Showing 25–36 of 56 results
-
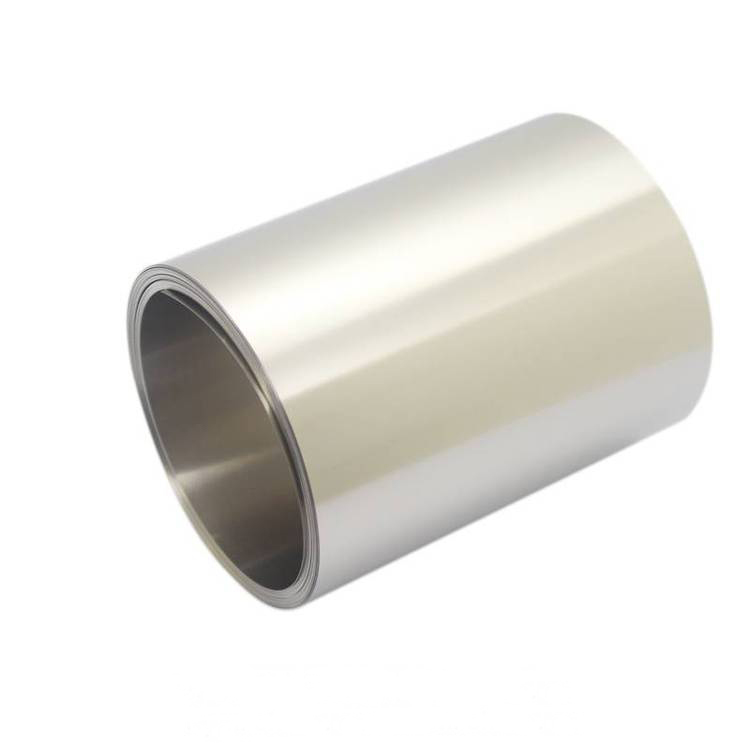
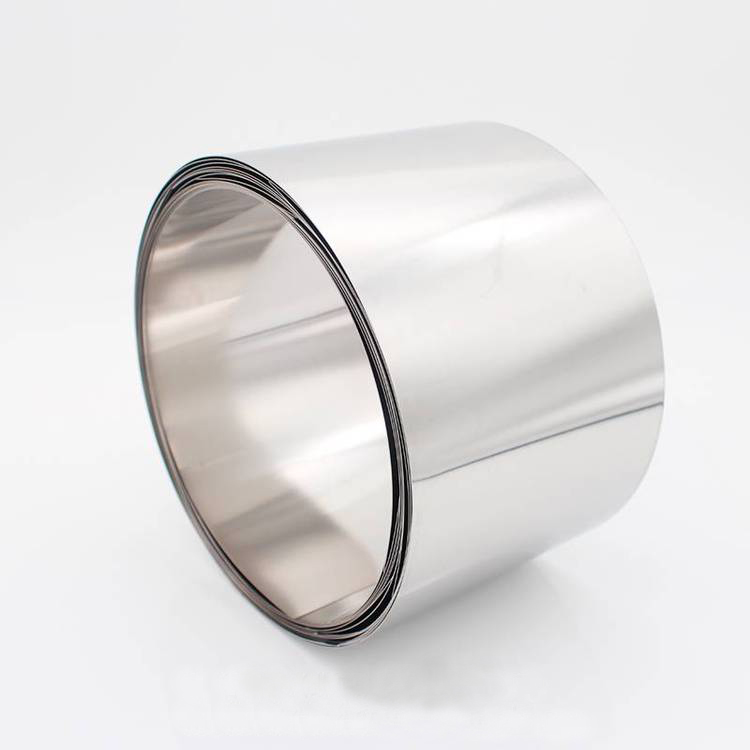
- High Strength-to-Weight Ratio: Titanium foil is known for its excellent strength-to-weight ratio, making it a lightweight yet durable material. This property is especially valuable in industries like aerospace, where minimizing weight while maintaining structural integrity is crucial.
- Corrosion Resistance: One of the standout features of titanium is its exceptional resistance to corrosion. It forms a stable oxide layer on its surface, protecting it from environmental factors such as water, air, and chemicals. This makes titanium foil ideal for use in harsh or corrosive environments.
- High-Temperature Resistance: Titanium foil can withstand high temperatures without compromising its mechanical properties. It remains strong and stable even at elevated temperatures, which is why it is used in high-performance applications like jet engines and chemical reactors.
