Showing 1–12 of 26 results
-
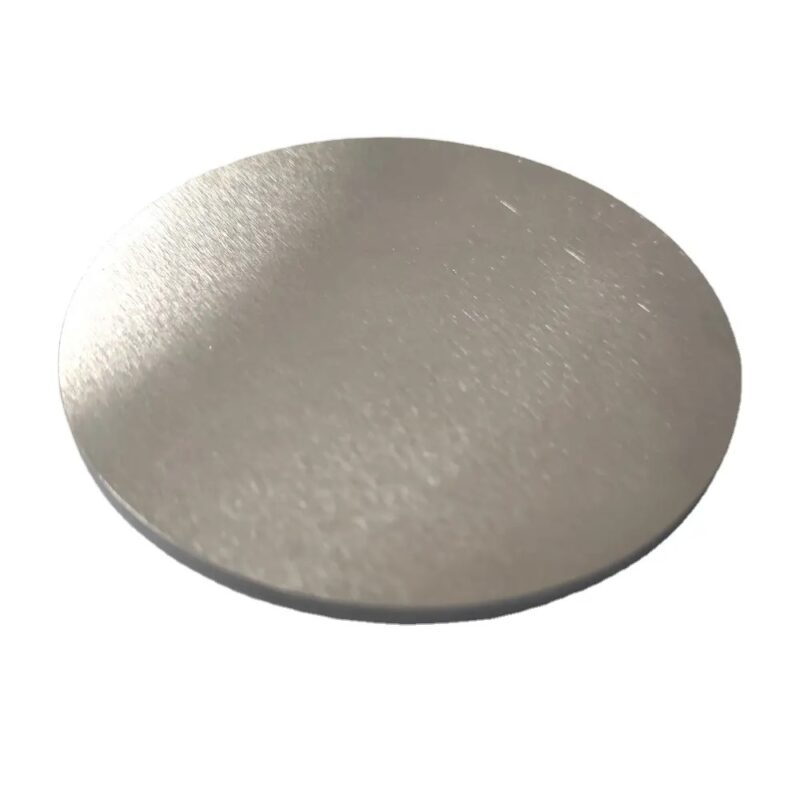
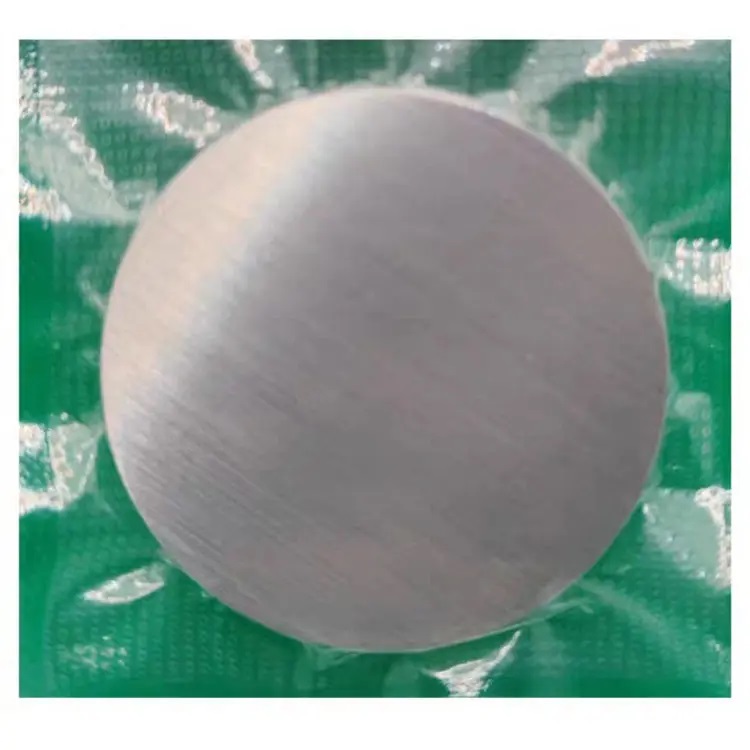
- Wear Resistance: CoCrW alloy provides excellent resistance to wear and abrasion, making it ideal for coatings on components subjected to mechanical stress and friction.
- Corrosion Resistance: The addition of chromium enhances the alloy’s resistance to corrosion, while tungsten improves hardness and durability, ensuring long-lasting performance in harsh environments.
- High-Temperature Stability: Cobalt and tungsten offer high thermal stability, allowing CoCrW thin films to retain their properties at elevated temperatures, making them suitable for high-heat applications such as in aerospace and power generation.
- Biocompatibility: CoCrW alloys are biocompatible, making them a preferred choice for medical applications such as orthopedic implants and surgical instruments.
- Excellent Hardness: The combination of tungsten and cobalt increases the hardness of the alloy, providing durable, wear-resistant coatings for industrial tools and components.
