Showing 1–12 of 39 results
-
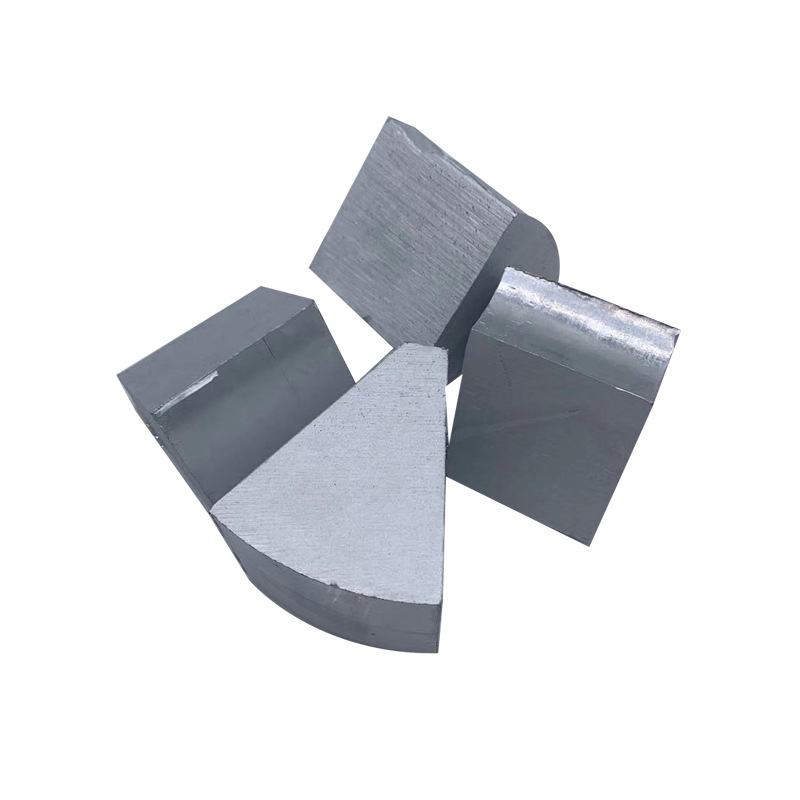
- Enhanced Strength: Molybdenum contributes to higher strength and stability at elevated temperatures.
- Good Thermal Conductivity: Provides effective heat dissipation in electronic applications.
- Corrosion Resistance: Offers improved resistance against oxidation and wear.
- Versatile Deposition: Compatible with thermal evaporation and sputtering techniques.
-
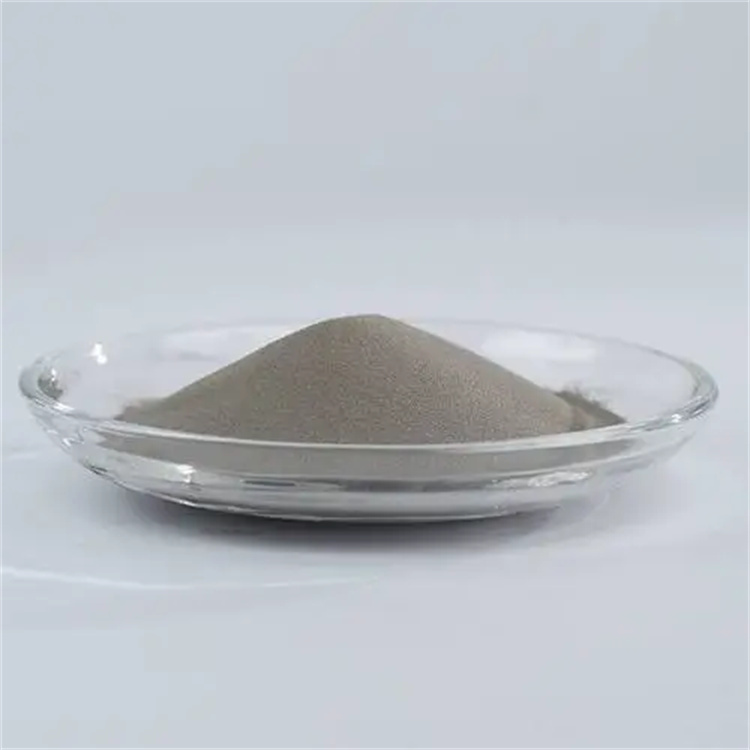
- Exceptional Corrosion Resistance: Resistant to pitting, crevice corrosion, and stress corrosion cracking in aggressive environments.