- Biocompatibility: Titanium is biocompatible, meaning it is non-toxic and compatible with the human body. This makes titanium foil a popular choice for medical implants and devices, as it does not cause adverse reactions in the body.
- Excellent Fatigue Resistance: Titanium foil has excellent fatigue resistance, making it suitable for applications that require materials to endure repeated stress without failure. This property is critical in aerospace, automotive, and other engineering sectors.
- Non-Magnetic: Titanium is non-magnetic, which makes titanium foil a valuable material in electronic and medical devices where magnetic interference can affect performance.
- Formability and Flexibility: Titanium foil is highly malleable and can be easily formed into various shapes. It can be rolled, stamped, or processed to meet the specific needs of different applications, making it versatile in manufacturing processes.
-
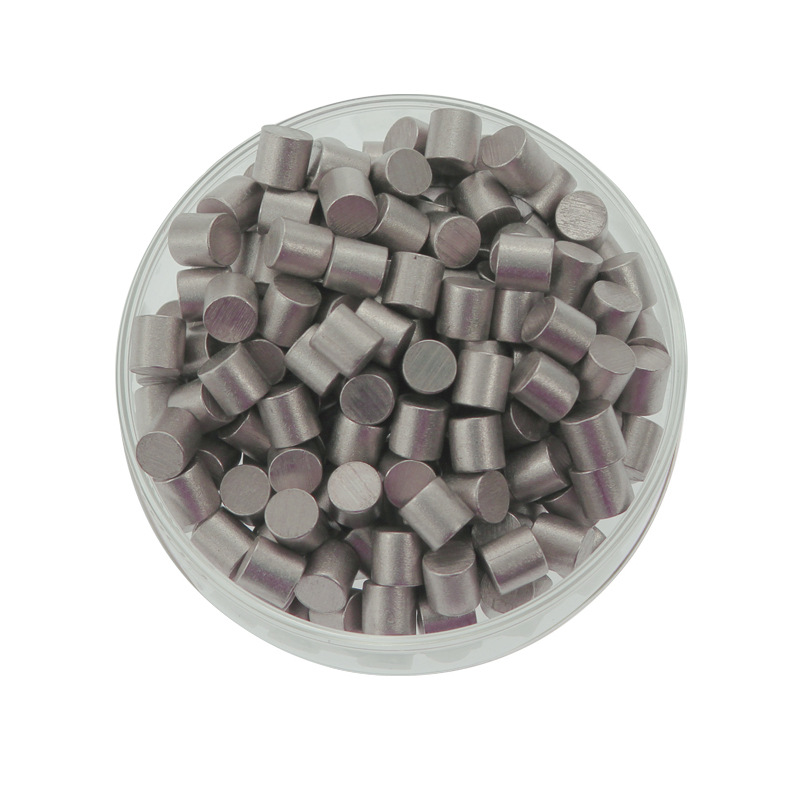
- High Corrosion Resistance: Titanium’s natural oxide layer provides exceptional resistance to corrosion, making it ideal for harsh environments.
- Strong Adhesion: Titanium films have excellent adhesion to a wide range of substrates, ensuring durable, stable coatings.
- Low Density: Titanium is lightweight, making it ideal for applications where weight reduction is important, such as in aerospace and medical industries.
- High Melting Point: With a melting point of 1,668°C, titanium can be used in high-temperature environments without degradation.
- Biocompatibility: Titanium’s biocompatibility makes it suitable for medical implants and devices.