-
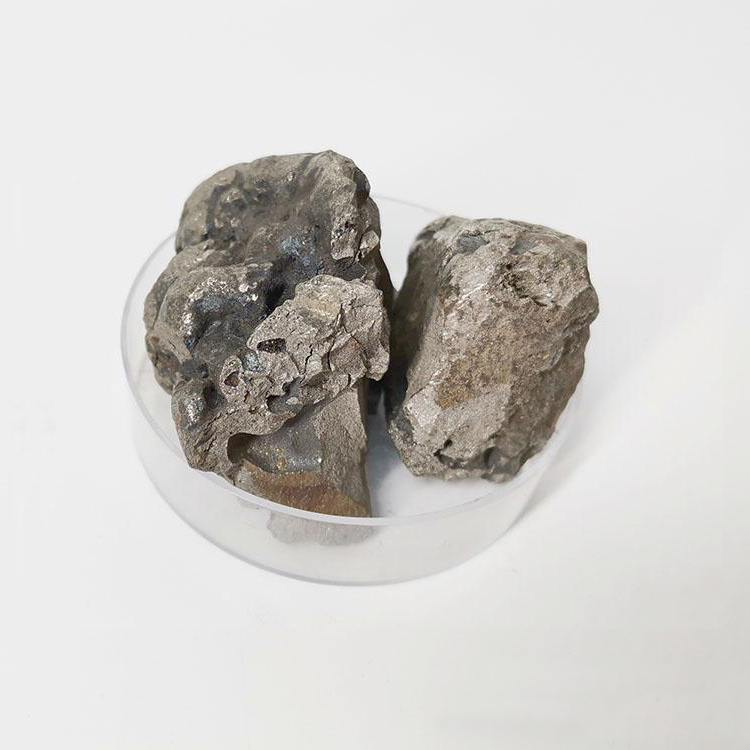
- High Hardness: Ensures excellent wear resistance for industrial applications.
- Thermal Stability: Performs reliably under high-temperature environments.
- Corrosion Resistance: Excellent chemical stability in harsh conditions.
- Customizable Compositions: FeW ratios tailored to specific application requirements.
- Versatile Particle Sizes: Available in nano to micrometer scales for diverse uses.
-
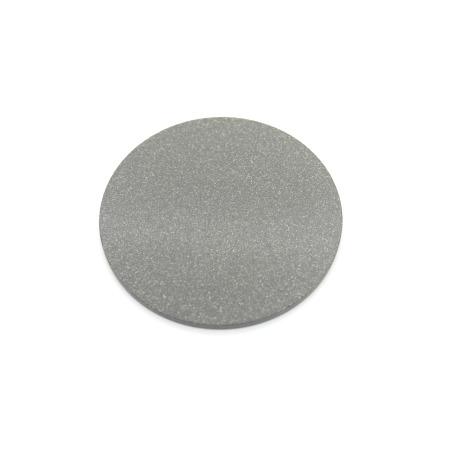
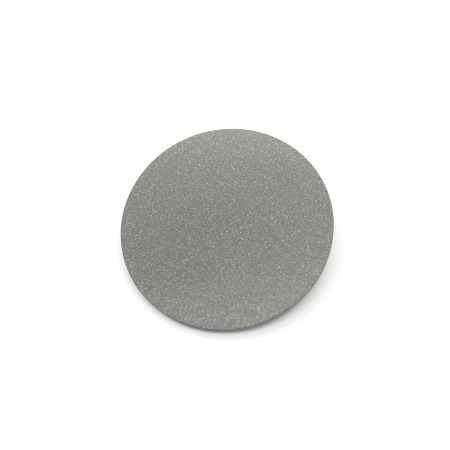
- High Optical Transparency: Enables the creation of efficient transparent films.
- Superior Conductivity: Provides excellent electrical performance for electronic applications.
- Thermal and Chemical Stability: Ensures reliability in high-temperature and reactive environments.
- Customizable Material Composition: Optimized for specific TCO requirements.
- Compatibility: Suitable for RF and DC sputtering systems.