- High Strength: Maintains mechanical integrity under high stress and temperature conditions.
- Weldability: Excellent compatibility with various welding methods, including TIG, MIG, and laser welding.
- Versatility: Suitable for additive manufacturing, powder metallurgy, and thermal spray coating applications.
- Thermal Stability: Performs reliably across a wide range of temperatures without compromising material properties.
-
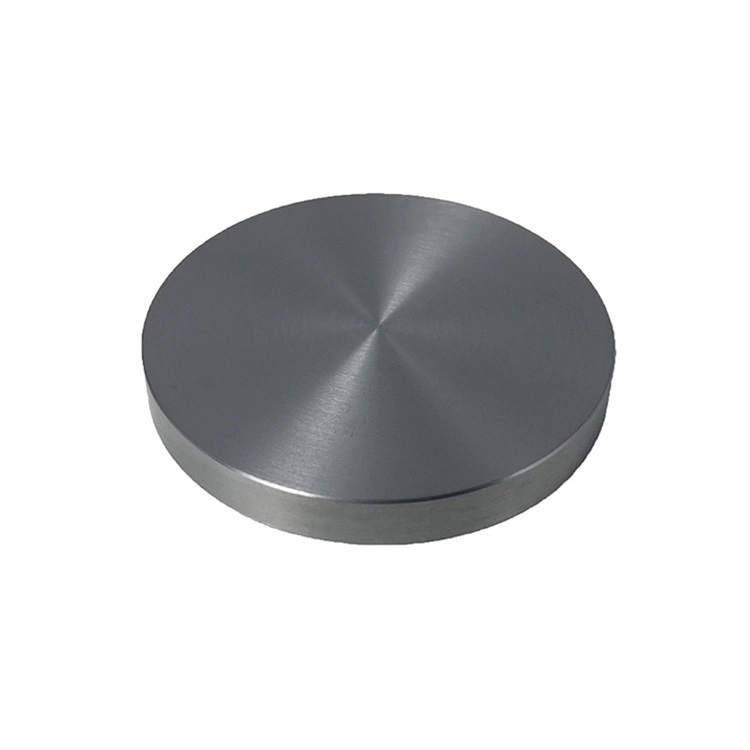
- Biocompatibility: CoCrMo alloys are highly biocompatible, making them ideal for medical implants and devices that come in contact with human tissue and bone.
- Wear Resistance: The addition of molybdenum enhances the alloy’s resistance to wear and fatigue, making CoCrMo thin films durable under mechanical stress and long-term use.
- Corrosion Resistance: Cobalt and chromium provide excellent corrosion resistance, protecting components from damage in harsh environments, including body fluids, chemicals, and marine conditions.
- Mechanical Strength: CoCrMo alloy sputtering targets produce thin films with exceptional mechanical strength, allowing coated components to withstand high loads and stresses.
- High-Temperature Stability: CoCrMo alloys retain their properties at elevated temperatures, making them suitable for applications in aerospace and industrial settings where heat resistance is critical.
