Showing 1–12 of 52 results
-
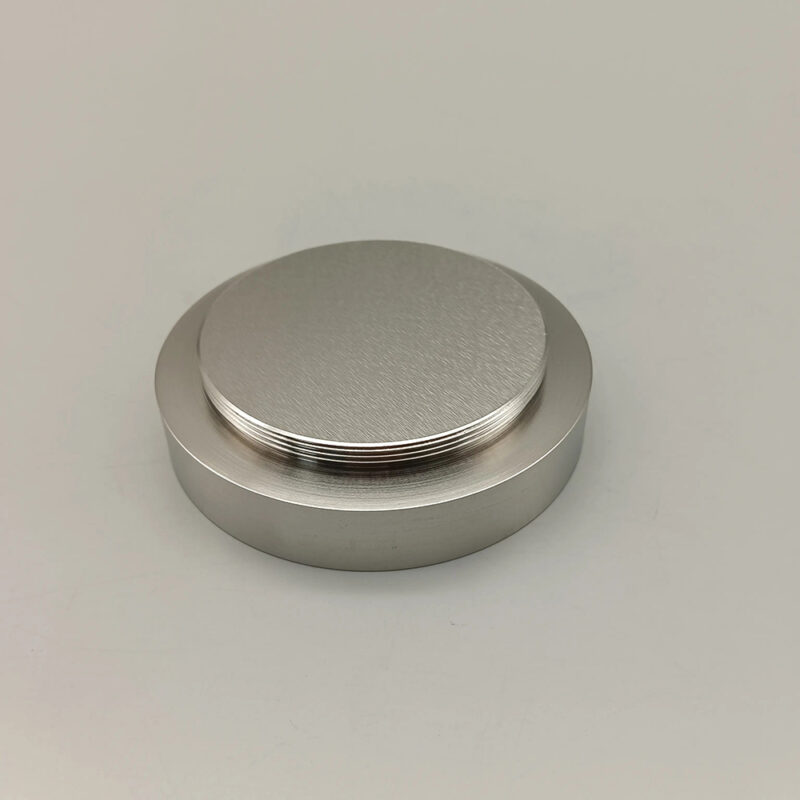
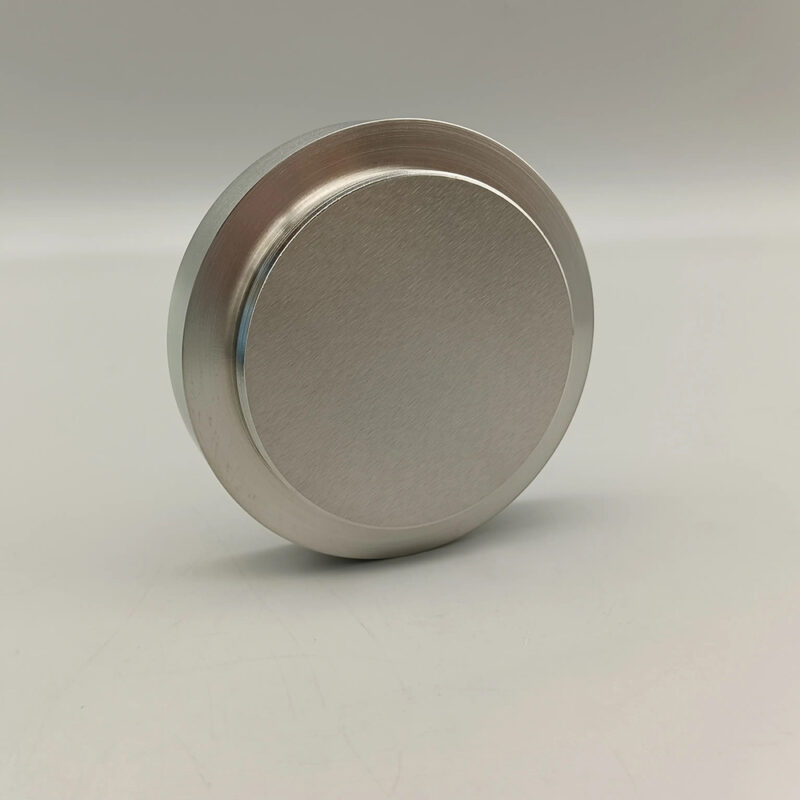
- High Mechanical Strength: The combination of aluminum, chromium, cobalt, iron, and nickel in the alloy imparts excellent mechanical strength, making it ideal for thin films that require toughness and resistance to mechanical stress.
- Superior Corrosion Resistance: Chromium and nickel contribute to the alloy’s outstanding corrosion resistance, allowing thin films to perform well in corrosive environments, such as in aerospace and marine applications.
- Thermal Stability: AlCrCoFeNi alloy thin films retain their structural properties at elevated temperatures, making them suitable for high-temperature environments, such as in engines and turbines.
- Wear Resistance: Cobalt and chromium enhance the wear resistance of the alloy, making it ideal for hard coatings in industrial tools and machinery parts.
- High-Entropy Alloy Properties: As a high-entropy alloy, AlCrCoFeNi offers a unique combination of properties that cannot be achieved with traditional alloys, including high strength, toughness, and resistance to oxidation and corrosion.