-
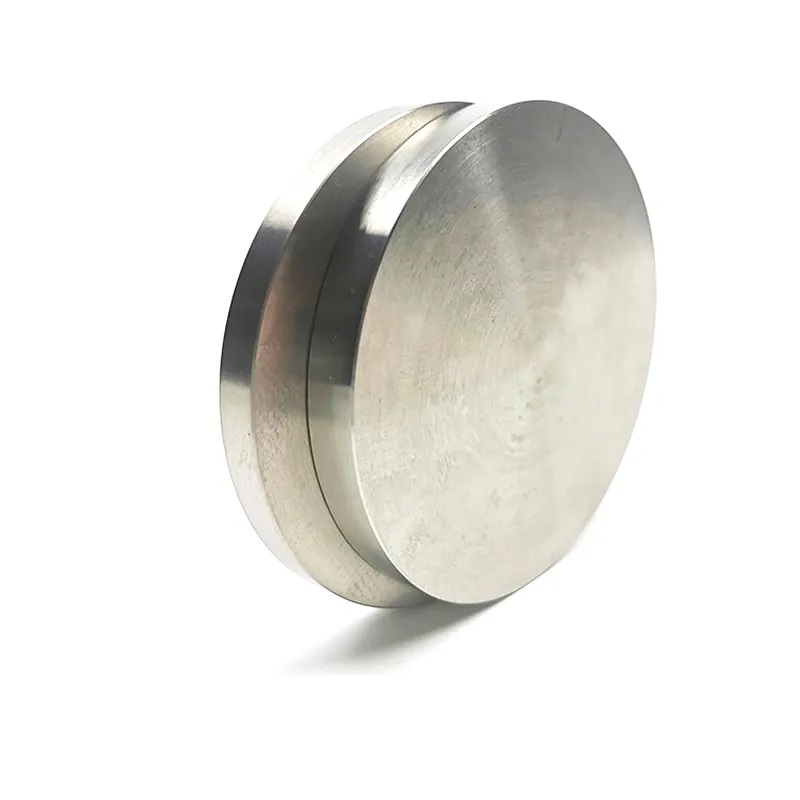
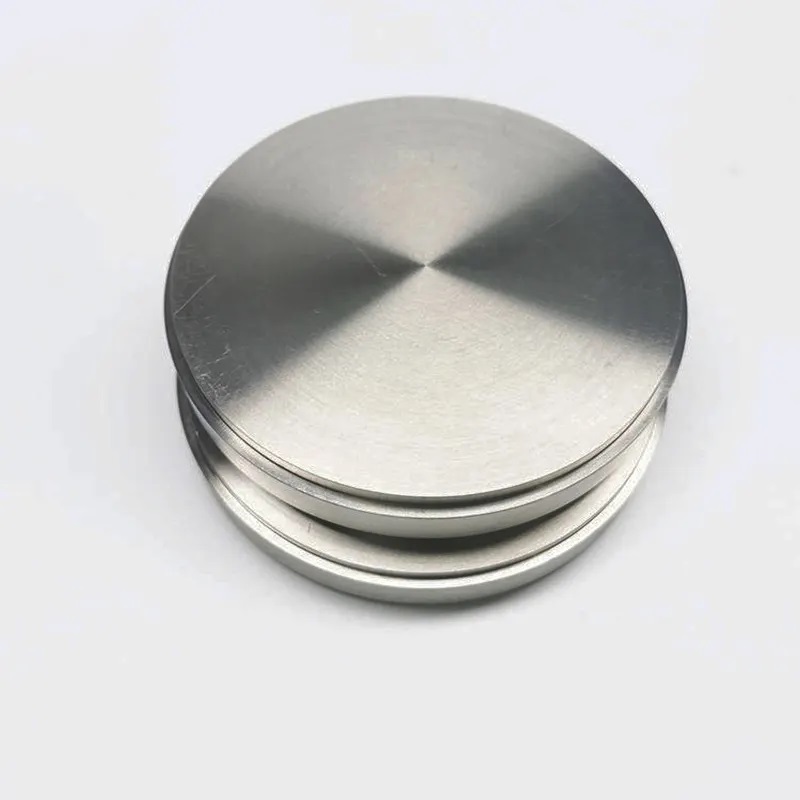
- Hardness and Durability: NiW alloys offer exceptional hardness and durability, making them ideal for wear-resistant coatings that protect mechanical parts and tools from wear and abrasion.
- Corrosion Resistance: NiW thin films provide strong resistance to corrosion, particularly in harsh environments exposed to moisture, chemicals, or high salinity, extending the service life of components.
- Thermal Stability: The alloy maintains its mechanical and chemical properties at elevated temperatures, making NiW thin films suitable for high-temperature applications in various industries.
- Magnetic Properties: The nickel content in NiW alloys provides magnetic characteristics that are useful in certain electronic and magnetic storage applications.
- Customizable Composition: The ratio of nickel to tungsten can be customized to fine-tune the properties of the thin film for specific applications, such as increasing hardness, wear resistance, or corrosion protection.