-
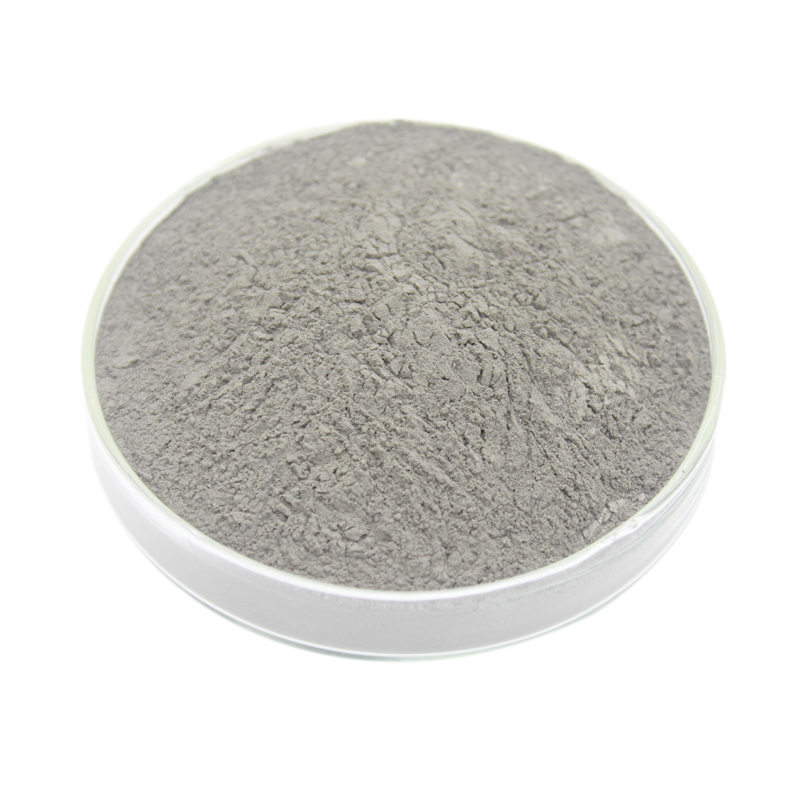
- High-Temperature Stability: Excellent performance at temperatures up to 900°C, making it suitable for aerospace and industrial applications.
- Corrosion Resistance: Outstanding resistance to oxidation and carburization in high-temperature environments.
- Superior Mechanical Strength: Maintains mechanical integrity under extreme conditions.
- Good Fabricability: Compatible with various manufacturing techniques, including additive manufacturing and welding.
- Versatility: Adaptable to multiple environments, including those with aggressive chemical exposure.
-
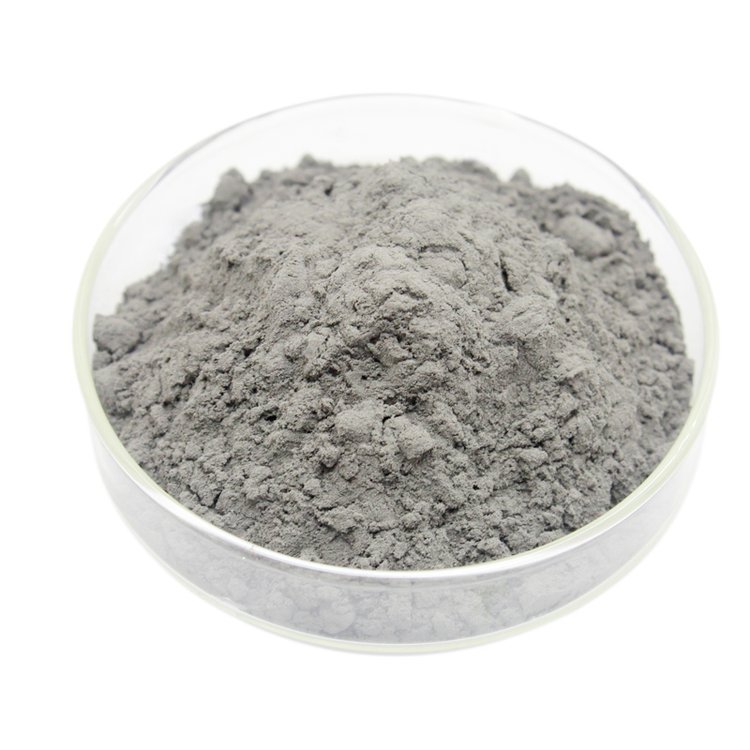
- Corrosion Resistance: Outstanding resistance to oxidation, pitting, and crevice corrosion in harsh environments.
- High-Temperature Performance: Maintains mechanical properties and structural integrity at temperatures up to 980°C.
- Exceptional Strength: Offers superior tensile, fatigue, and creep-rupture properties.