-
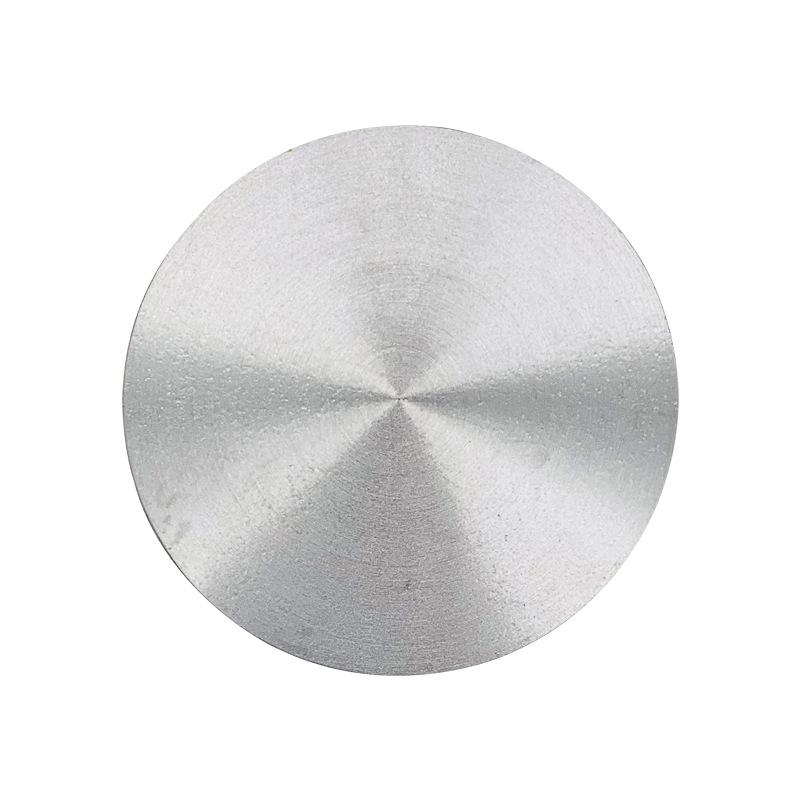
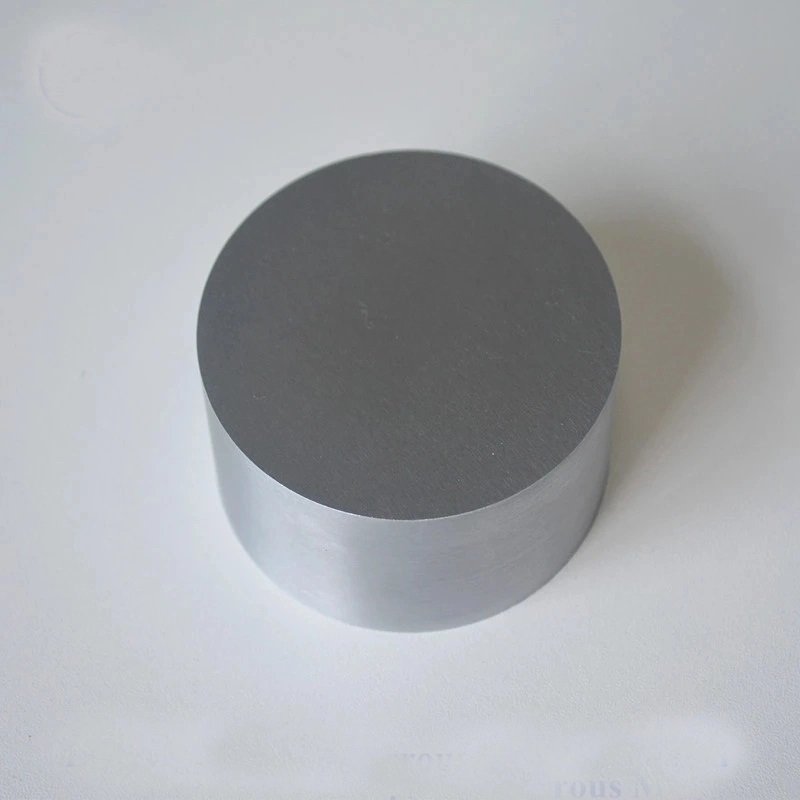
Titanium (Ti) sputtering targets are widely used in physical vapor deposition (PVD) processes to create thin films and coatings on various substrates. Titanium is known for its high strength-to-weight ratio, excellent corrosion resistance, and ability to form strong bonds with a variety of materials, making it an ideal choice for many industrial applications.