-
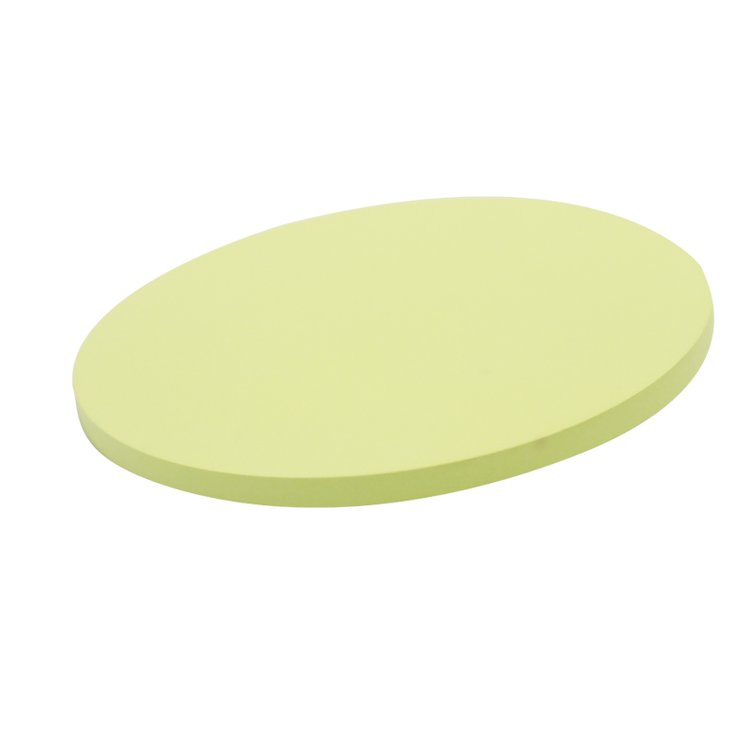
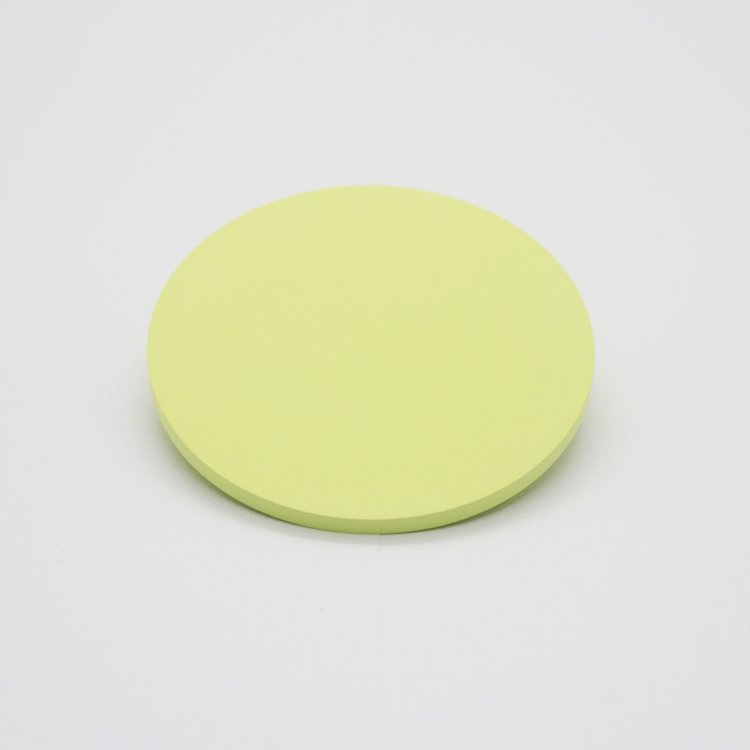
- High Purity: Ensures consistent film quality and performance.
- Customizable Dimensions: Available in a variety of sizes and shapes to meet specific requirements.
- Excellent Durability: Suitable for high-temperature and high-power sputtering processes.
- Uniformity: Enables consistent thin-film deposition for advanced technologies.
- Eco-Friendly Applications: Ideal for energy-efficient devices like smart windows.
-
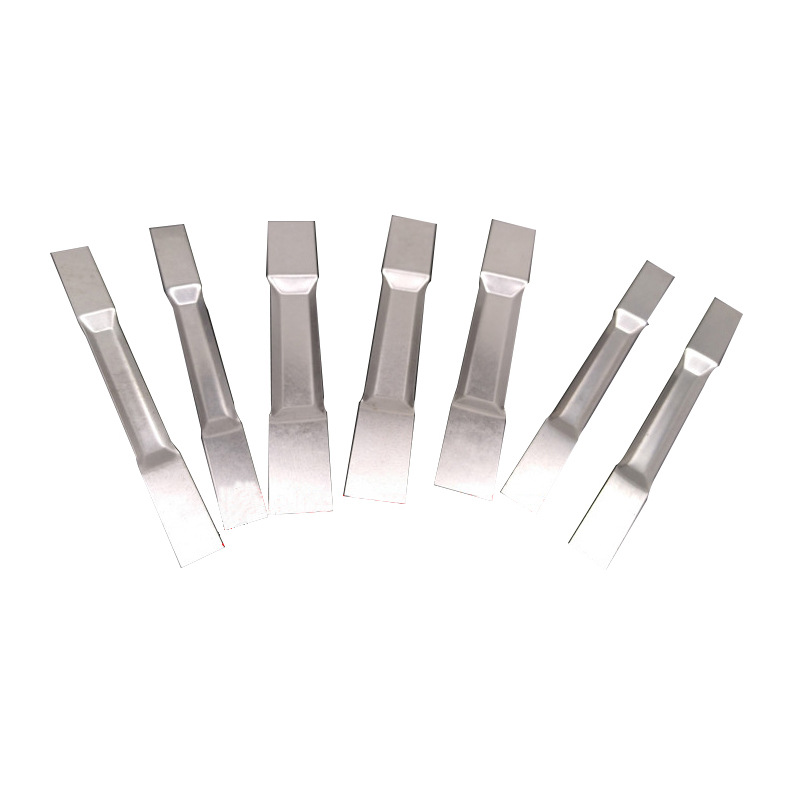
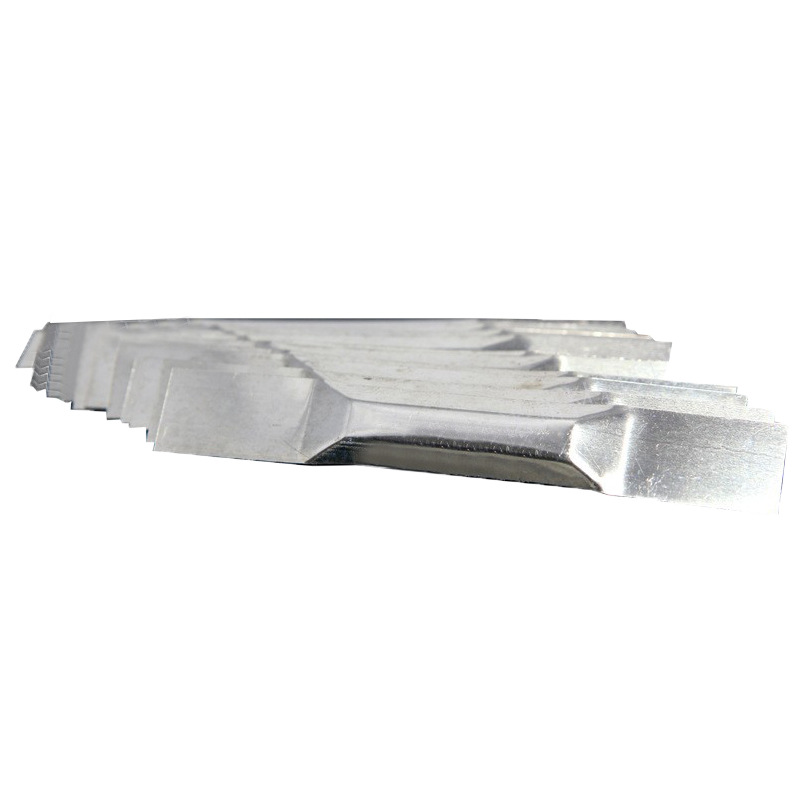
- Long lifespan due to exceptional wear resistance.
- Customizable design for specific applications.
- High purity ensures minimal contamination in sensitive processes.
- Suitable for both batch production and R&D applications.
-
