Showing 1–12 of 39 results
-
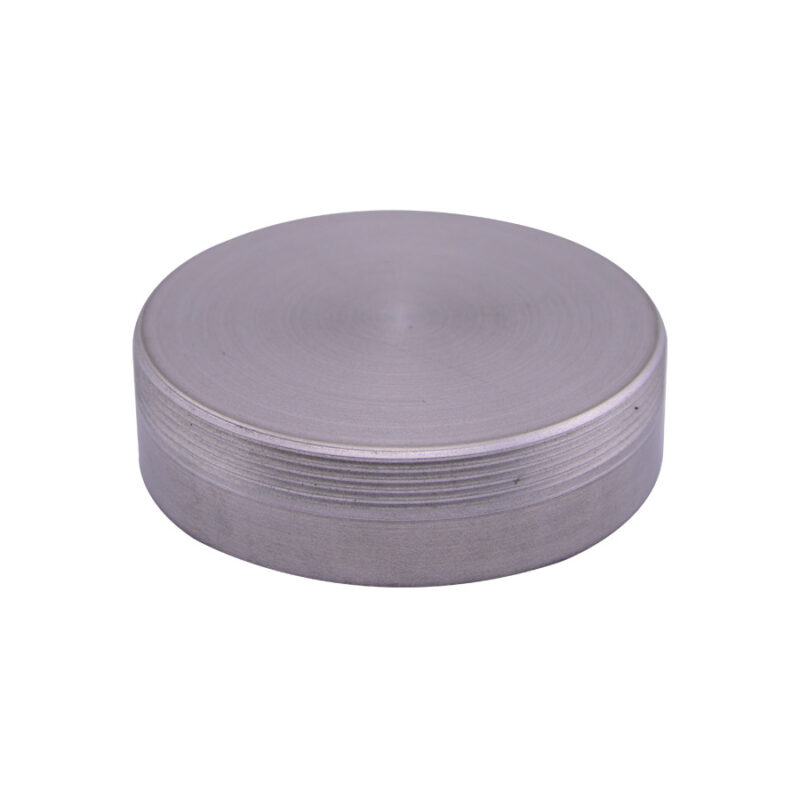
- Superior Electrical Conductivity: Silver provides excellent electrical conductivity, making AgCr thin films ideal for use in electronic applications requiring efficient conduction of electricity.
- Corrosion Resistance: Chromium enhances the corrosion resistance of AgCr alloy, allowing the thin films to perform reliably in environments prone to oxidation and chemical exposure.
- Durability and Wear Resistance: The addition of chromium improves the mechanical strength and wear resistance of AgCr thin films, ensuring longer-lasting performance in various industrial applications.
- High Reflectivity: Silver’s reflective properties make AgCr thin films suitable for optical coatings where high reflectivity is desired, such as in mirrors and optical components.
- Customizable Composition: The ratio of silver to chromium in the alloy can be adjusted to tailor the properties of the thin film for specific applications, such as improving conductivity or enhancing corrosion resistance.
-
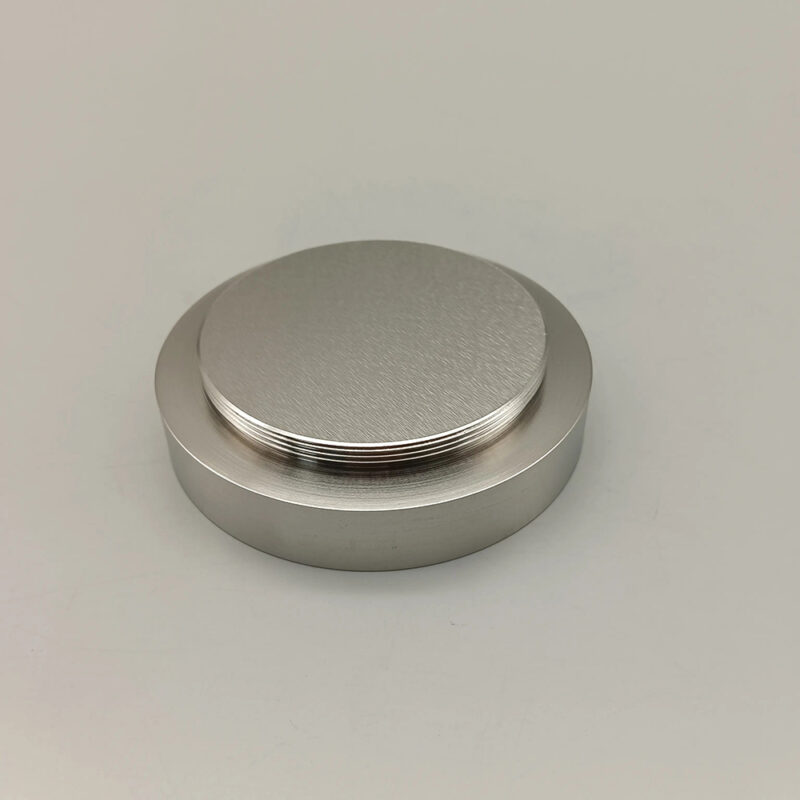
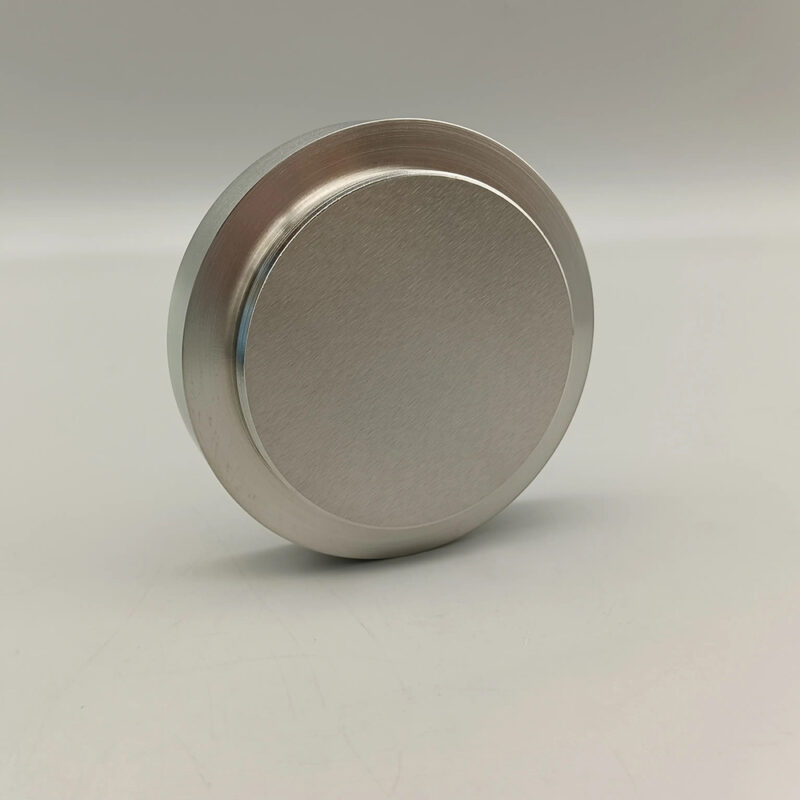
- High Mechanical Strength: The combination of aluminum, chromium, cobalt, iron, and nickel in the alloy imparts excellent mechanical strength, making it ideal for thin films that require toughness and resistance to mechanical stress.
