Showing 13–24 of 43 results
-
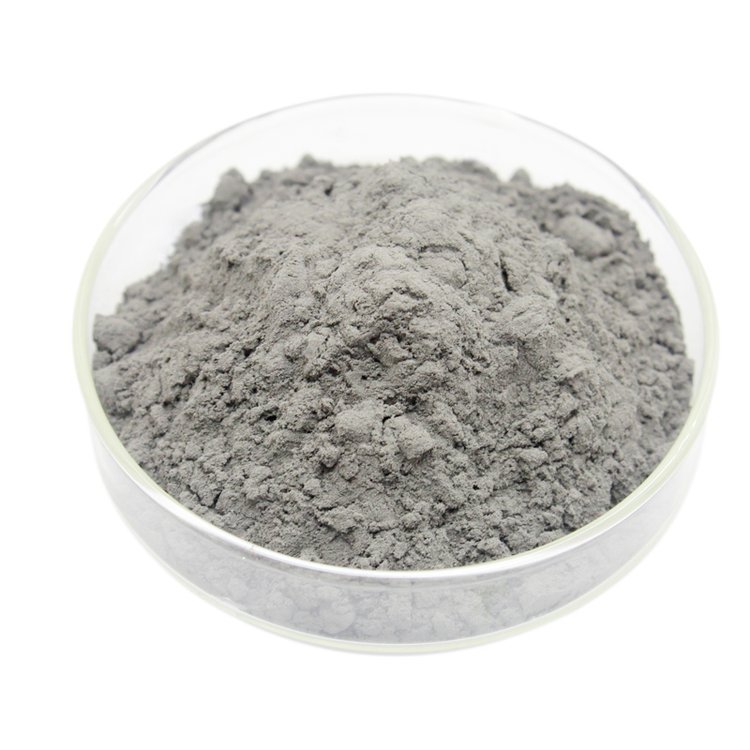
- Corrosion Resistance: Outstanding resistance to oxidation, pitting, and crevice corrosion in harsh environments.
- High-Temperature Performance: Maintains mechanical properties and structural integrity at temperatures up to 980°C.
- Exceptional Strength: Offers superior tensile, fatigue, and creep-rupture properties.
- Weldability and Fabricability: Excellent compatibility with welding and additive manufacturing processes.
- Versatile Material: Suitable for applications requiring resistance to seawater, chemicals, and high heat.
-
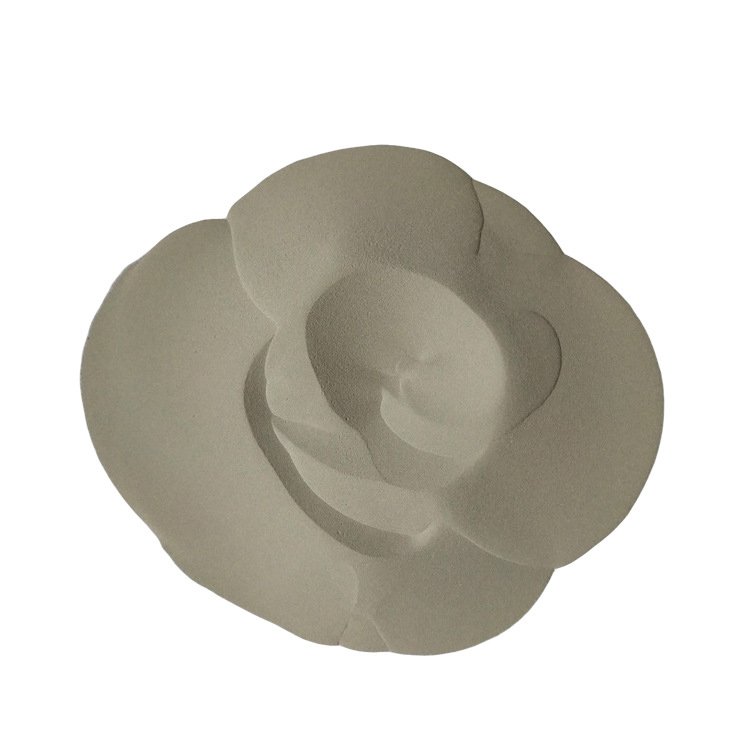
- High-Temperature Strength: Excellent strength and stability at high temperatures.