-
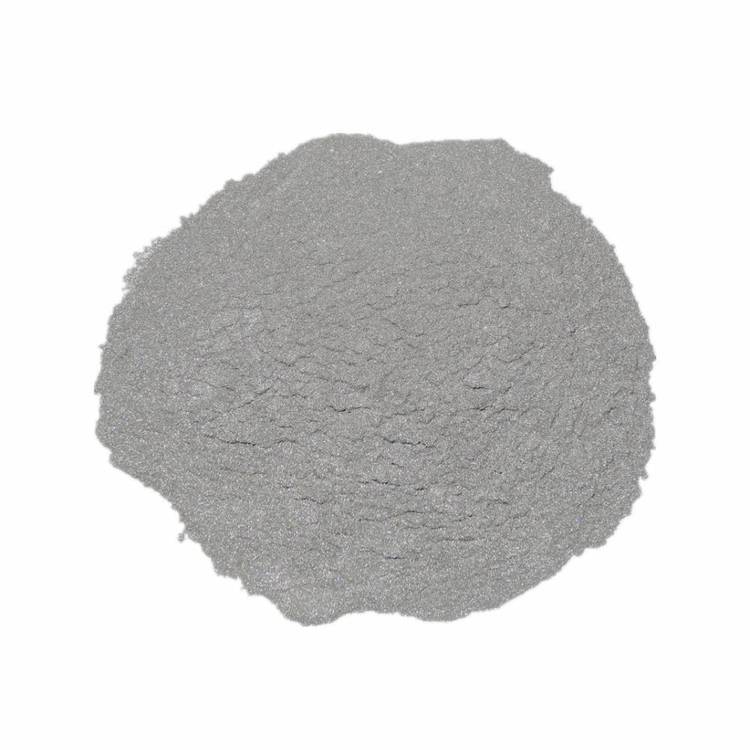
- High Strength-to-Weight Ratio: Combines the lightweight benefits of aluminum with the strength of iron.
- Thermal Stability: Resistant to high temperatures, making it ideal for demanding environments.
- Corrosion Resistance: Excellent performance in corrosive conditions.
- Customizable Particle Sizes: Suitable for diverse manufacturing processes.
- High Purity: Ensures consistent quality and performance.
- Excellent Alloying Properties: Compatible with various manufacturing techniques like powder metallurgy and additive manufacturing.
-
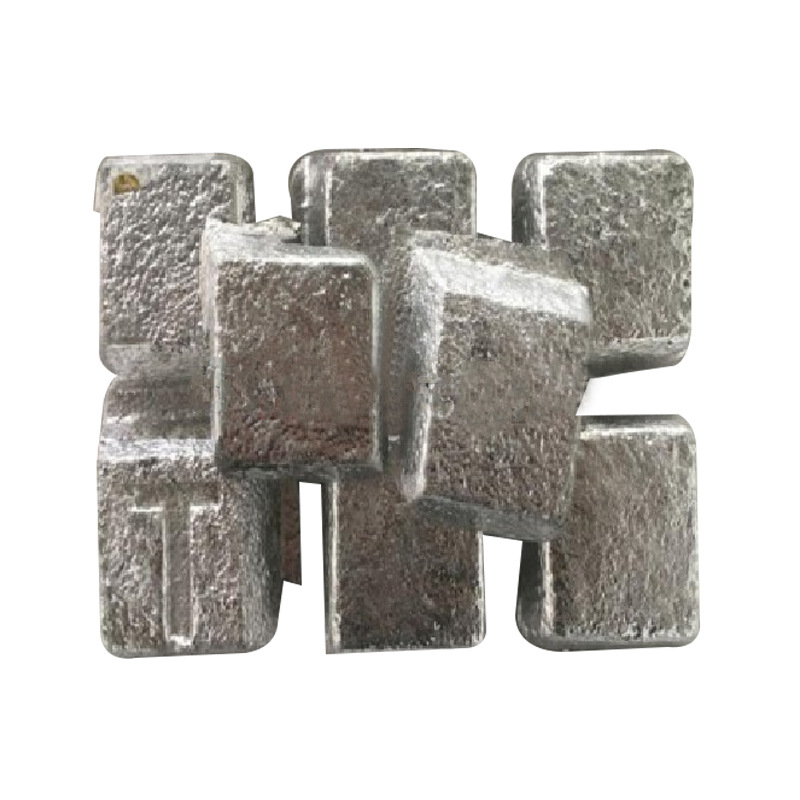
- Enhanced Strength: The iron content provides increased mechanical strength compared to pure aluminum.
- Corrosion Resistance: Improved corrosion resistance, making it suitable for harsh environments.
- Magnetic Properties: Offers magnetic characteristics beneficial for specific electronic applications.
- Versatile Deposition Techniques: Compatible with various deposition methods, including thermal evaporation and sputtering.