-
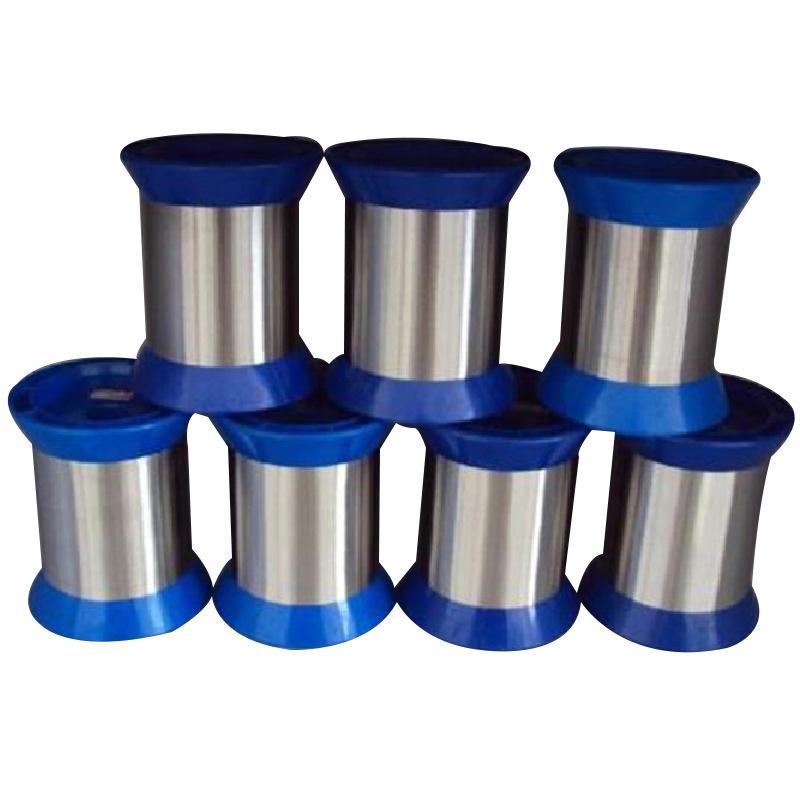
- Durability in Extreme Conditions: Titanium wire retains its properties in extreme temperatures and corrosive environments, ensuring reliable performance.
- Lightweight Design: The low density of titanium wire reduces the weight of structures and components, crucial for aerospace and automotive industries.
- Environmentally Friendly: Titanium is non-toxic and fully recyclable, making it a sustainable material choice.
- Customizability: Titanium wire can be manufactured in various diameters, grades, and finishes to meet specific industry requirements.
- Superior Surface Finish: The wire can be polished or coated to enhance its performance and appearance in specialized applications.
-
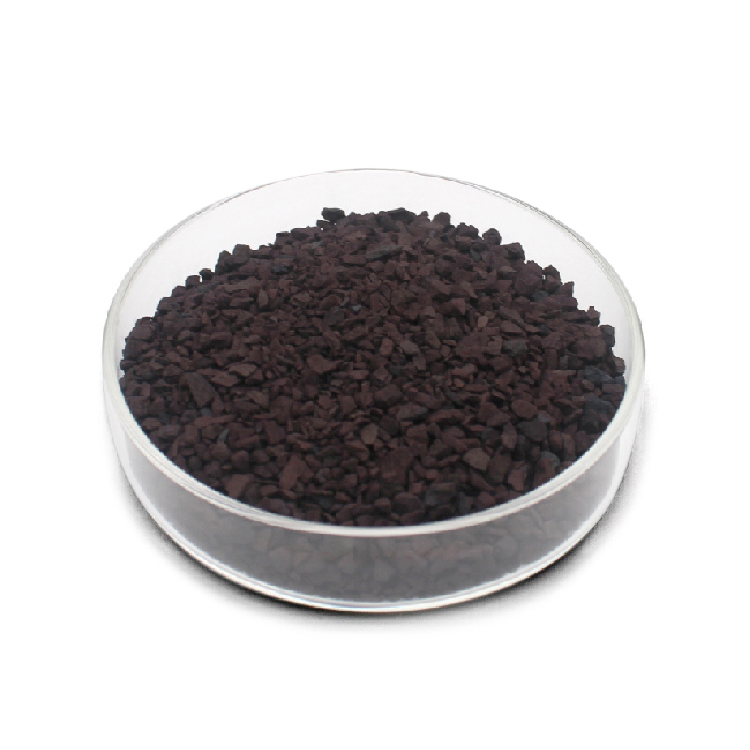
- High purity (≥99.99%).
- Excellent electrical conductivity and stability.
- Unique optical properties, including selective light absorption.
- Uniform pellet size for consistent deposition and performance.
- Customizable sizes and packaging for various applications.
-
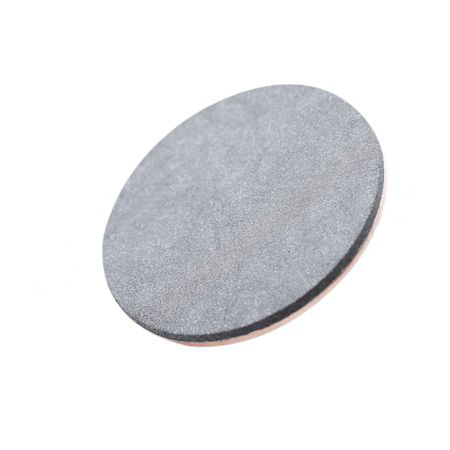
- High Purity: Ensures uniform film deposition with minimal contamination.
- Excellent Optical Properties: Provides transparency and reflectivity for optical applications.