- Corrosion Resistance: Exceptional resistance to oxidation, ensuring long-term performance in harsh environments.
- Customizable Powder Sizes: Available in a range of particle sizes for various manufacturing processes.
- Enhanced Durability: Superior wear and fatigue resistance, ideal for aerospace and high-stress applications.
- Versatile: Suitable for a variety of applications including additive manufacturing, powder metallurgy, and casting.
-
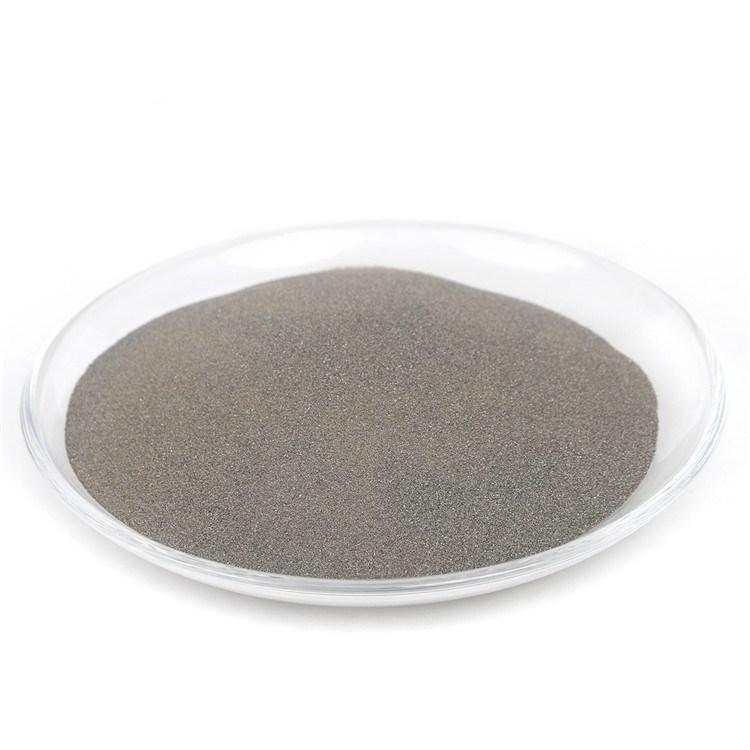
- High-Temperature Performance: Exceptional resistance to high temperatures, maintaining strength and stability.
- Corrosion and Oxidation Resistance: Designed for longevity in extreme environments, resistant to high-temperature oxidation and corrosion.
- Good Weldability: Excellent ability to be welded, ensuring high-quality and durable joints in complex components.
- Superior Durability: High fatigue resistance, making it ideal for components exposed to repeated stress and thermal cycling.
- Versatile Applications: Suitable for additive manufacturing, powder metallurgy, and casting processes for precision parts.
