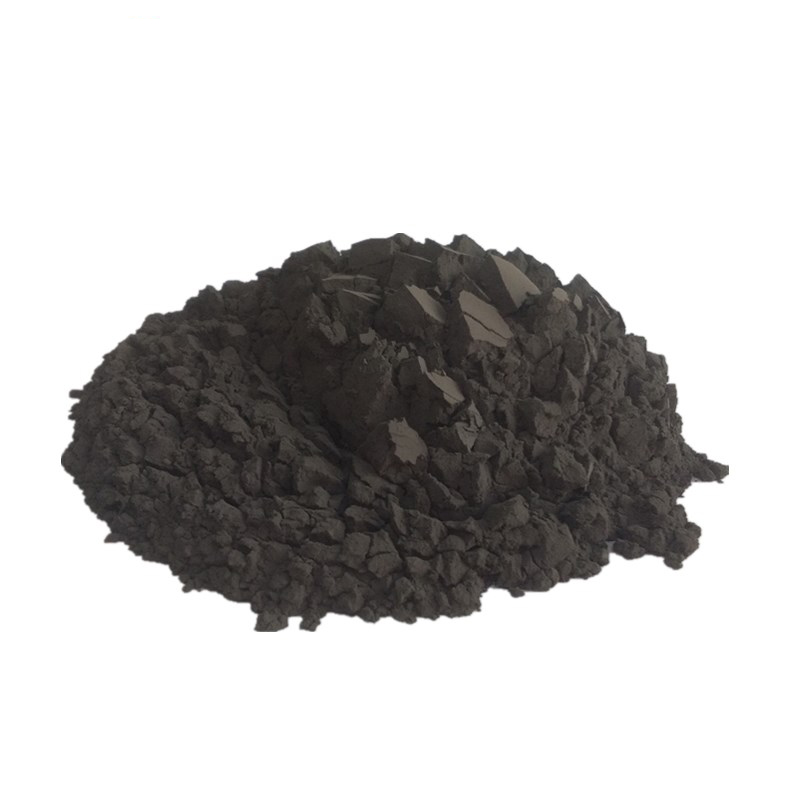
- High Purity: Available with purity levels of ≥99.5%.
- Thermal Stability: Stable under high-temperature conditions.
- Catalytic Efficiency: Effective for a variety of chemical reactions.
- Electronic Properties: Suitable for semiconductors and electronic components.
- Customizable Particle Sizes: Nano (<100 nm) and micro (1–50 µm) grades available or customized.
-
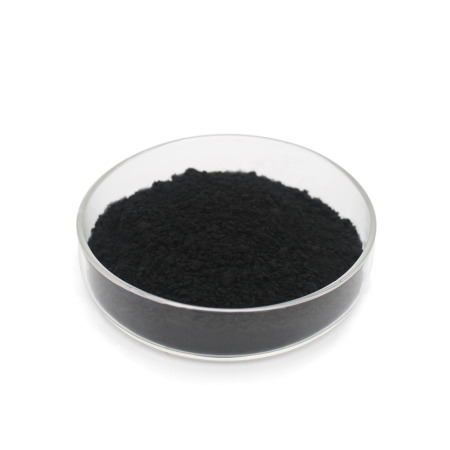
- High Purity: Available with purity levels of ≥99.5%.
- Thermal Stability: Performs effectively in high-temperature environments.
- Magnetic Properties: Exhibits unique magnetic behavior suitable for electronic applications.
- Catalytic Activity: Effective in promoting chemical reactions.
- Customizable Particle Sizes: Nano (<100 nm) and micro (1–50 µm) grades available or customized.
-
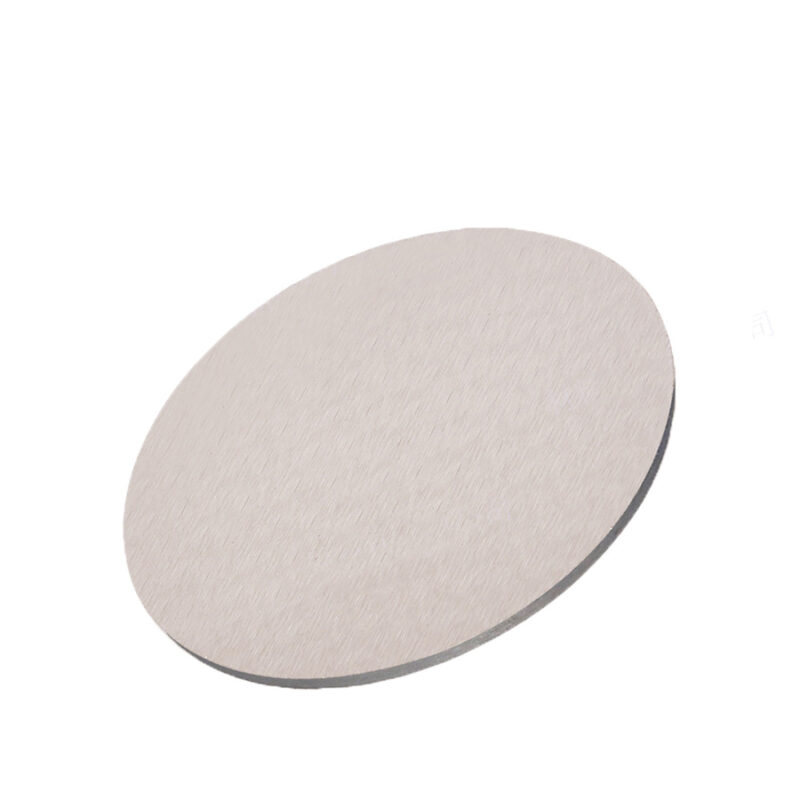
- High Conductivity: Co3O4 thin films exhibit good electrical conductivity, which can be tailored for use in supercapacitors and battery electrodes.