- Superior Corrosion Resistance: Chromium and nickel contribute to the alloy’s outstanding corrosion resistance, allowing thin films to perform well in corrosive environments, such as in aerospace and marine applications.
- Thermal Stability: AlCrCoFeNi alloy thin films retain their structural properties at elevated temperatures, making them suitable for high-temperature environments, such as in engines and turbines.
- Wear Resistance: Cobalt and chromium enhance the wear resistance of the alloy, making it ideal for hard coatings in industrial tools and machinery parts.
- High-Entropy Alloy Properties: As a high-entropy alloy, AlCrCoFeNi offers a unique combination of properties that cannot be achieved with traditional alloys, including high strength, toughness, and resistance to oxidation and corrosion.
-
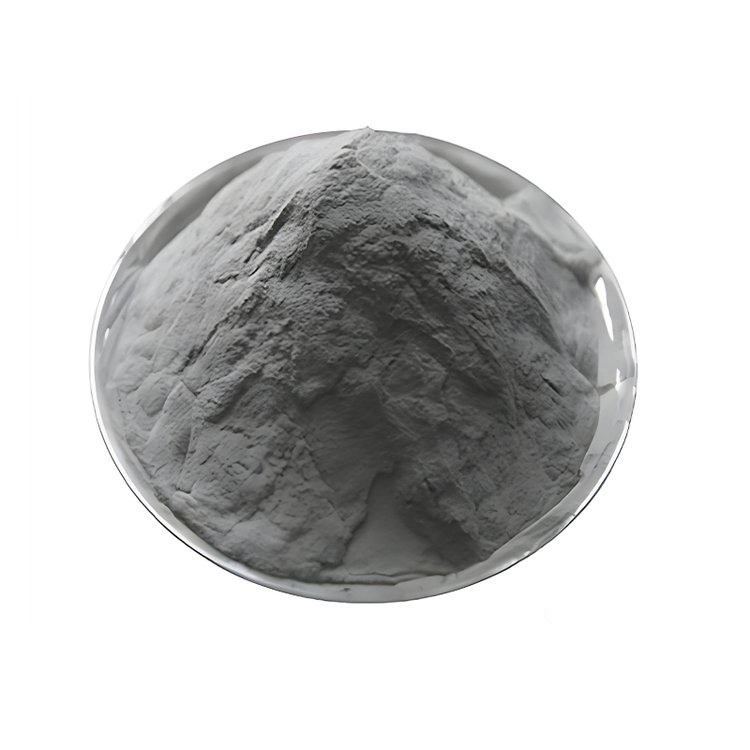
- High Strength-to-Weight Ratio: Combines lightweight characteristics with robust mechanical properties.
- Excellent Wear Resistance: Ensures durability in high-stress environments.
- Corrosion and Oxidation Resistance: Performs reliably in extreme chemical or thermal conditions.
- Uniform Microstructure: Enhances performance consistency across applications.