-
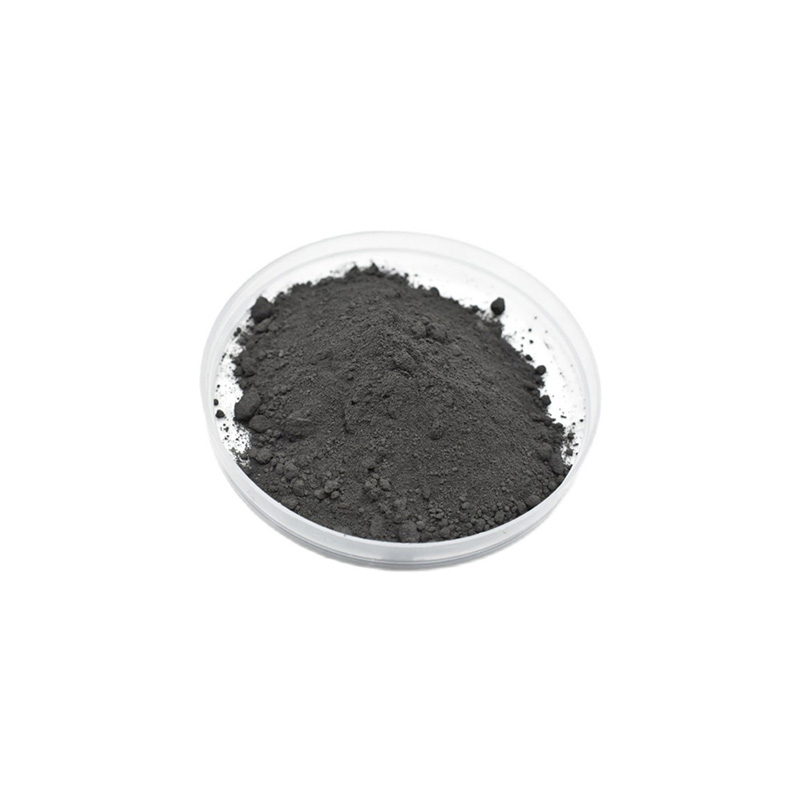
- High-Temperature Strength: Outstanding strength retention at elevated temperatures, ensuring long-term performance in extreme conditions.
- Excellent Corrosion and Oxidation Resistance: Designed to perform under high temperatures, with superior resistance to oxidation and corrosion in aggressive environments.
- Good Fabrication Characteristics: Offers excellent weldability, making it suitable for complex, high-precision components.
- Fatigue Resistance: Exceptional fatigue resistance, ideal for components exposed to cyclical thermal and mechanical stress.
- Versatile Manufacturing Options: Suitable for use in powder metallurgy, casting, and additive manufacturing processes.
-
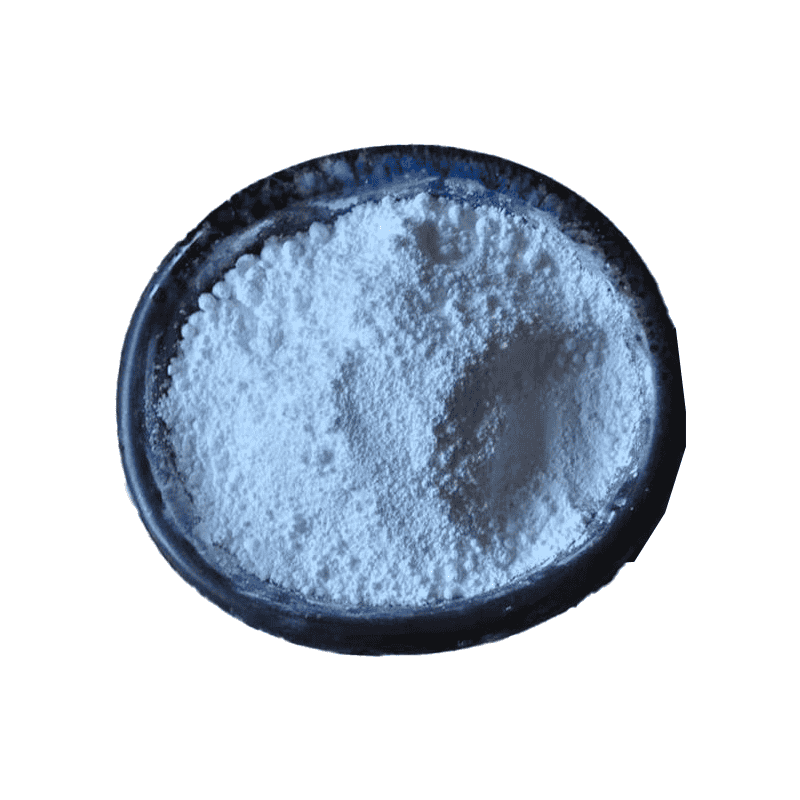
- High-Temperature Strength: Retains superior mechanical properties at elevated temperatures, ensuring long-term reliability in harsh conditions.