-
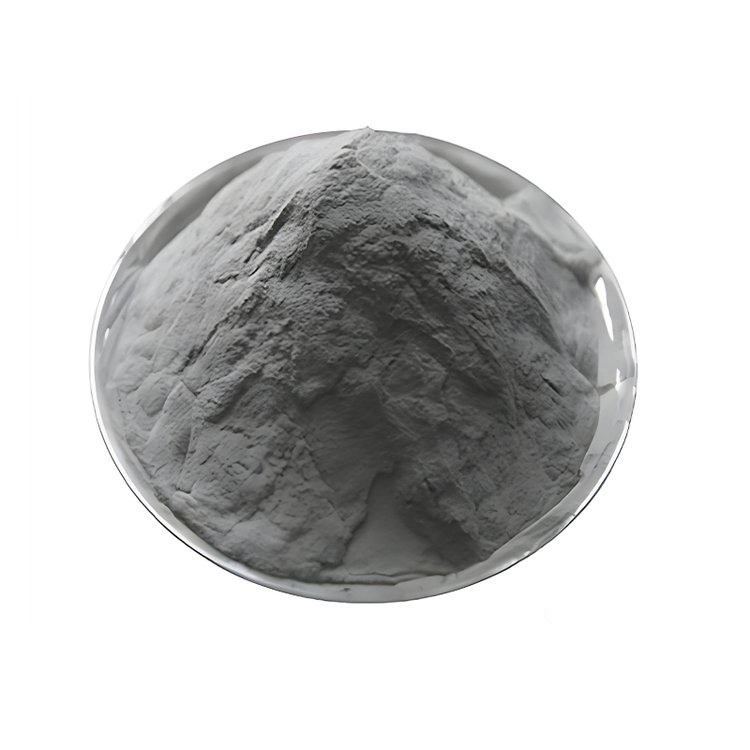
- High Strength-to-Weight Ratio: Combines lightweight characteristics with robust mechanical properties.
- Excellent Wear Resistance: Ensures durability in high-stress environments.
- Corrosion and Oxidation Resistance: Performs reliably in extreme chemical or thermal conditions.
- Uniform Microstructure: Enhances performance consistency across applications.
- Wide Applicability: Suitable for 3D printing, surface coatings, and high-performance components.
-
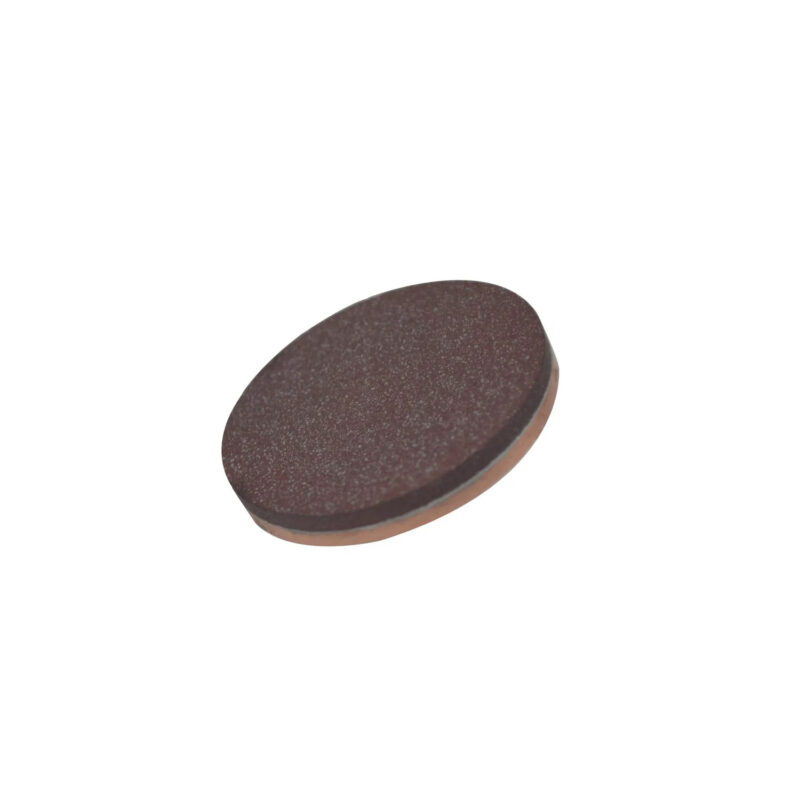
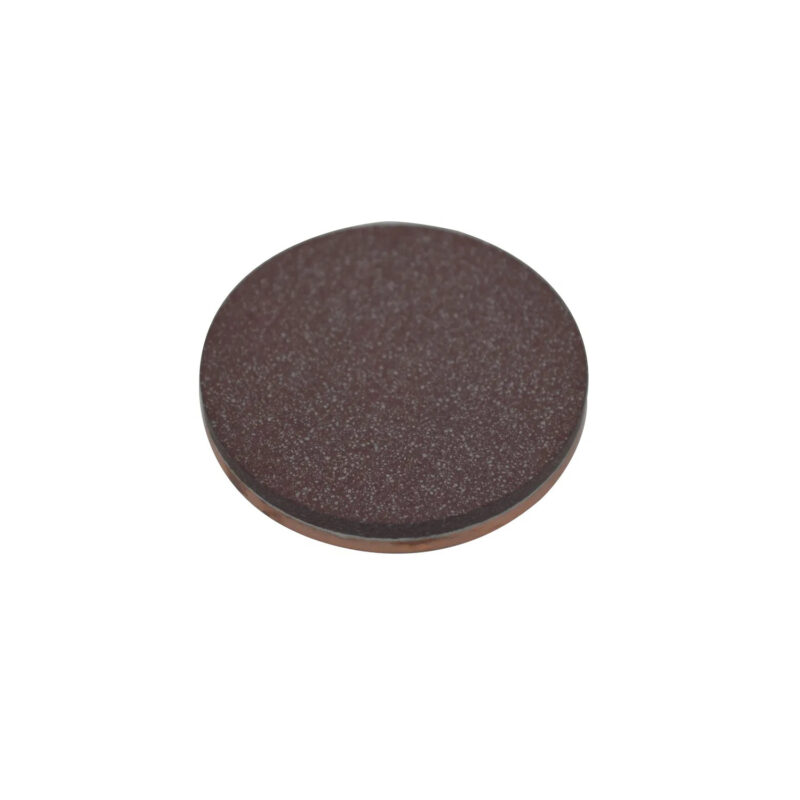
- Multiferroic Properties: BiFeO₃ demonstrates both ferroelectric and antiferromagnetic properties, making it ideal for multifunctional devices.