- Wide Applicability: Suitable for 3D printing, surface coatings, and high-performance components.
-
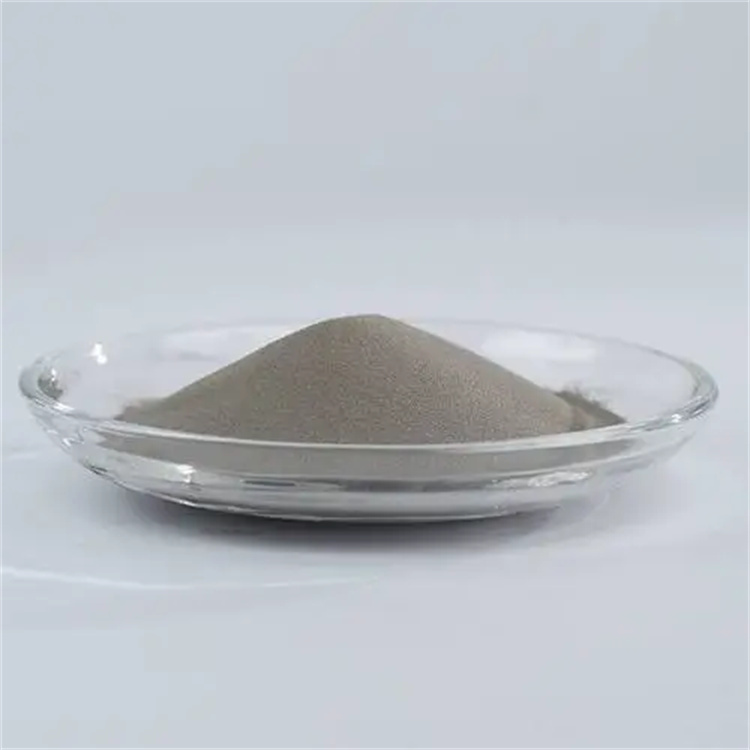
- Exceptional Corrosion Resistance: Resistant to pitting, crevice corrosion, and stress corrosion cracking in aggressive environments.
- High Strength: Maintains mechanical integrity under high stress and temperature conditions.
- Weldability: Excellent compatibility with various welding methods, including TIG, MIG, and laser welding.
- Versatility: Suitable for additive manufacturing, powder metallurgy, and thermal spray coating applications.
- Thermal Stability: Performs reliably across a wide range of temperatures without compromising material properties.
-
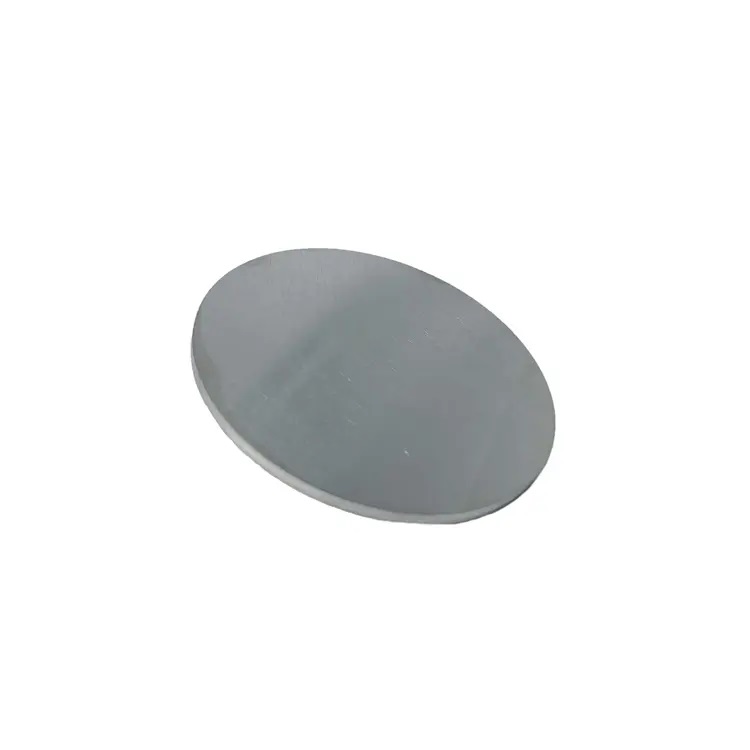
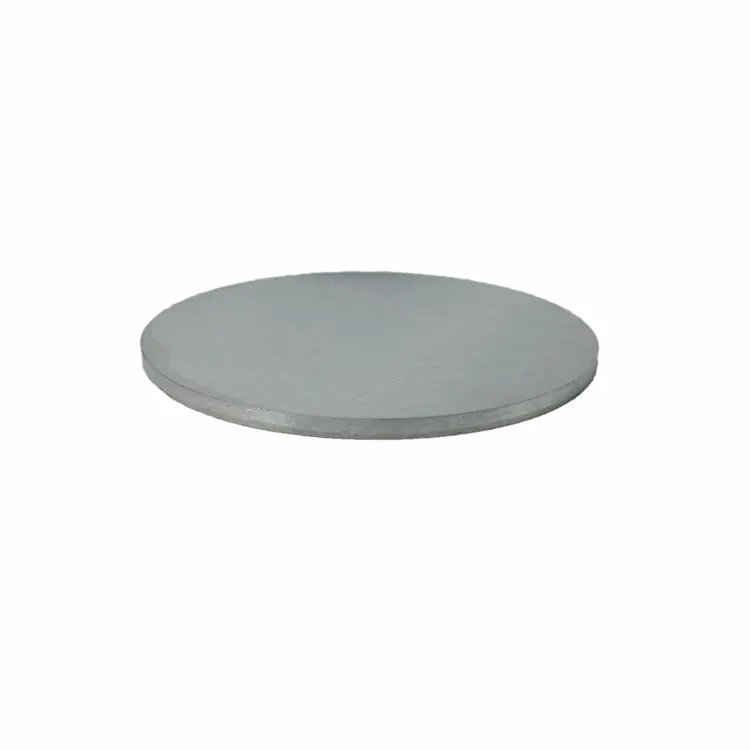
- Exceptional Corrosion Resistance: The addition of chromium significantly enhances the corrosion resistance of CoCr thin films, making them suitable for harsh environments, including medical and aerospace applications.