- Oxidation and Corrosion Resistance: Exceptional resistance to oxidation and corrosion, even in extreme high-temperature environments.
- Excellent Castability: Ideal for casting applications due to its excellent moldability and resistance to thermal fatigue.
- Versatile Manufacturing: Compatible with additive manufacturing, powder metallurgy, and traditional casting methods.
- High-Precision Components: Suitable for applications that require high-performance parts with precision and minimal defects.
-
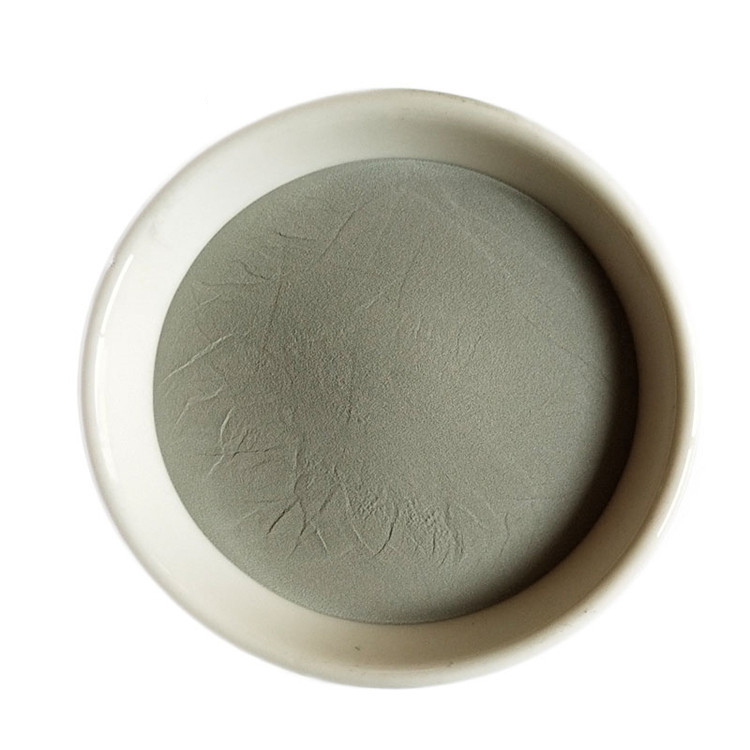
- High-Temperature Performance: Outstanding mechanical strength and creep resistance at elevated temperatures.
- Oxidation and Corrosion Resistance: Excellent resistance to oxidation and hot corrosion, ensuring long-term durability.
- Low Carbon Content: Reduces susceptibility to carbide precipitation, improving fatigue resistance.
- Exceptional Castability: Optimized for precision casting applications, with excellent mold-filling capabilities.
- Versatile Applications: Compatible with powder metallurgy and additive manufacturing for complex component production.