- Room Temperature Functionality: One of the few multiferroic materials that operates effectively at room temperature, allowing for broader application in consumer electronics and industrial devices.
- Photovoltaic Effects: BiFeO₃ can be used to create thin films that convert light into electricity, opening avenues for energy harvesting and improving photovoltaic technologies.
- Customizable: The size, shape, and purity of BiFeO₃ sputtering targets can be tailored to meet specific requirements for various deposition techniques.
-
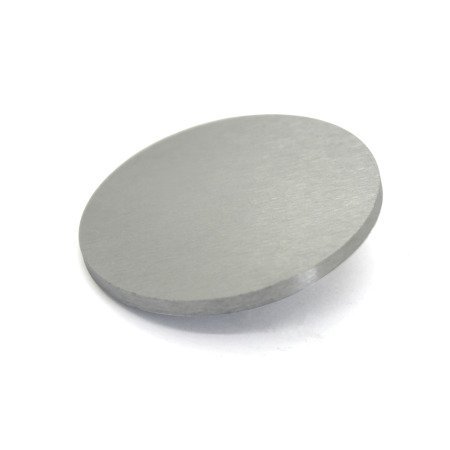
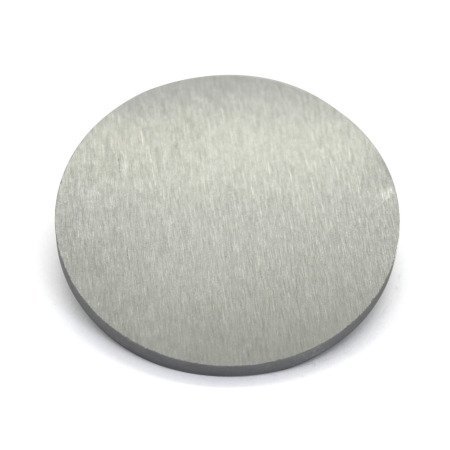
- High Purity: ≥ 99.9% purity ensures high-quality thin films with precise optical and magnetic properties.
- Superior Magneto-Optical Performance: Provides excellent Faraday rotation and low optical loss.
- Stable Composition: Chemically stable and reliable for prolonged usage.
- Customizability: Available in various shapes, sizes, and thicknesses to fit specific sputtering systems.
- Compatibility: Suitable for both RF and DC magnetron sputtering methods.
-
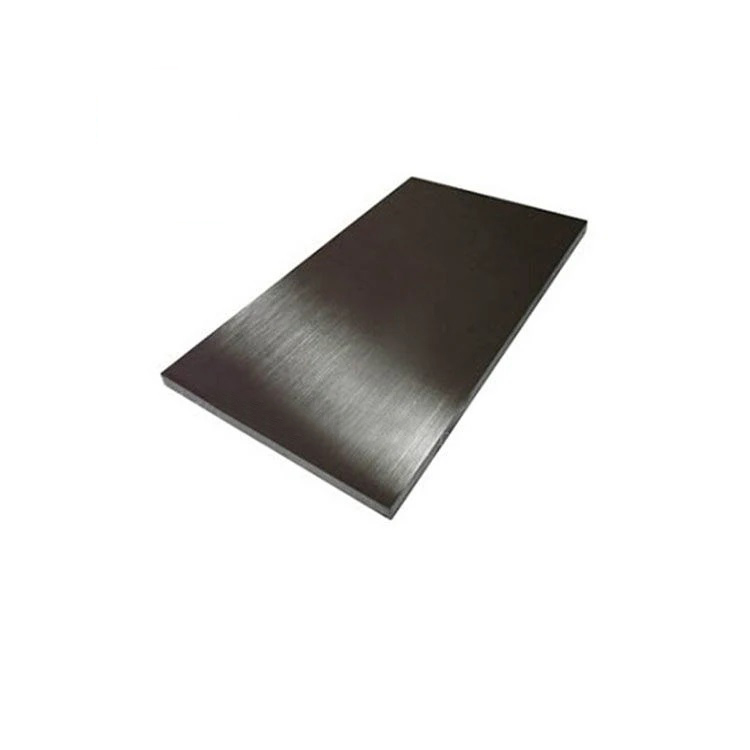