- High Wear Resistance: CoCr alloys are known for their wear resistance, making them ideal for applications requiring durable coatings, such as in industrial machinery and tools.
- Thermal Stability: Cobalt’s high melting point, combined with chromium’s ability to withstand oxidation, allows CoCr thin films to maintain their properties in high-temperature environments.
- Biocompatibility: The CoCr alloy is biocompatible, making it the material of choice for medical implants and devices, where resistance to body fluids and mechanical durability are essential.
- Good Mechanical Strength: CoCr sputtering targets produce films with excellent mechanical properties, ensuring strength and toughness for components exposed to stress and abrasion.
-
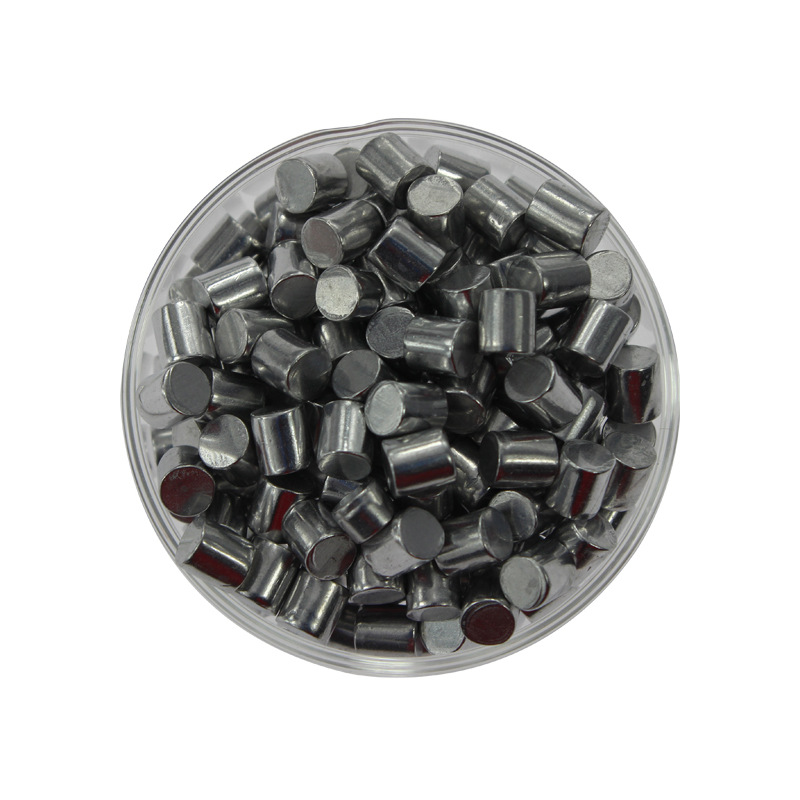
- High Strength: Provides excellent mechanical strength and stability at elevated temperatures.
- Corrosion Resistance: Resists oxidation and corrosion, enhancing the longevity of components.
- Wear Resistance: Ideal for applications requiring materials that can withstand high levels of wear and tear.
-
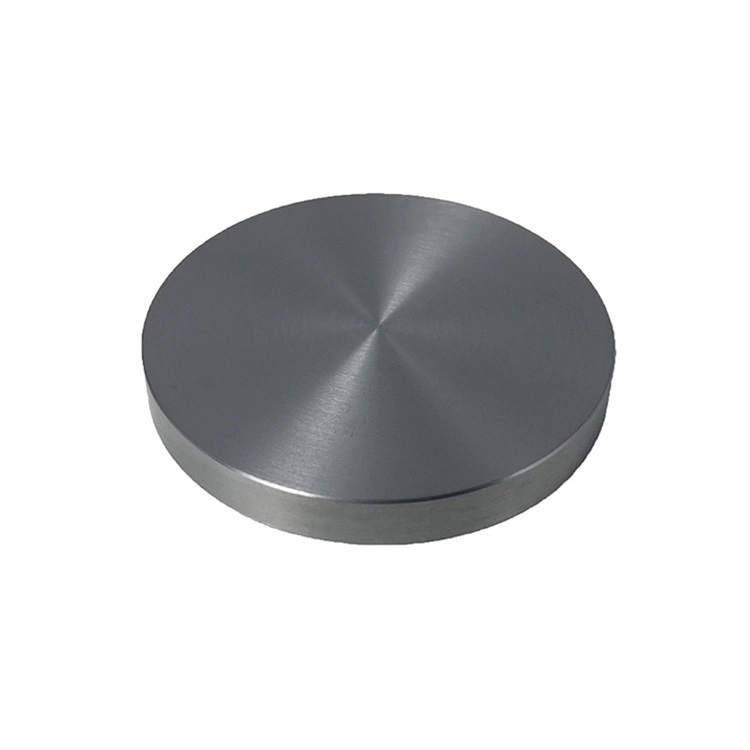
- Biocompatibility: CoCrMo alloys are highly biocompatible, making them ideal for medical implants and devices that come in contact with human tissue and bone.