-
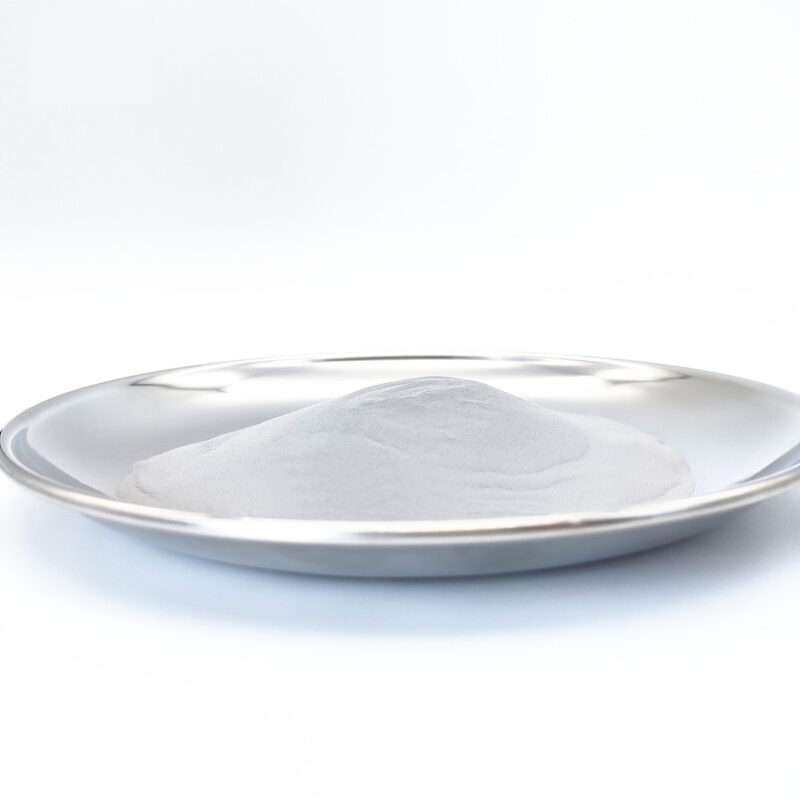
- Corrosion Resistance: Excellent performance in seawater, acidic, and alkaline environments.
- High Strength: Maintains structural integrity under stress and extreme conditions.
- Versatile Fabrication: Ideal for welding, machining, and advanced manufacturing techniques.
- Thermal Stability: Performs reliably at both low and high temperatures.
- Non-Magnetic: Retains non-magnetic properties in various conditions.
-
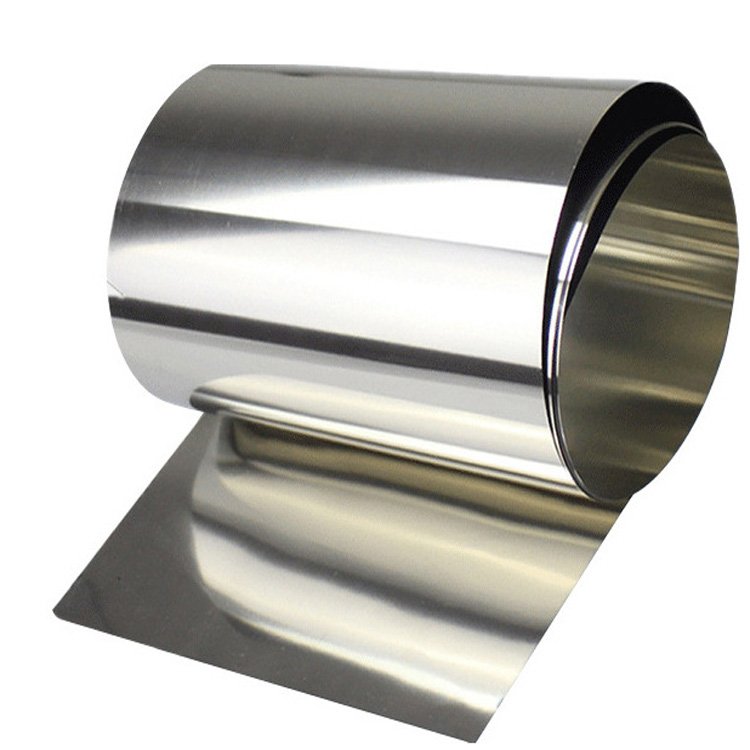
- Corrosion Resistance: Nickel foil is highly resistant to corrosion, especially in harsh environments, making it suitable for applications in corrosive conditions like chemical processing and marine industries.
- High Thermal Stability: Nickel foil maintains its performance at high temperatures, ensuring stable functionality in high-heat applications such as furnaces and heat exchangers.
- Excellent Electrical Conductivity: Known for its good electrical conductivity, nickel foil is used in the electronics industry for components like batteries, capacitors, and electrical connections.
- Malleability and Flexibility: Nickel foil is malleable and can be easily shaped into thin sheets, which is beneficial for precision applications that require flexibility.