- Weldability and Fabricability: Excellent compatibility with welding and additive manufacturing processes.
- Versatile Material: Suitable for applications requiring resistance to seawater, chemicals, and high heat.
-
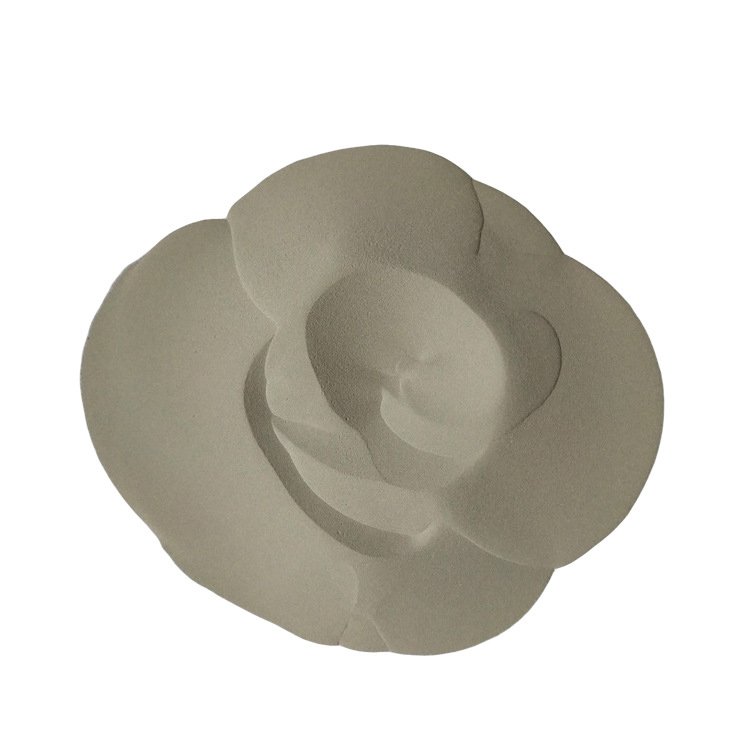
- High-Temperature Strength: Excellent strength and stability at high temperatures.
- Corrosion Resistance: Exceptional resistance to oxidation, ensuring long-term performance in harsh environments.
- Customizable Powder Sizes: Available in a range of particle sizes for various manufacturing processes.
- Enhanced Durability: Superior wear and fatigue resistance, ideal for aerospace and high-stress applications.
- Versatile: Suitable for a variety of applications including additive manufacturing, powder metallurgy, and casting.
-
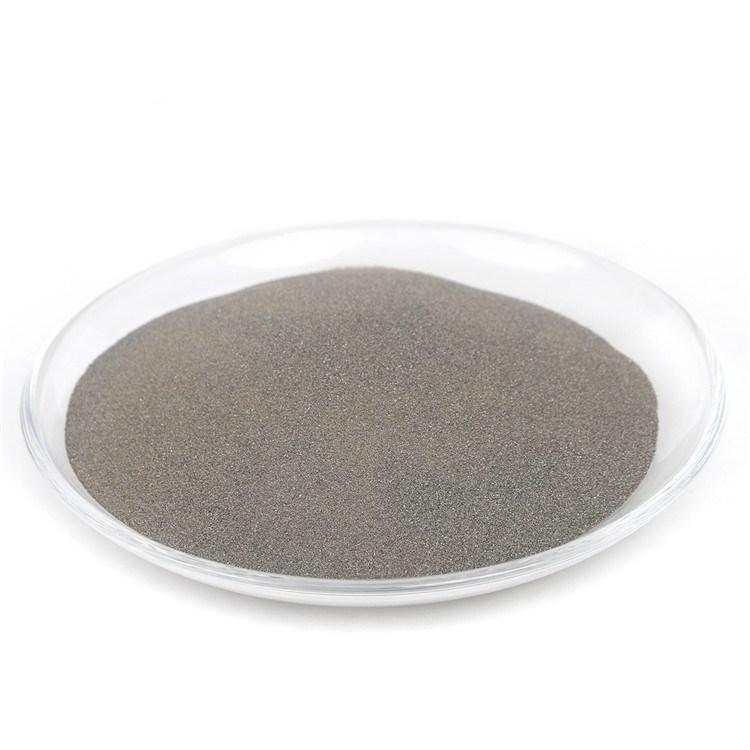
- High-Temperature Performance: Exceptional resistance to high temperatures, maintaining strength and stability.