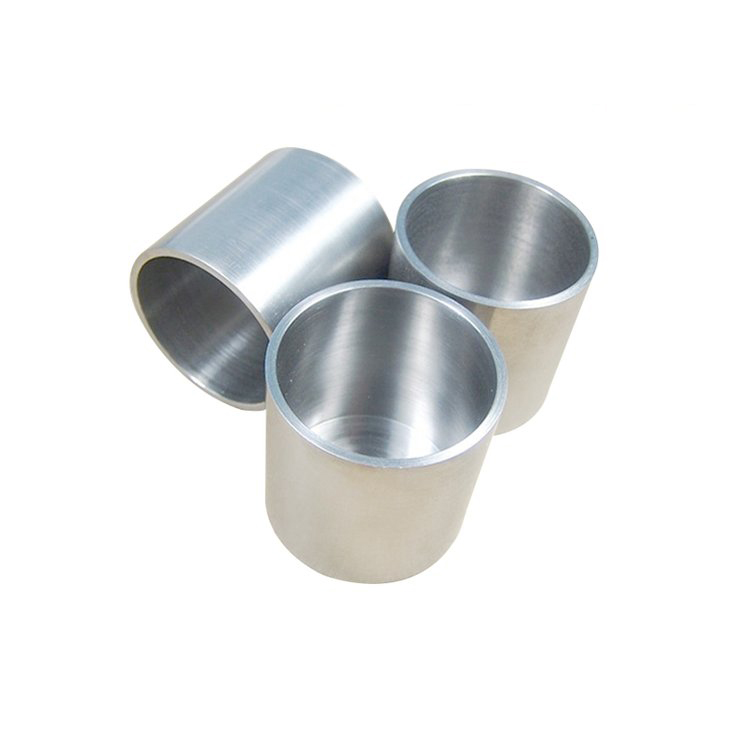
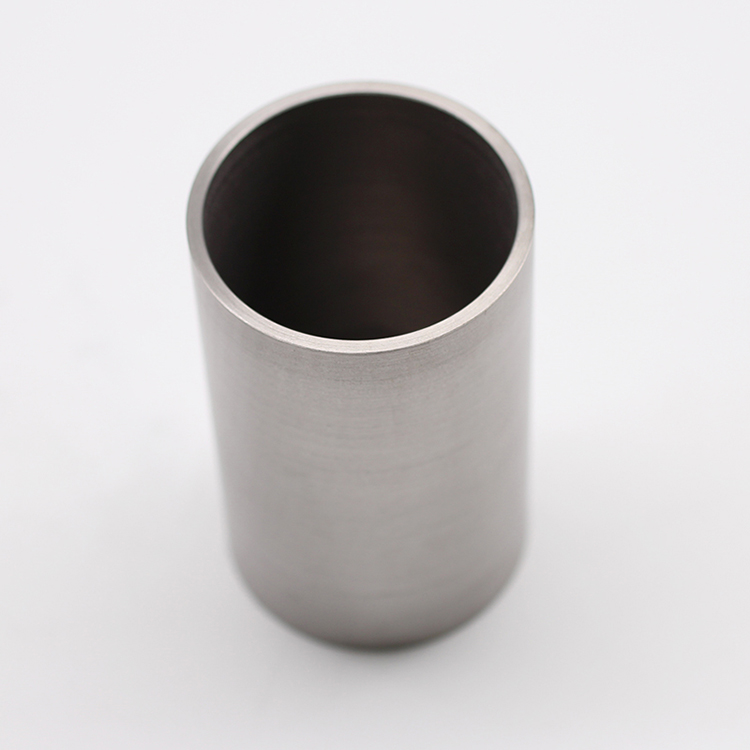
- High Melting Point: Tungsten has the highest melting point of all metals (3,422°C), making it suitable for extreme high-temperature environments.
- Thermal Stability: Excellent ability to withstand high temperatures without warping or breaking, ensuring consistent performance under heat stress.
- Corrosion Resistance: Highly resistant to chemical corrosion, particularly in reducing environments and molten metals, ensuring long-lasting use in aggressive chemical environments.
- Mechanical Strength: Very high tensile strength and hardness, ensuring that the crucible maintains its shape under both thermal and mechanical stress.
- Low Thermal Expansion: Tungsten’s low coefficient of thermal expansion minimizes cracking and deformation when subjected to rapid temperature changes.