- Magnetic Properties: Nickel exhibits ferromagnetic properties, making it ideal for use in magnetic shielding applications and other electromagnetic devices.
- Durability and Strength: Nickel foil is tough and resistant to wear and tear, ensuring long-lasting performance in demanding applications.
-
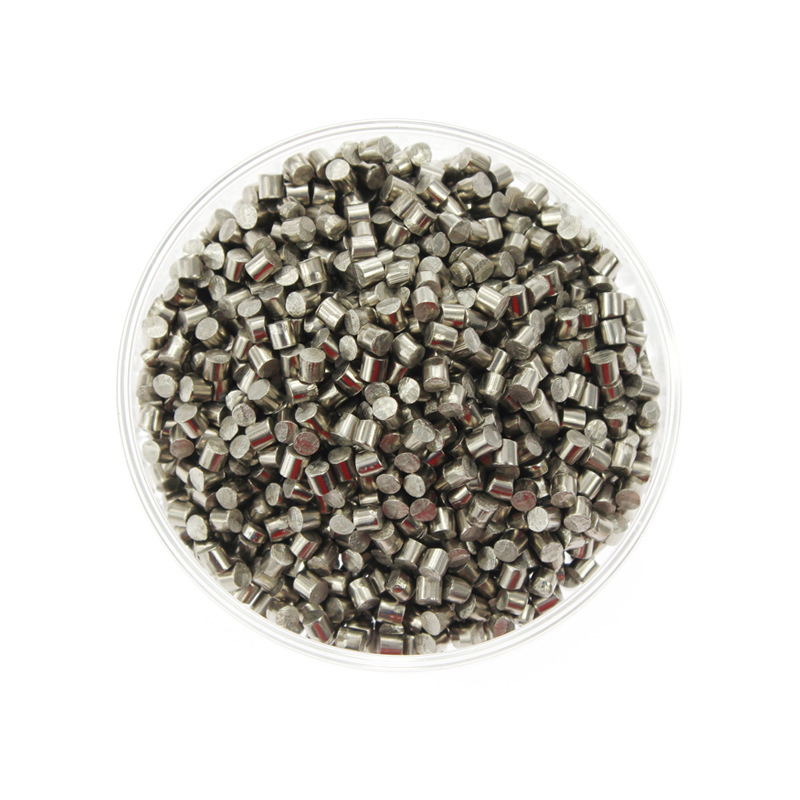
- High Purity: Nickel pellets are available with purity levels of ≥ 99.9%, ensuring superior quality films.
- Uniform Shape: Designed for smooth and consistent evaporation, providing uniform film thickness.
- High Conductivity: Excellent thermal and electrical conductivity make it ideal for electronic and thermal applications.
- Corrosion Resistance: Nickel’s natural resistance to oxidation ensures long-lasting coatings in corrosive environments.
- Magnetic Properties: Suitable for applications that require magnetic thin films.
-
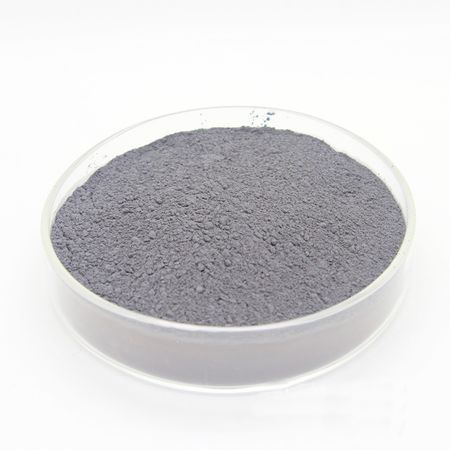
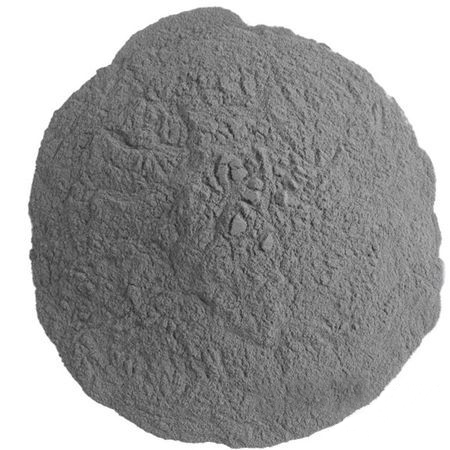
- High Purity: Ensures superior performance in critical applications.