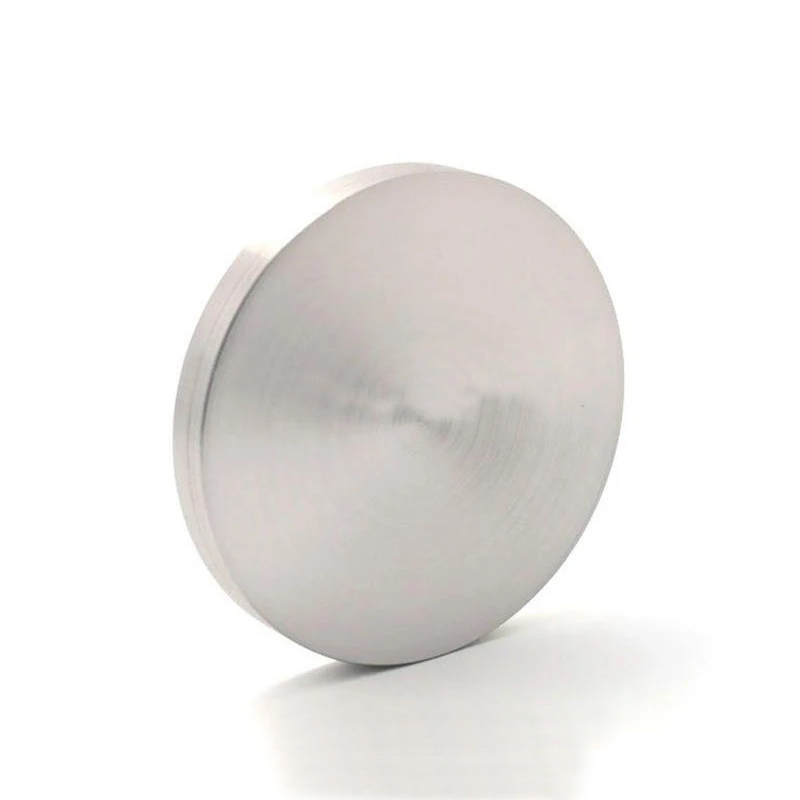
- High Saturation Magnetization: CoFe alloys exhibit one of the highest saturation magnetizations among magnetic materials, making them ideal for magnetic storage and sensor applications.
- Excellent Permeability: The alloy’s high permeability enables efficient magnetic performance, particularly in devices requiring soft magnetic properties with minimal energy loss.
- Low Coercivity: CoFe films have low coercivity, which is beneficial for reducing power losses in magnetic components and enhancing the performance of thin-film magnetic sensors and data storage devices.
- Corrosion Resistance: CoFe alloys possess good resistance to oxidation and corrosion, extending the longevity of thin-film applications in harsh environments.
- Customizable Composition: The ratio of cobalt to iron can be adjusted to fine-tune magnetic properties and optimize the sputtering target for specific applications.
-
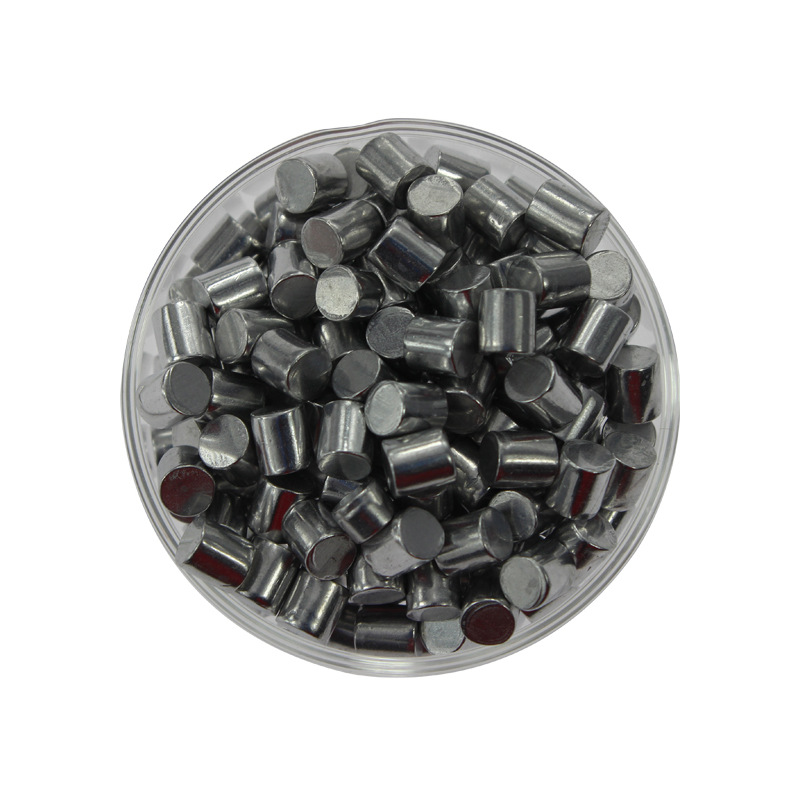
- High Magnetic Saturation: Offers strong magnetic performance, making it suitable for a range of electromagnetic applications.