- High Thermal Conductivity: Efficient heat distribution within the crucible helps in achieving uniform melting or material processing.
-
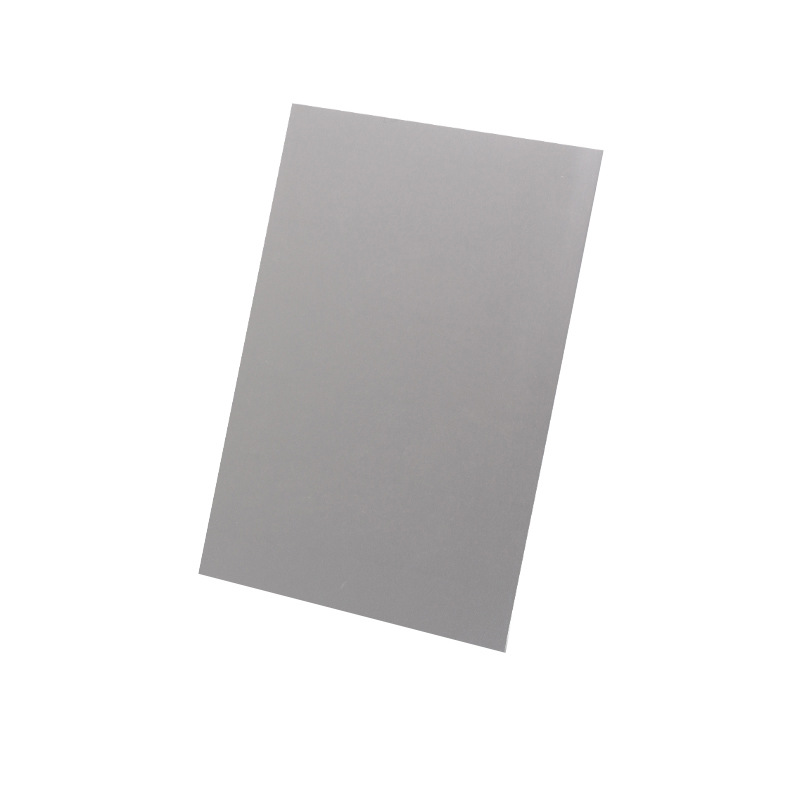
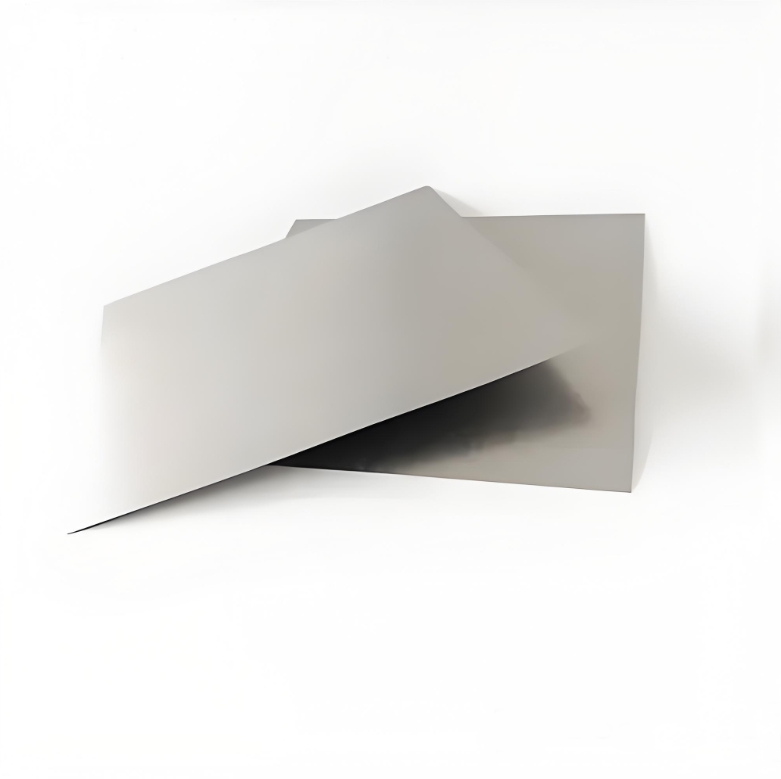
- High Melting Point: Tungsten has the highest melting point of any metal, around 3,422°C (6,192°F). This makes it perfect for high-temperature applications such as heat shields, aerospace components, and vacuum furnaces.
- Excellent Strength: Tungsten foil exhibits outstanding tensile strength, maintaining its integrity even under stress or at elevated temperatures. This property ensures that it is highly durable and reliable for demanding applications.
- Low Thermal Expansion: Tungsten has an extremely low coefficient of thermal expansion (CTE), which means it does not expand or contract