- Electrical Conductivity: Suitable for applications requiring conductive thin films.
- Durable and Stable: Resistant to chemical and thermal degradation, ensuring long-lasting performance.
- Versatile Compatibility: Can be used with various sputtering systems and processes.
-
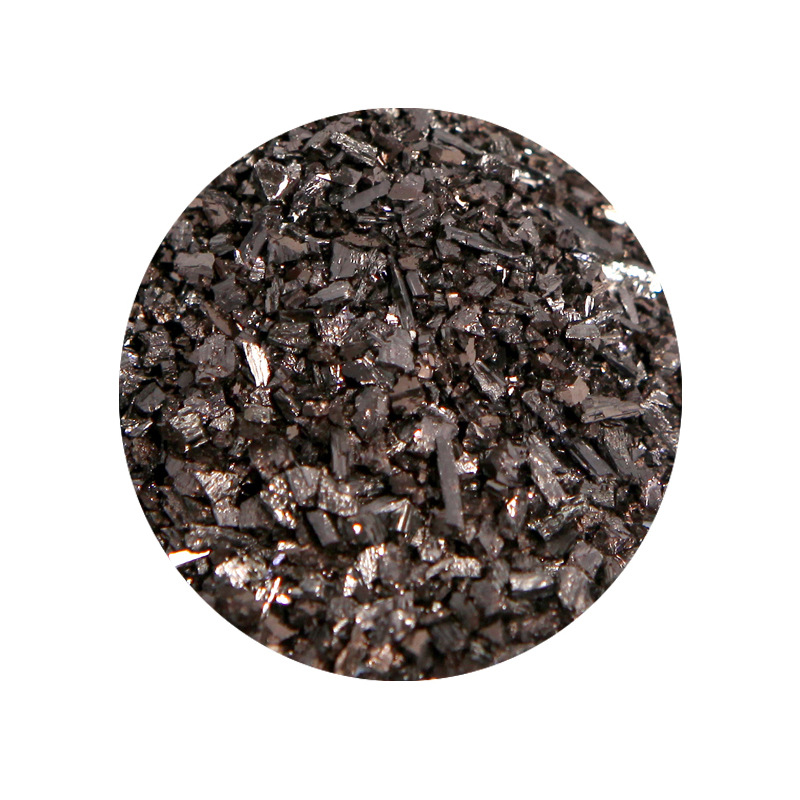
$25.00 – $130.00
- High Refractive Index: Ti₃O₅ has a high refractive index, making it suitable for optical coating applications where control of light reflection and transmission is essential.
- Excellent Thermal Stability: With a high melting point and stability at elevated temperatures, Ti₃O₅ is ideal for use in high-temperature processes like e-beam and thermal evaporation.
- Good Catalytic Properties: Ti₃O₅ has notable catalytic capabilities, especially in photocatalytic reactions for air and water purification.
- Durability and Hardness: Ti₃O₅ thin films are durable and resistant to wear, making them suitable for both protective and decorative purposes.
- Semiconducting Properties: With its semiconducting characteristics, Ti₃O₅ is useful in electronic components and sensor technology.
-
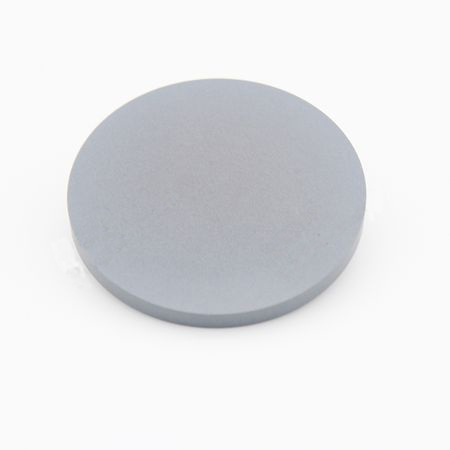
- High Purity: Ensures consistent and reliable thin-film quality.
- Stable Performance: Exceptional thermal and chemical stability for demanding applications.
- Customizable Configurations: Available in various sizes and forms to suit diverse deposition systems.
- Optical Clarity: Produces transparent coatings with excellent optical properties.
- Durability: High resistance to mechanical stress and environmental degradation.