- Durability: Provides good mechanical strength and resistance to wear and corrosion.
- Versatile: Can be used in various thin-film deposition techniques for diverse applications.
-
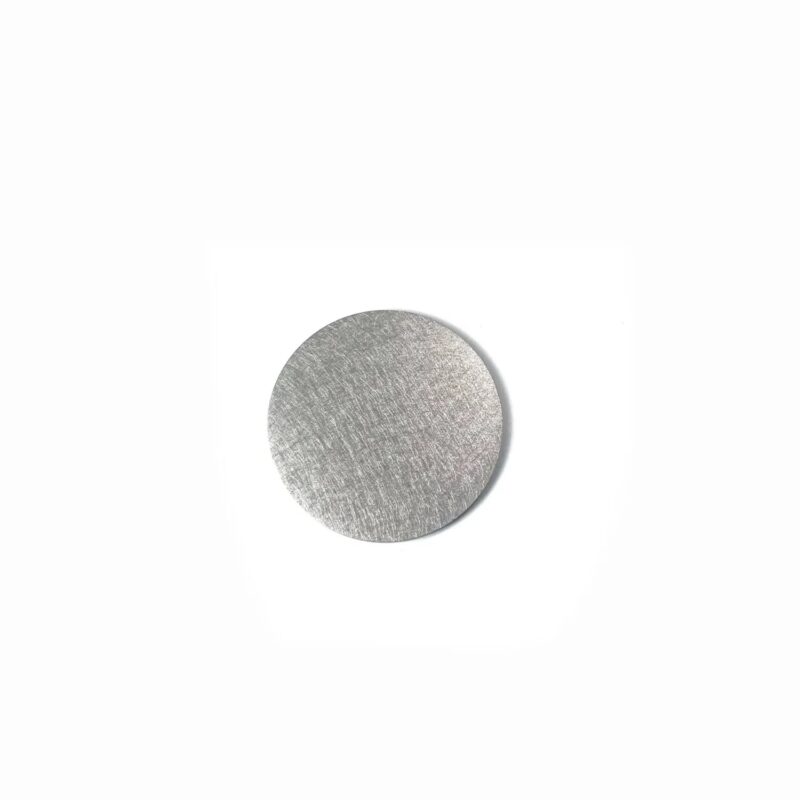
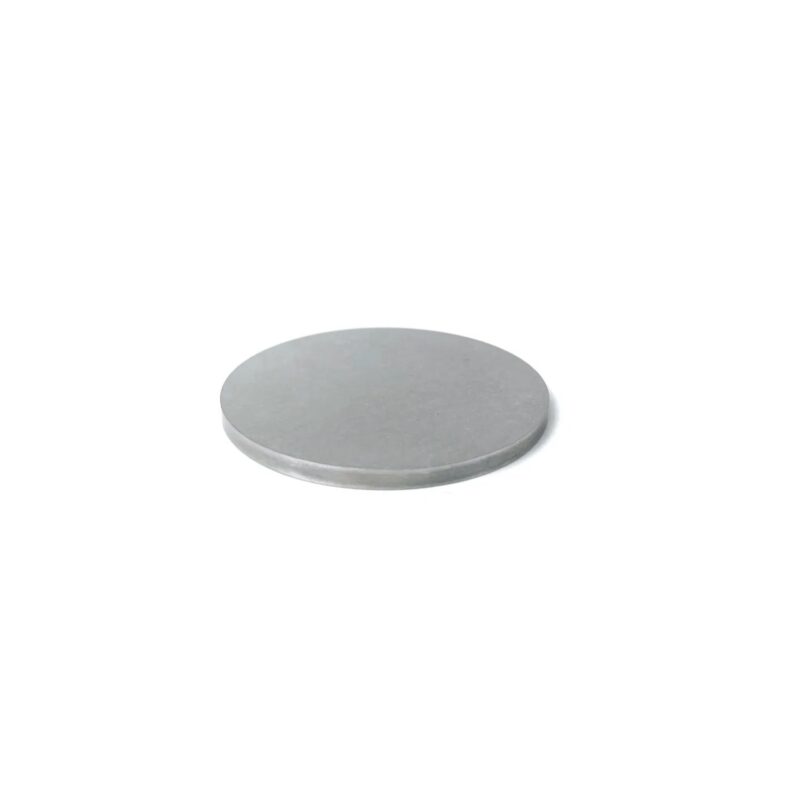
- High Magnetic Moment: CoFeB alloy exhibits a high magnetic moment, making it ideal for applications requiring strong magnetic fields, such as data storage and magnetic sensors.
- Soft Magnetic Properties: The addition of boron to the CoFe alloy improves the soft magnetic properties, reducing coercivity and allowing for efficient magnetization with minimal energy loss.
- Low Coercivity: CoFeB films have very low coercivity, contributing to higher energy efficiency and better performance in magnetic thin films and devices.