- Wear Resistance: The addition of molybdenum enhances the alloy’s resistance to wear and fatigue, making CoCrMo thin films durable under mechanical stress and long-term use.
- Corrosion Resistance: Cobalt and chromium provide excellent corrosion resistance, protecting components from damage in harsh environments, including body fluids, chemicals, and marine conditions.
- Mechanical Strength: CoCrMo alloy sputtering targets produce thin films with exceptional mechanical strength, allowing coated components to withstand high loads and stresses.
- High-Temperature Stability: CoCrMo alloys retain their properties at elevated temperatures, making them suitable for applications in aerospace and industrial settings where heat resistance is critical.
-
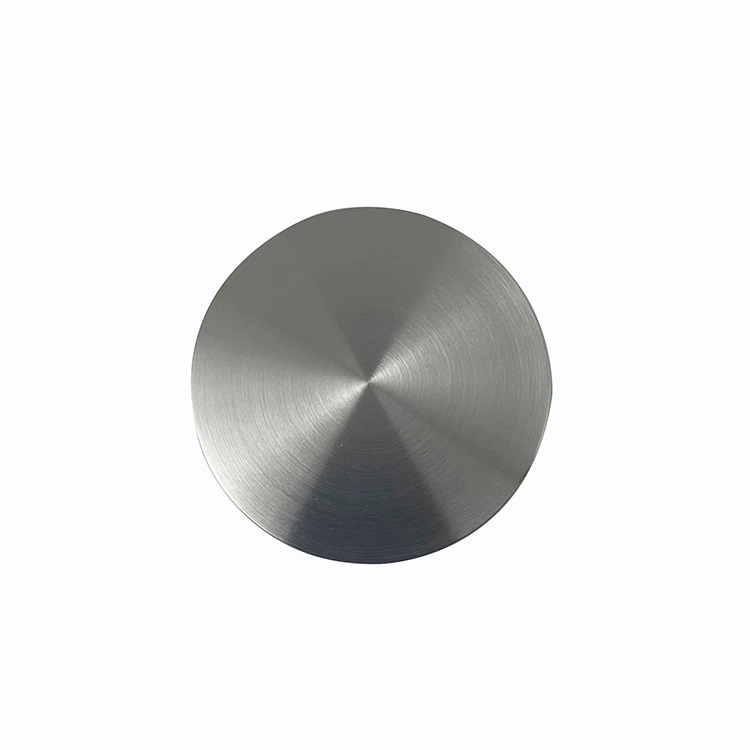
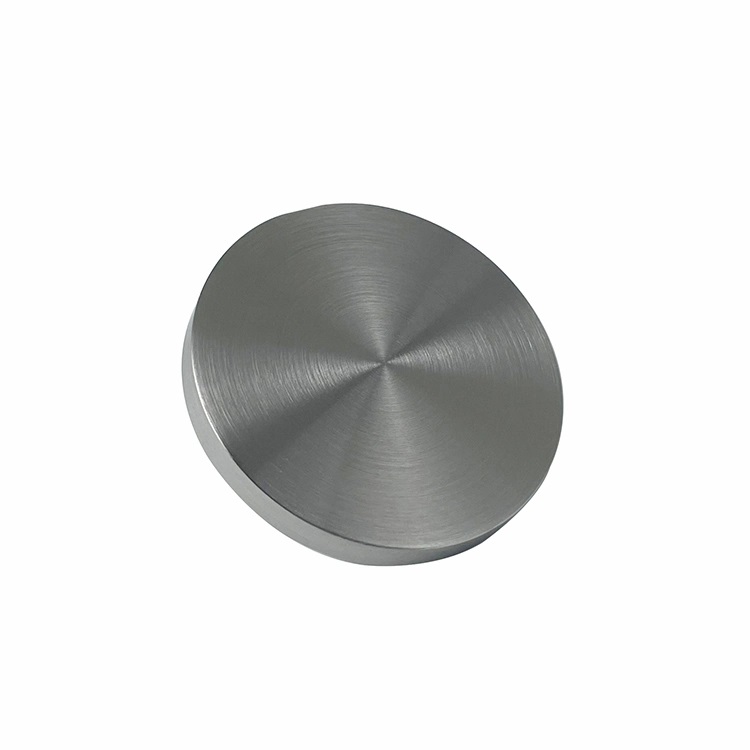
- Excellent Corrosion Resistance: Chromium and nickel provide outstanding corrosion resistance, making CoCrNi thin films suitable for harsh environments, including those found in aerospace, medical, and industrial applications.