-
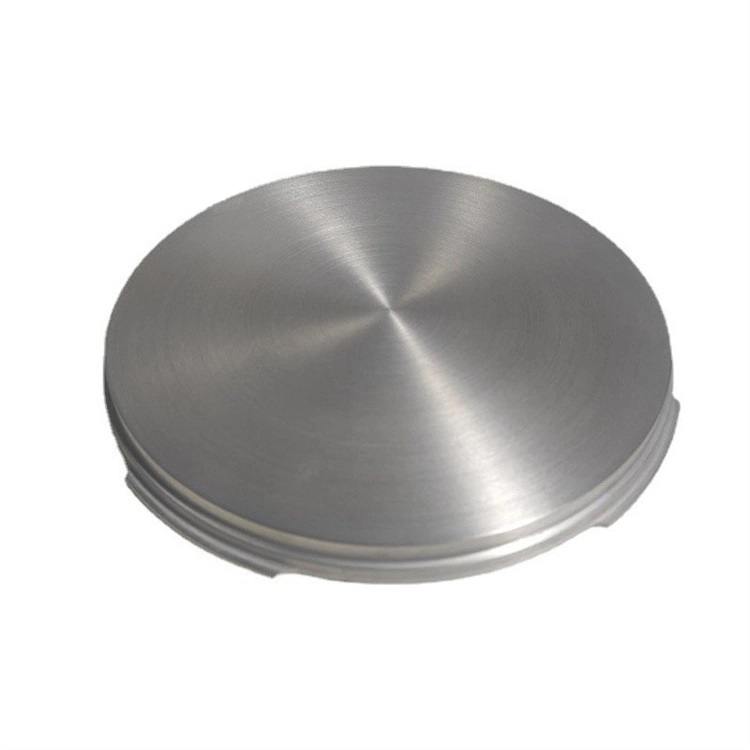
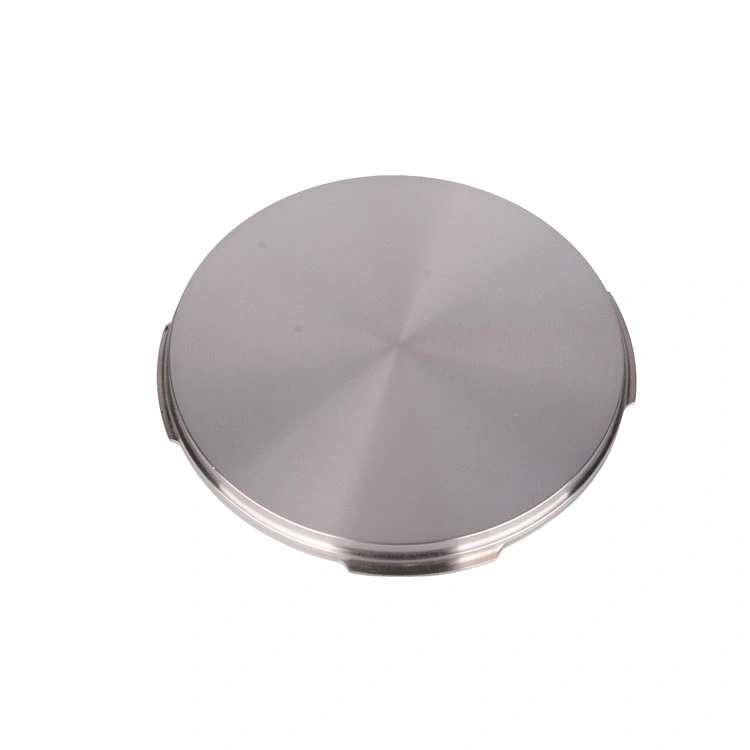
- High Strength-to-Weight Ratio: TiAl alloys combine the lightweight nature of aluminum with the strength of titanium, making them ideal for thin films in high-performance applications.
- Corrosion and Oxidation Resistance: TiAl films provide excellent resistance to corrosion and oxidation, ensuring durability and longevity in harsh environments.
- Thermal Stability: TiAl alloys can withstand high temperatures without losing mechanical properties, making them suitable for applications in high-temperature environments.
- Good Adhesion: TiAl thin films exhibit excellent adhesion to substrates, which is crucial for semiconductor and coating applications where film integrity is vital.
- Wear Resistance: The addition of titanium improves the hardness and wear resistance of TiAl coatings, contributing to extended tool life and enhanced component durability.