- Corrosion Resistance: Exceptional resistance to oxidation and harsh environments.
- Thermal Stability: Performs reliably under high-temperature conditions.
- Excellent Conductivity: High electrical and thermal conductivity for electronic and energy applications.
- Customizable Particle Sizes: From nano to micrometer scales for specific industrial needs.
- Versatile Applications: Suitable for batteries, coatings, catalysts, and additive manufacturing.
-
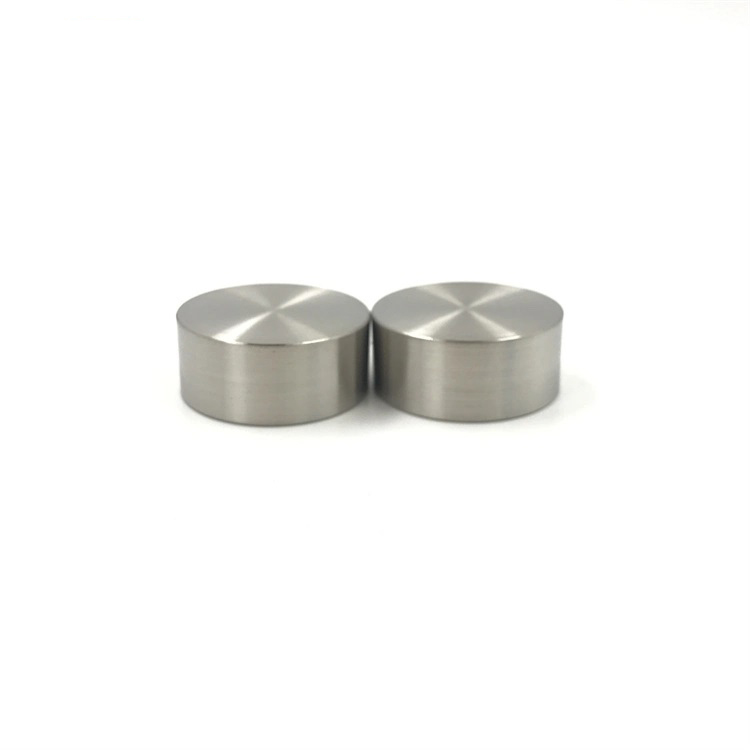
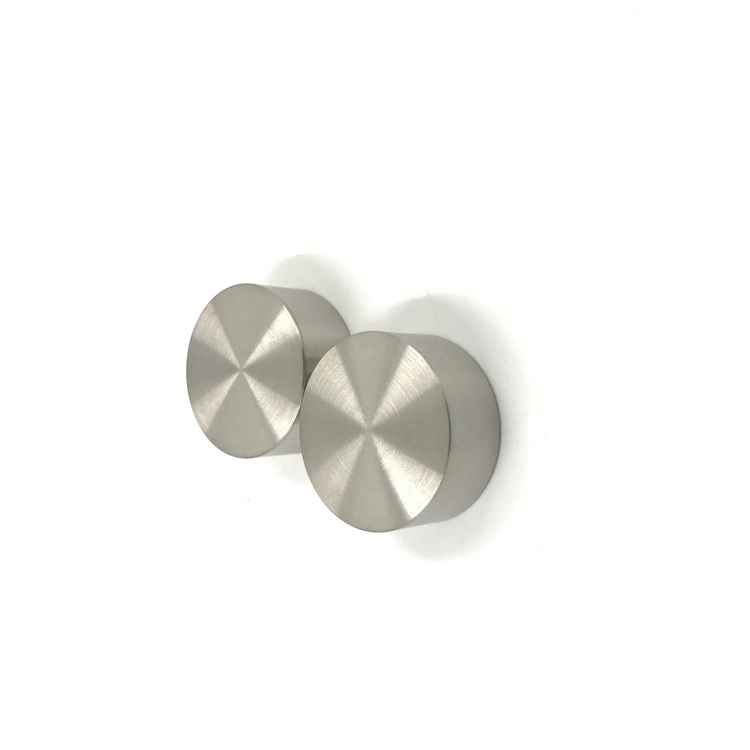
- Thickness: The thickness of the nickel coating can be precisely controlled during the sputtering process, allowing for customized solutions to meet specific application needs.