- Catalytic Activity: Cobalt oxide is a highly efficient catalyst, especially in electrochemical applications, due to its ability to facilitate oxidation-reduction reactions.
- Good Thermal Stability: Co3O4 is thermally stable, making it suitable for high-temperature applications such as catalysis and energy storage.
- Magnetic Properties: Co3O4 films possess useful magnetic properties, which are exploited in various magnetic and electronic devices.
-
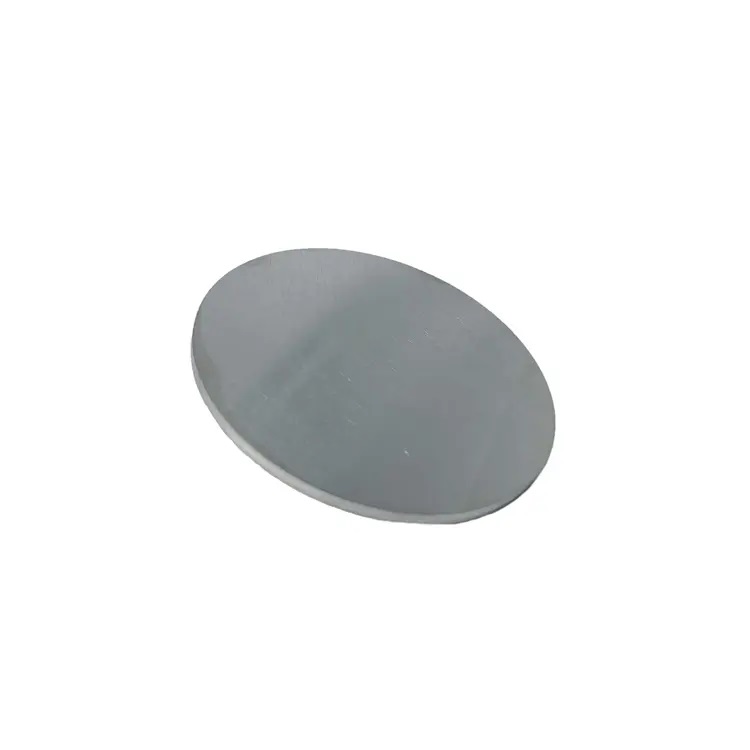
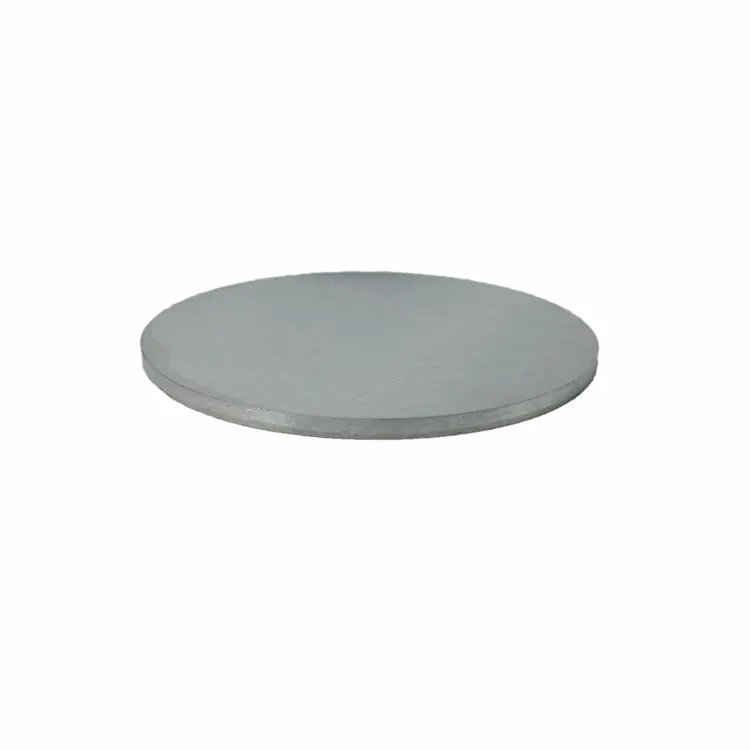
- Exceptional Corrosion Resistance: The addition of chromium significantly enhances the corrosion resistance of CoCr thin films, making them suitable for harsh environments, including medical and aerospace applications.
- High Wear Resistance: CoCr alloys are known for their wear resistance, making them ideal for applications requiring durable coatings, such as in industrial machinery and tools.
- Thermal Stability: Cobalt’s high melting point, combined with chromium’s ability to withstand oxidation, allows CoCr thin films to maintain their properties in high-temperature environments.
- Biocompatibility: The CoCr alloy is biocompatible, making it the material of choice for medical implants and devices, where resistance to body fluids and mechanical durability are essential.
- Good Mechanical Strength: CoCr sputtering targets produce films with excellent mechanical properties, ensuring strength and toughness for components exposed to stress and abrasion.