- High Mechanical Strength: Cobalt contributes to the alloy’s superior mechanical properties, providing excellent wear resistance and toughness, which are essential for industrial and aerospace components.
- Thermal Stability: The combination of cobalt, chromium, and nickel allows CoCrNi thin films to retain their properties at elevated temperatures, making them ideal for high-temperature environments, such as in aerospace and energy applications.
- Biocompatibility: CoCrNi alloys are biocompatible, making them suitable for use in medical implants and devices, where both mechanical strength and resistance to bodily fluids are required.
- Good Electrical Properties: The electrical conductivity of the alloy makes it suitable for electronic applications, including connectors and semiconductor components.
-
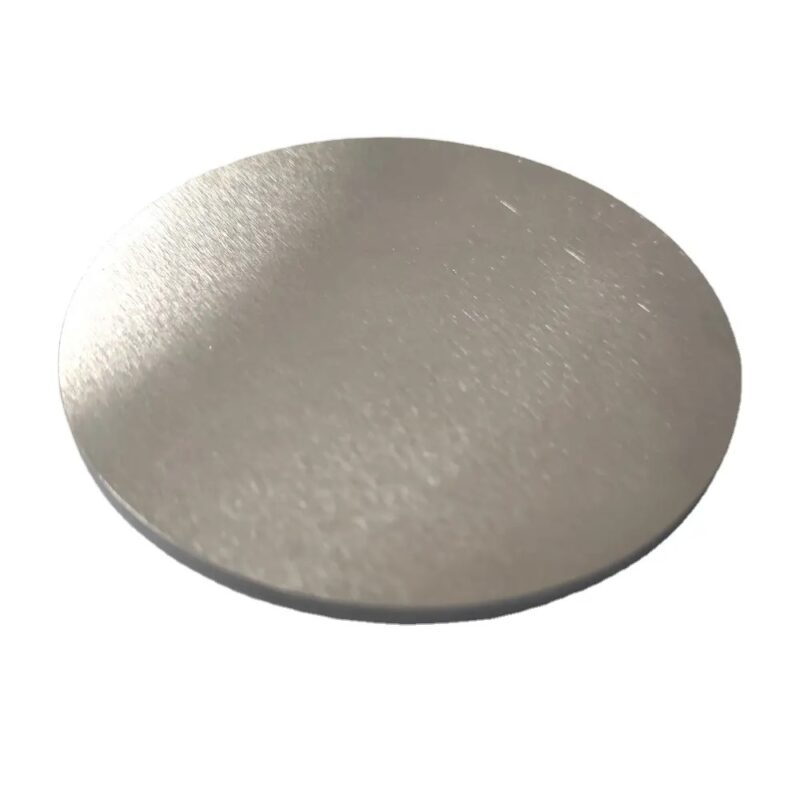
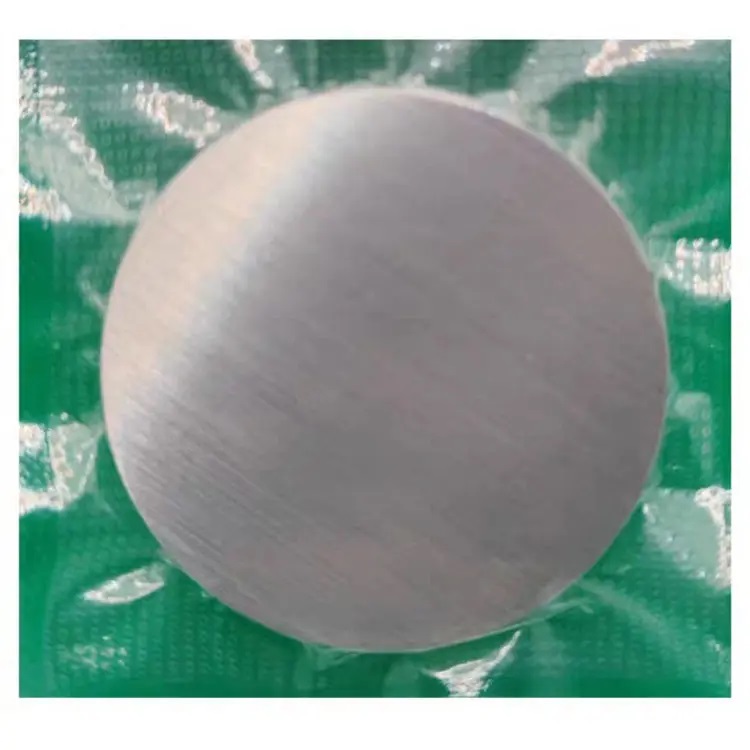
- Wear Resistance: CoCrW alloy provides excellent resistance to wear and abrasion, making it ideal for coatings on components subjected to mechanical stress and friction.
- Corrosion Resistance: The addition of chromium enhances the alloy’s resistance to corrosion, while tungsten improves hardness and durability, ensuring long-lasting performance in harsh environments.