- Thermal Stability: CoFeB exhibits excellent thermal stability, maintaining its magnetic properties at elevated temperatures, making it suitable for high-performance applications.
- Tunneling Magnetoresistance (TMR): CoFeB is widely used in magnetic tunneling junctions due to its ability to produce a high tunneling magnetoresistance effect, improving the performance of MRAM and spintronic devices.
-
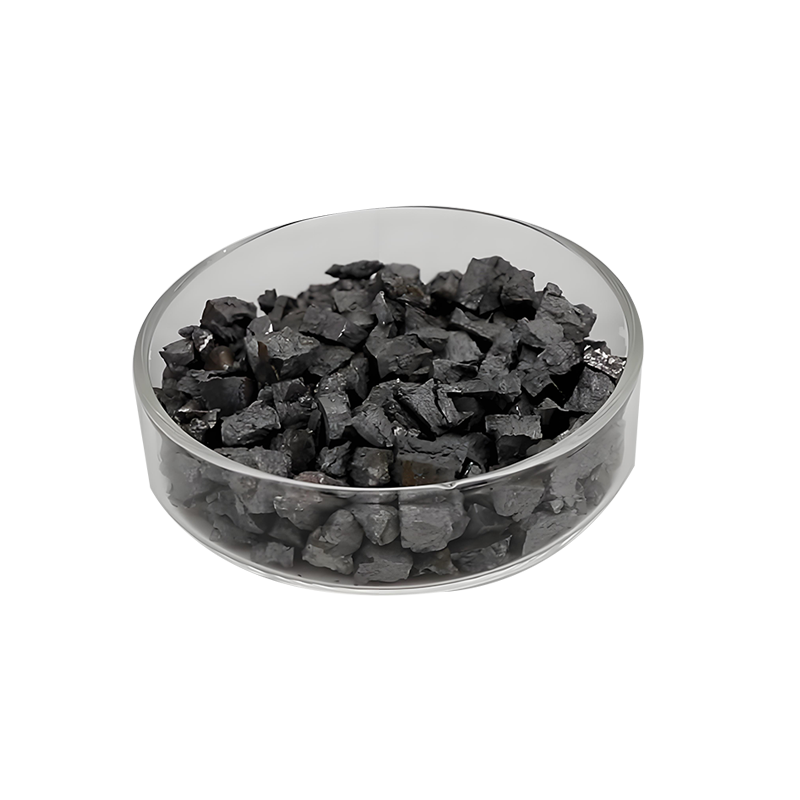
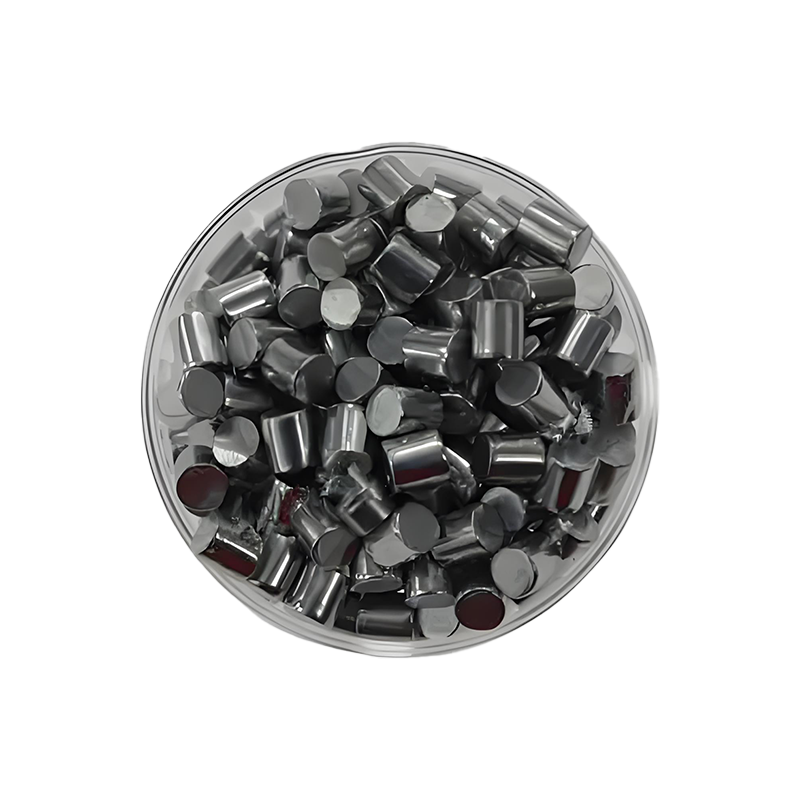
- Excellent Magnetic Properties: High saturation magnetization and low coercivity for efficient magnetic performance.
- Thermal Stability: Maintains magnetic properties under high-temperature conditions.
- Low Magnetostriction: Ensures minimal distortion in magnetic fields for precision applications.
- Customizable Composition: Available with tailored Co, Fe, and B ratios to meet specific needs.
- Versatile Particle Sizes: Suitable for nanometer to micrometer applications.