- Corrosion and Oxidation Resistance: Designed for longevity in extreme environments, resistant to high-temperature oxidation and corrosion.
- Good Weldability: Excellent ability to be welded, ensuring high-quality and durable joints in complex components.
- Superior Durability: High fatigue resistance, making it ideal for components exposed to repeated stress and thermal cycling.
- Versatile Applications: Suitable for additive manufacturing, powder metallurgy, and casting processes for precision parts.
-
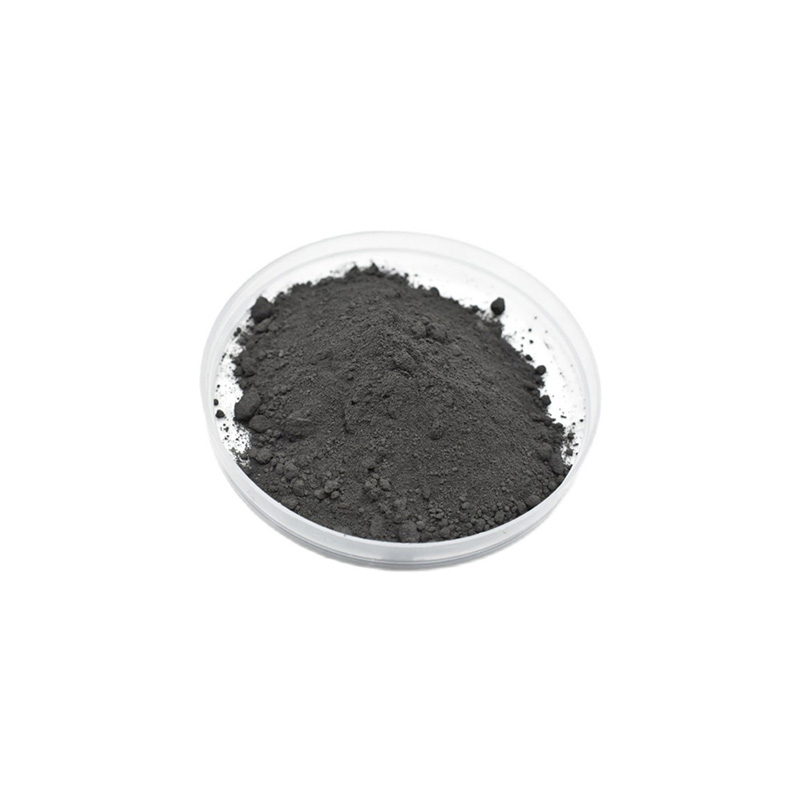
- High-Temperature Strength: Outstanding strength retention at elevated temperatures, ensuring long-term performance in extreme conditions.
- Excellent Corrosion and Oxidation Resistance: Designed to perform under high temperatures, with superior resistance to oxidation and corrosion in aggressive environments.
- Good Fabrication Characteristics: Offers excellent weldability, making it suitable for complex, high-precision components.
- Fatigue Resistance: Exceptional fatigue resistance, ideal for components exposed to cyclical thermal and mechanical stress.
- Versatile Manufacturing Options: Suitable for use in powder metallurgy, casting, and additive manufacturing processes.