significantly when subjected to temperature changes. This is crucial for applications requiring dimensional stability under fluctuating temperatures.
- High Density: With a density of approximately 19.25 g/cm³, tungsten is one of the heaviest metals, giving it excellent mass and stability for a variety of industrial uses.
- Corrosion Resistance: Tungsten is resistant to corrosion in most environments. It is particularly resistant to oxidation, making it suitable for applications in vacuum environments or where high chemical stability is required.
- Biocompatibility: Tungsten is biocompatible and is used in medical implants, surgical tools, and radiation shielding, where its non-reactive nature is a significant advantage.
-
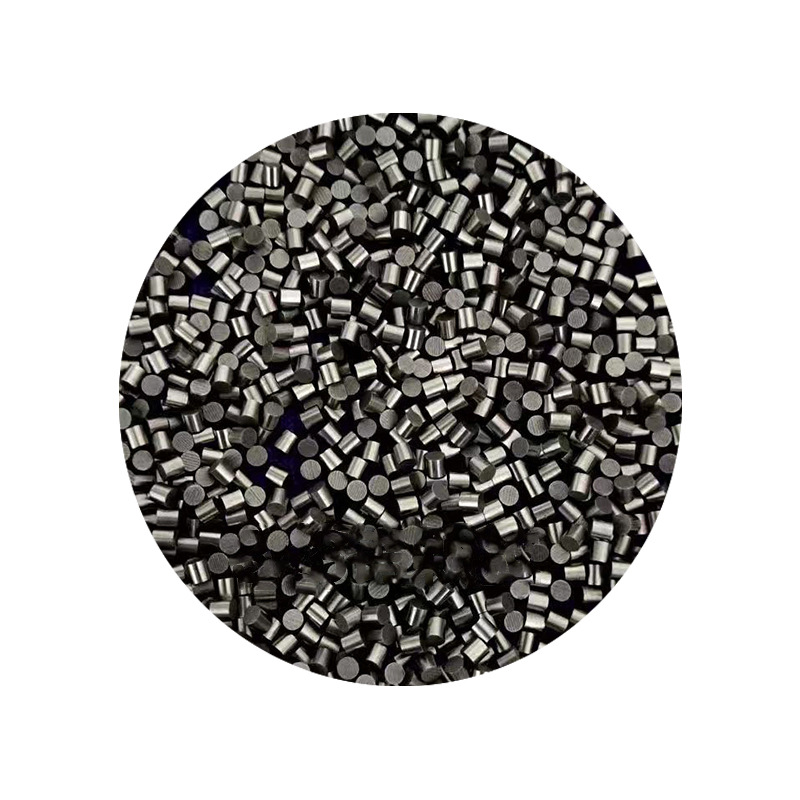
- High Purity: Ensures optimal performance in sensitive applications.