-
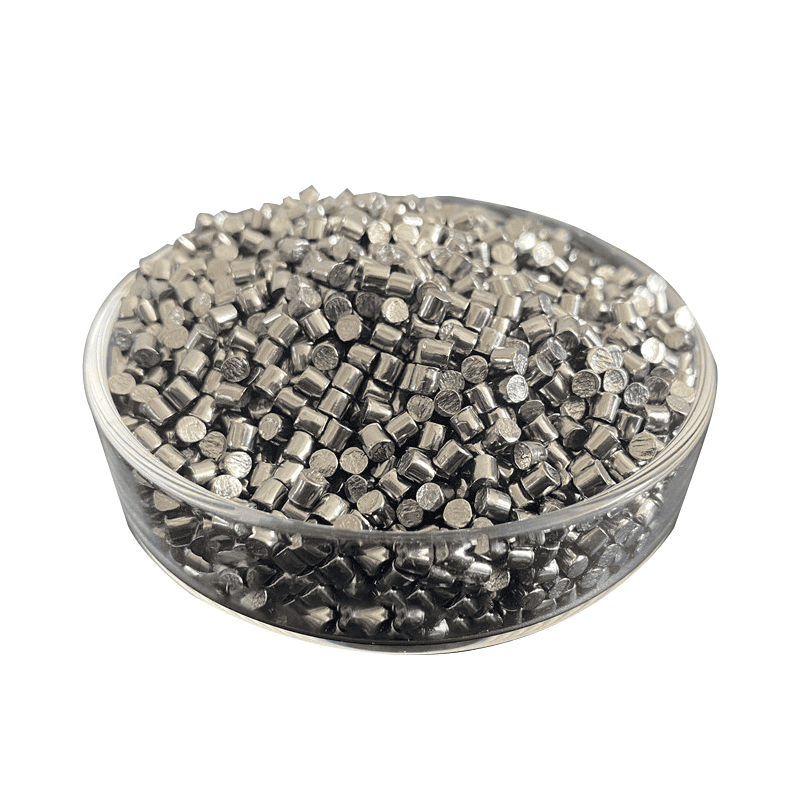
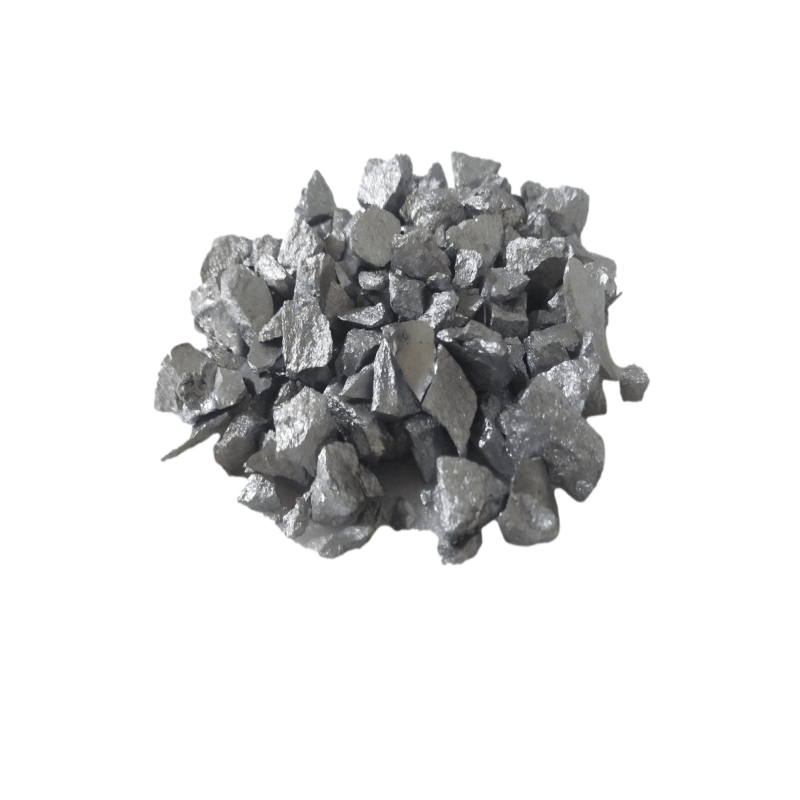
- High Strength-to-Weight Ratio: Ideal for lightweight and robust components.
- Excellent High-Temperature Resistance: Retains strength at elevated temperatures.
- Oxidation and Corrosion Resistance: Prolongs material lifespan in harsh environments.
- Customizable Ti-Al Ratios: Tailored to meet specific industrial requirements.
- Wide Range of Particle Sizes: From nano to micrometer scales for diverse applications.