-
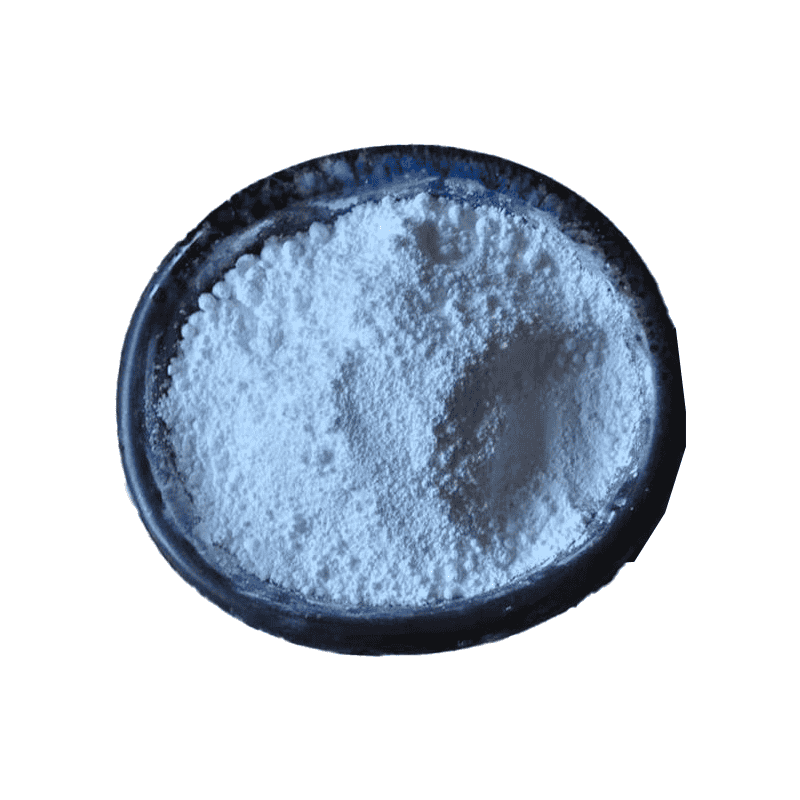
- High-Temperature Strength: Retains superior mechanical properties at elevated temperatures, ensuring long-term reliability in harsh conditions.
- Oxidation and Corrosion Resistance: Exceptional resistance to oxidation and corrosion, even in extreme high-temperature environments.
- Excellent Castability: Ideal for casting applications due to its excellent moldability and resistance to thermal fatigue.
- Versatile Manufacturing: Compatible with additive manufacturing, powder metallurgy, and traditional casting methods.
- High-Precision Components: Suitable for applications that require high-performance parts with precision and minimal defects.
-
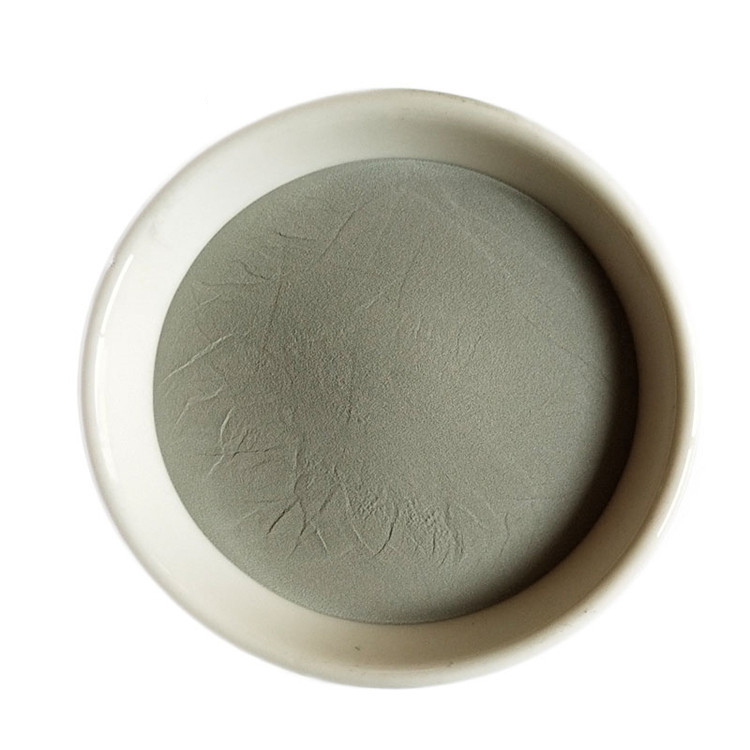
- High-Temperature Performance: Outstanding mechanical strength and creep resistance at elevated temperatures.