- High-Temperature Stability: Cobalt and tungsten offer high thermal stability, allowing CoCrW thin films to retain their properties at elevated temperatures, making them suitable for high-heat applications such as in aerospace and power generation.
- Biocompatibility: CoCrW alloys are biocompatible, making them a preferred choice for medical applications such as orthopedic implants and surgical instruments.
- Excellent Hardness: The combination of tungsten and cobalt increases the hardness of the alloy, providing durable, wear-resistant coatings for industrial tools and components.
-
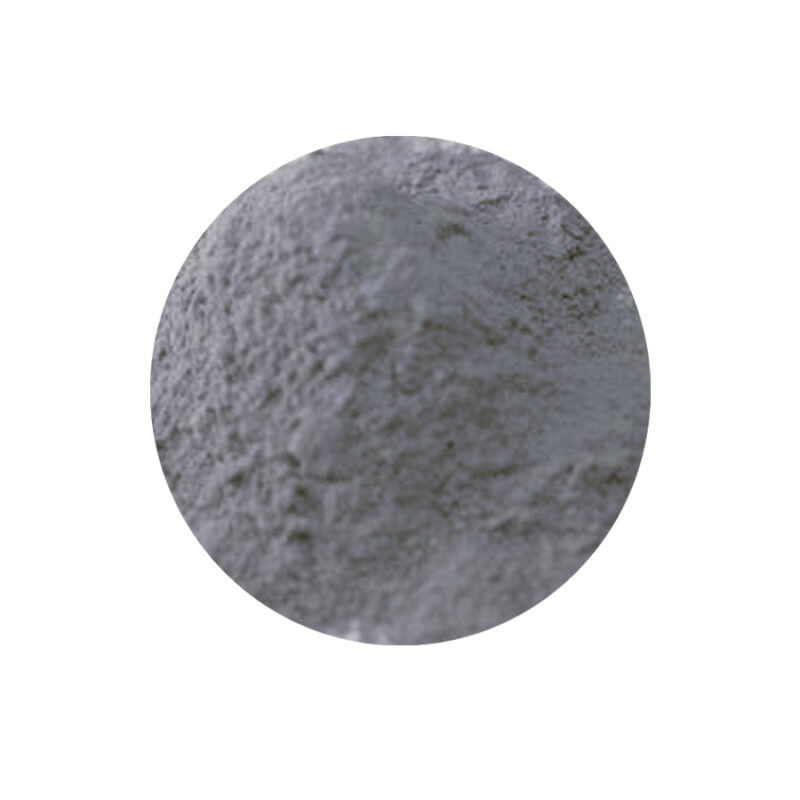
- High Purity: Available with purity levels of ≥99.5%.
- Corrosion Resistance: Provides superior resistance to rust and oxidation, making it ideal for harsh environments.
- Hardness: Chromium is known for its hardness and wear resistance, ideal for use in manufacturing high-performance alloys.
- High Melting Point: With a melting point of 1,907°C, chromium powder is highly suited for high-temperature applications.
- Versatile Applications: Used in alloy production, coating technologies, and in a range of chemical processes.
-
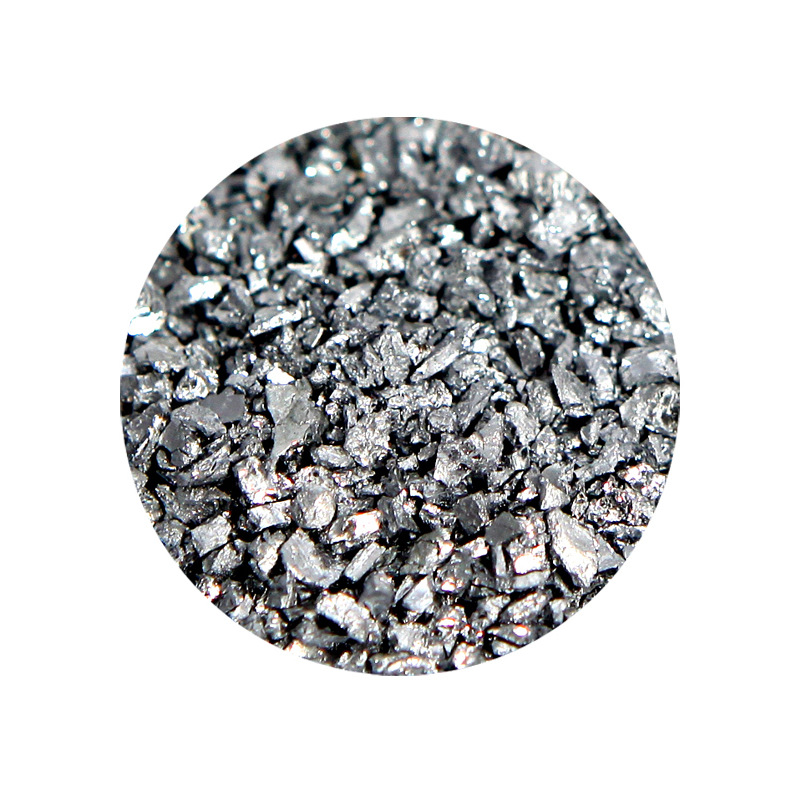
- High Hardness & Durability: Chromium thin films are known for their hardness, making them ideal for wear-resistant applications.