-
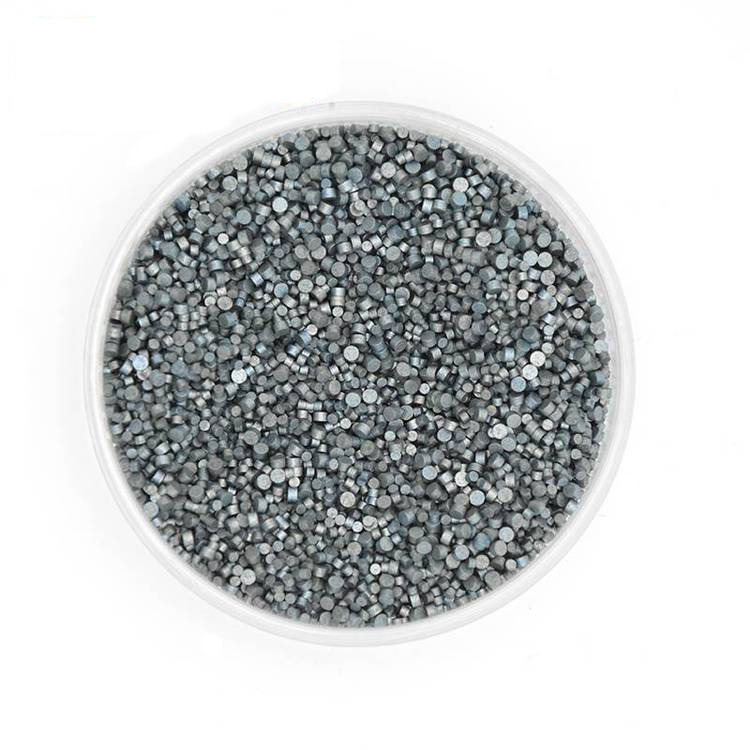
- High Hardness: TiB₂ has one of the highest hardness values among borides, making it ideal for creating hard coatings that resist wear and abrasion.
- Thermal Stability: It has excellent thermal conductivity and stability at high temperatures, which is critical for coatings used in high-temperature applications.
- Electrical Conductivity: TiB₂ is a good conductor of electricity, allowing its use in thin-film applications that require conductivity without sacrificing durability.
- Corrosion Resistance: TiB₂ is resistant to many corrosive environments, especially when exposed to molten metals or extreme industrial conditions.
- Strong Adhesion: TiB₂ coatings bond strongly to a variety of substrates, ensuring long-lasting performance in industrial and electronic applications.
-
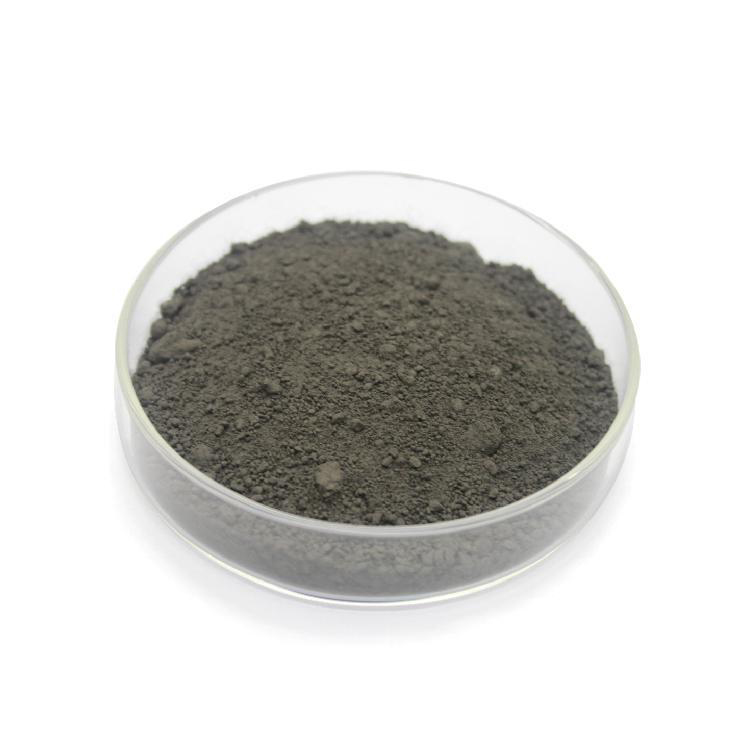
- Exceptional Hardness: Highly resistant to wear and abrasion.
- High Thermal Conductivity: Ideal for heat dissipation applications.
- Excellent Corrosion Resistance: Stable in molten metals and harsh chemical environments.
- Electrical Conductivity: Suitable for conductive ceramics and electrodes.
- High Melting Point: Withstands extreme temperatures without degradation.
- Customizable Particle Size: Tailored to specific application requirements.