- Oxidation and Corrosion Resistance: Excellent resistance to oxidation and hot corrosion, ensuring long-term durability.
- Low Carbon Content: Reduces susceptibility to carbide precipitation, improving fatigue resistance.
- Exceptional Castability: Optimized for precision casting applications, with excellent mold-filling capabilities.
- Versatile Applications: Compatible with powder metallurgy and additive manufacturing for complex component production.
-
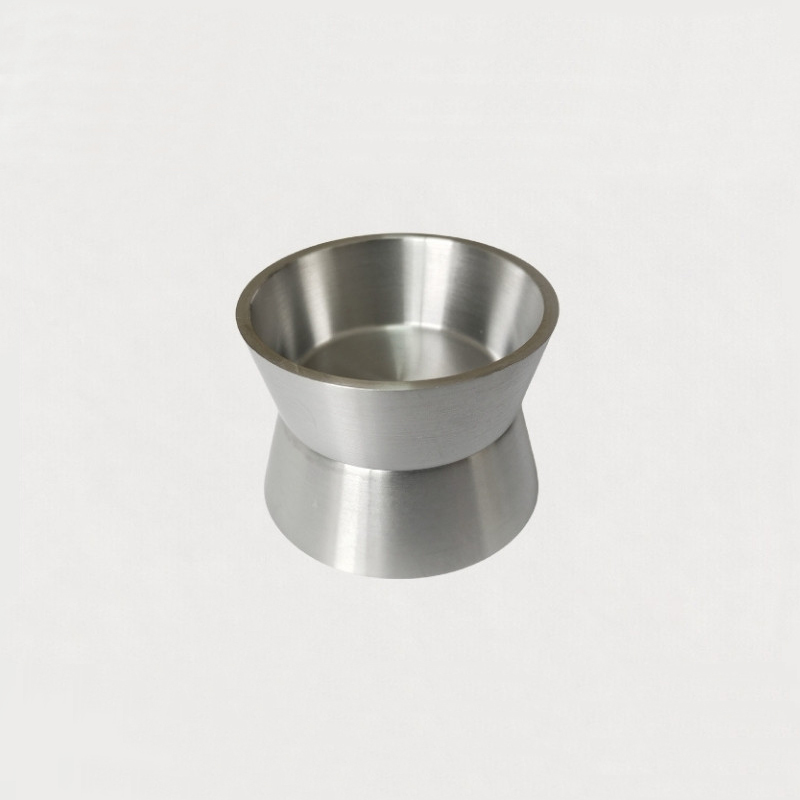
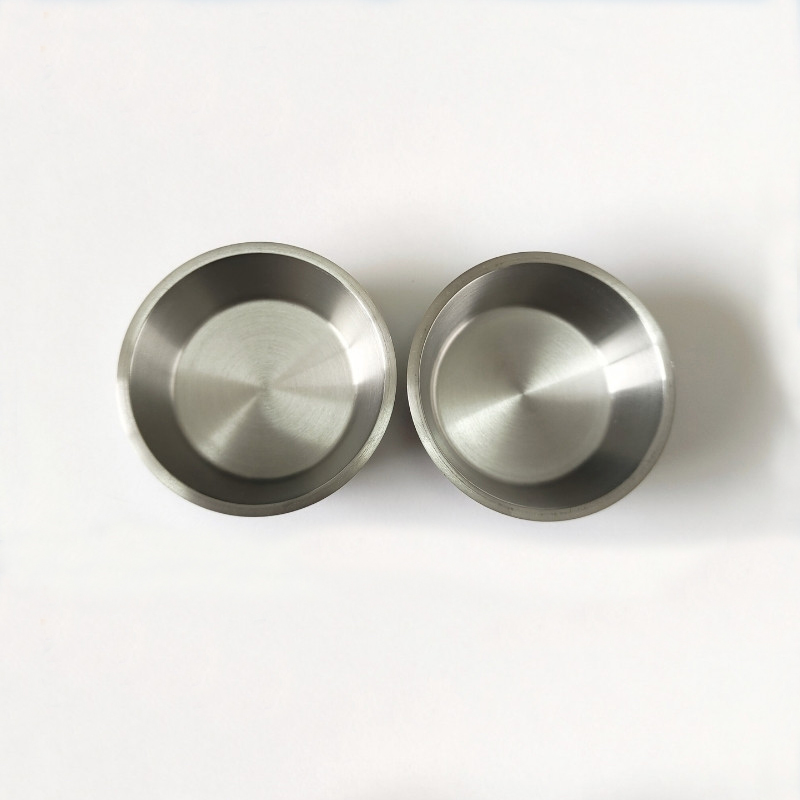
$1.00
- High Melting Point: With a melting point of 2,623°C, molybdenum crucibles are ideal for ultra-high-temperature environments.