- Alloys: Nickel sputtering targets can be produced as pure nickel or in alloyed forms, such as nickel-cobalt (Ni-Co) or nickel-chromium (Ni-Cr), depending on the desired properties of the thin film.
- Backing Plates: Nickel targets can be bonded to backing plates made from materials like copper or molybdenum to improve thermal conductivity and mechanical stability during the sputtering process.
-
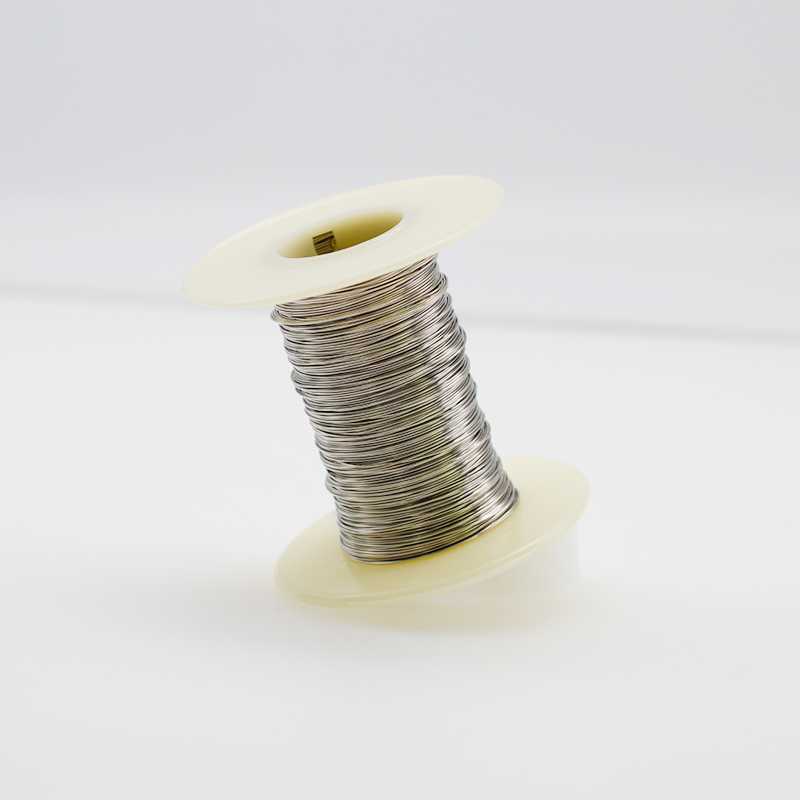
- High Corrosion Resistance: Nickel wire is highly resistant to oxidation and corrosion, especially in harsh environments, such as acidic or alkaline conditions.
- Excellent Electrical Conductivity: Offers stable and reliable electrical conductivity, making it ideal for electrical and electronic applications.
- Thermal Resistance: Can withstand high temperatures without degrading, making it suitable for heat-intensive processes.
- Ductility and Workability: Highly malleable and ductile, allowing it to be drawn into thin wires or shaped for specific applications.
- Magnetic Properties: Nickel exhibits ferromagnetic properties, enabling its use in magnetic and electronic components.
- High Melting Point: Nickel has a melting point of 1455°C, allowing it to maintain performance under extreme conditions.