- High Purity: Available in high-purity forms (≥ 99.95%) to ensure optimal deposition with minimal contamination during the evaporation process.
- Excellent Adhesion: Chromium adheres well to a wide range of substrates, making it suitable for multi-layer coatings and complex material systems.
- Corrosion & Oxidation Resistance: Chromium thin films provide superior resistance to corrosion and oxidation, extending the lifespan of the coated components.
-
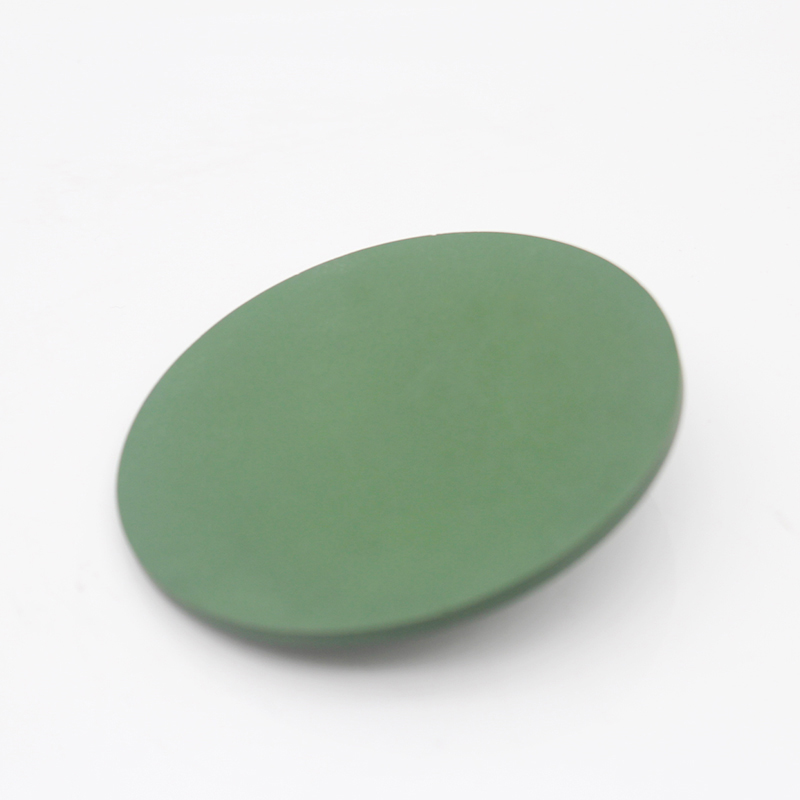
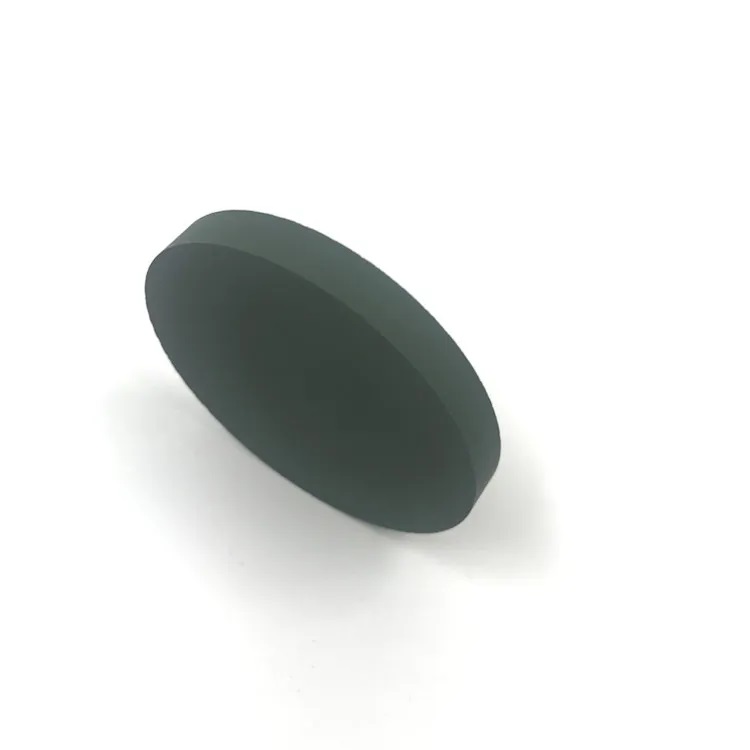
- High Hardness: Chromium oxide produces extremely hard coatings that are resistant to scratching, wear, and corrosion, ideal for industrial and mechanical applications.
- Chemical Resistance: Cr₂O₃ coatings are chemically inert and resist oxidation and corrosion, making them useful in harsh chemical environments.
- Thermal Stability: Chromium oxide has excellent thermal stability, allowing it to maintain its protective properties even at elevated temperatures.
- High IR Absorption: Due to its absorption properties in the infrared spectrum, Cr₂O₃ sputtering targets are used in coatings for IR sensors and optical devices.