- Thermal Stability: Maintains strength and stability at elevated temperatures, ensuring consistent performance.
- Corrosion Resistance: Excellent resistance to chemical corrosion, particularly in reducing atmospheres and molten metals.
- Mechanical Strength: High tensile strength and resistance to deformation, even under thermal stress.
- High Thermal Conductivity: Efficient heat distribution, essential for uniform thermal processes.
- Low Thermal Expansion: Minimal dimensional changes under thermal cycling reduce the risk of cracking or warping.
-
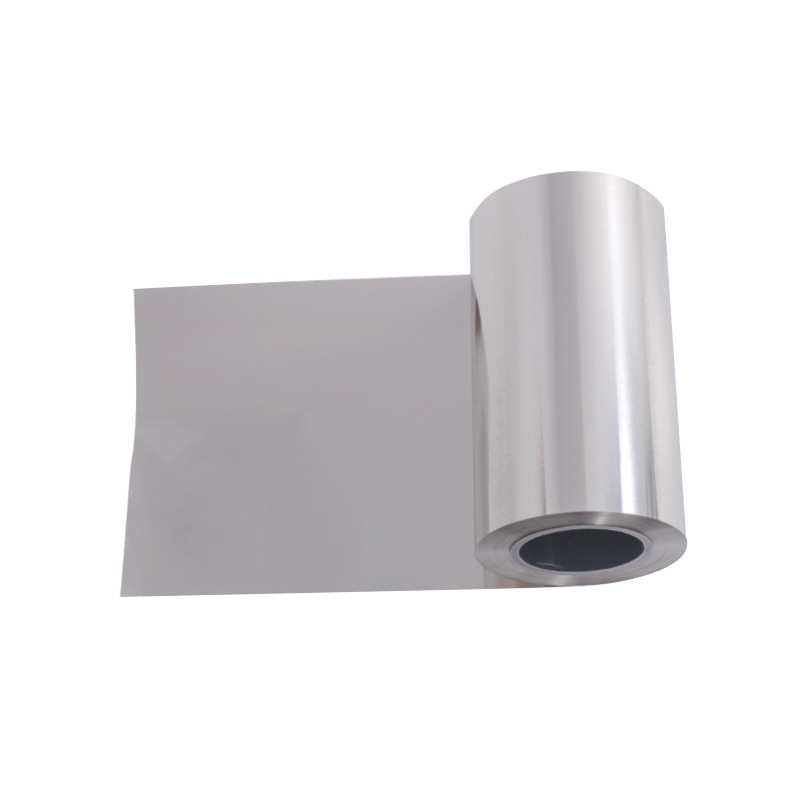
- High Melting Point: With a melting point of 2623°C, molybdenum foil can withstand extreme temperatures.
- Thermal and Electrical Conductivity: Molybdenum exhibits excellent thermal and electrical conductivity, essential for heat dissipation and electrical components.
- High Purity: Available in ultra-high purity grades, ensuring consistent performance in sensitive applications.
- Corrosion Resistance: Molybdenum is highly resistant to oxidation and corrosion, even in extreme environments.
- Strength and Stability: Molybdenum foil maintains mechanical strength and dimensional stability at high temperatures.
- Malleability and Workability: Despite its robustness, molybdenum foil is malleable and can be fabricated into complex shapes.