-
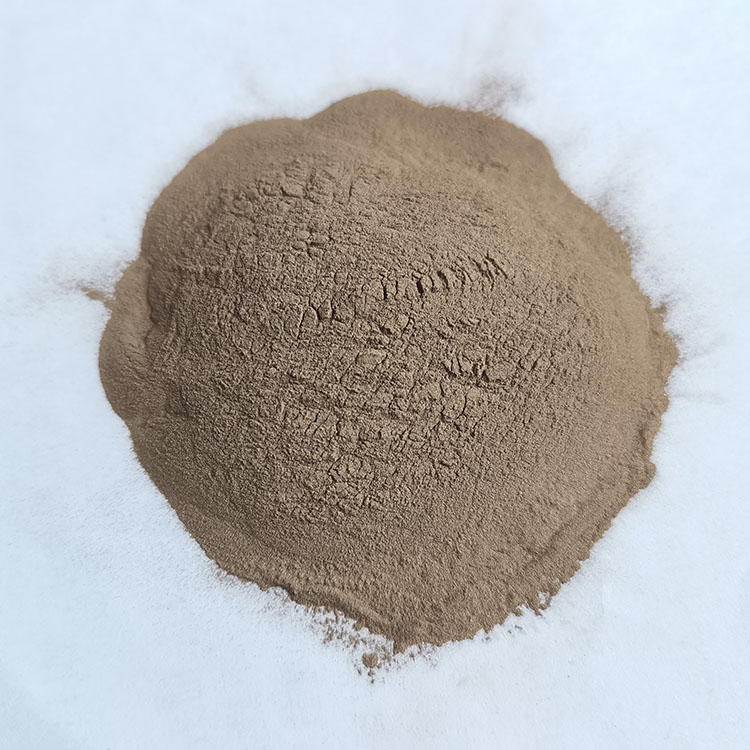
- High Electrical Conductivity: Retains copper’s excellent conductive properties.
- Mechanical Strength: Enhanced by the inclusion of iron, making it suitable for robust applications.
- Customizable Composition: Various Cu-Fe ratios tailored to specific industrial needs.
- Corrosion Resistance: Provides protection against oxidation and wear.
- Uniform Particle Size: Ensures consistency in manufacturing processes.
-
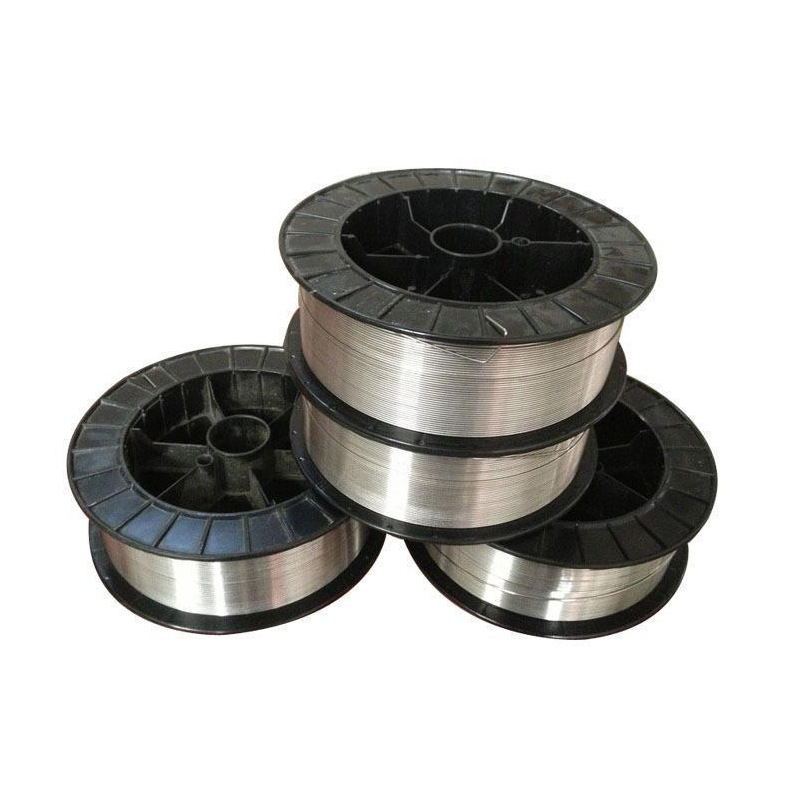
- Superior Performance in Electromagnetic Applications: The high magnetic permeability of high purity iron makes it an ideal material for manufacturing electromagnetic components such as inductors, transformers, and magnetic shielding.
- Enhanced Material Properties: The minimal presence of impurities in high purity iron improves its mechanical properties, such as ductility, tensile strength, and fatigue resistance, making it more reliable in demanding applications.
- Improved Durability: The high purity of iron ensures that it is less susceptible to failure due to impurities, offering longer-lasting performance in industrial and technological applications.
- Customization: High purity iron wire can be tailored to specific requirements, such as wire gauge, length, and coatings, for specialized applications in different industries.
- High Precision and Consistency: The uniformity of high purity iron ensures that it performs consistently in precision applications, where small variations in material properties can lead to failure.
- Cost-Effectiveness: While high purity iron wire may have a slightly higher initial cost than standard iron wire, its superior performance and longer lifespan make it a cost-effective choice in the long run, especially for advanced applications.