- High Melting Point: Allows for use in high-temperature environments without degradation.
- Excellent Electrical Conductivity: Ideal for applications requiring effective electrical connections.
- Thermal Stability: Maintains performance under varying temperature conditions.
- Robustness: Provides durability and reliability in demanding applications.
-
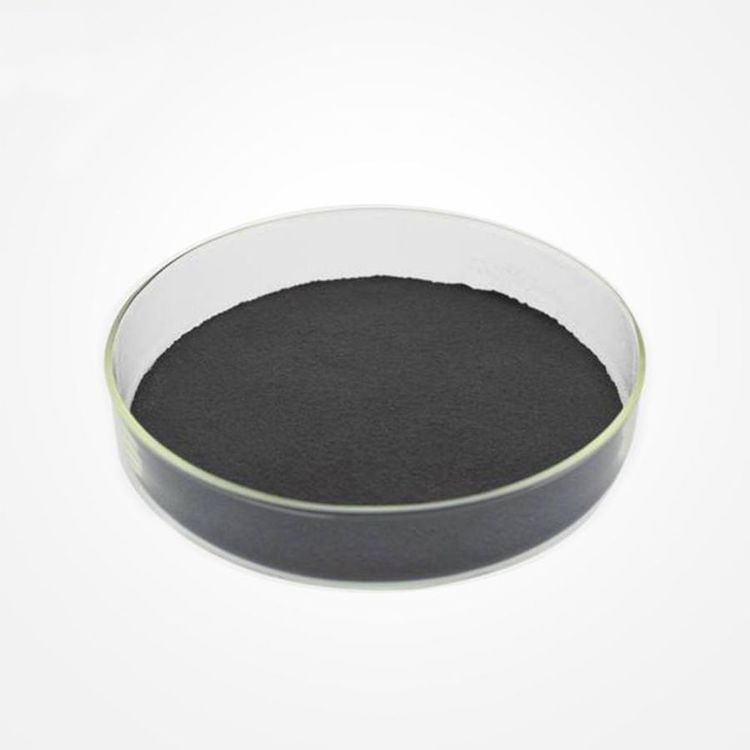
- High Purity: Exceptional quality with a purity of ≥99.9%.
- High Density: Ideal for applications demanding weight and strength.
- Thermal Stability: Excellent performance at high temperatures.
- Electrical Conductivity: Superior conductivity for electronic applications.
- Versatile Applications: Suitable for industries including aerospace, defense, and medical.
-
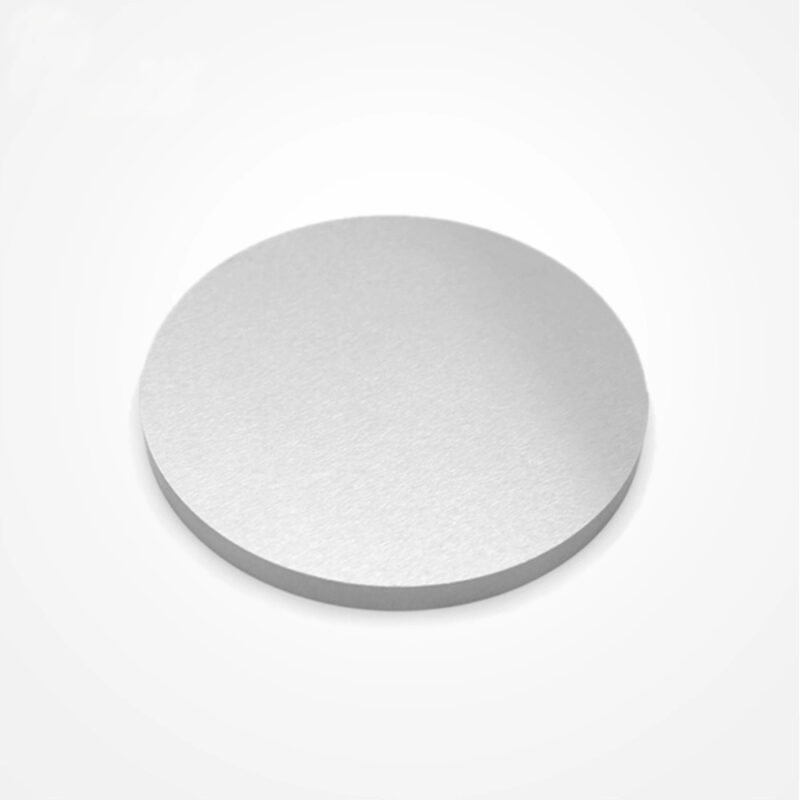
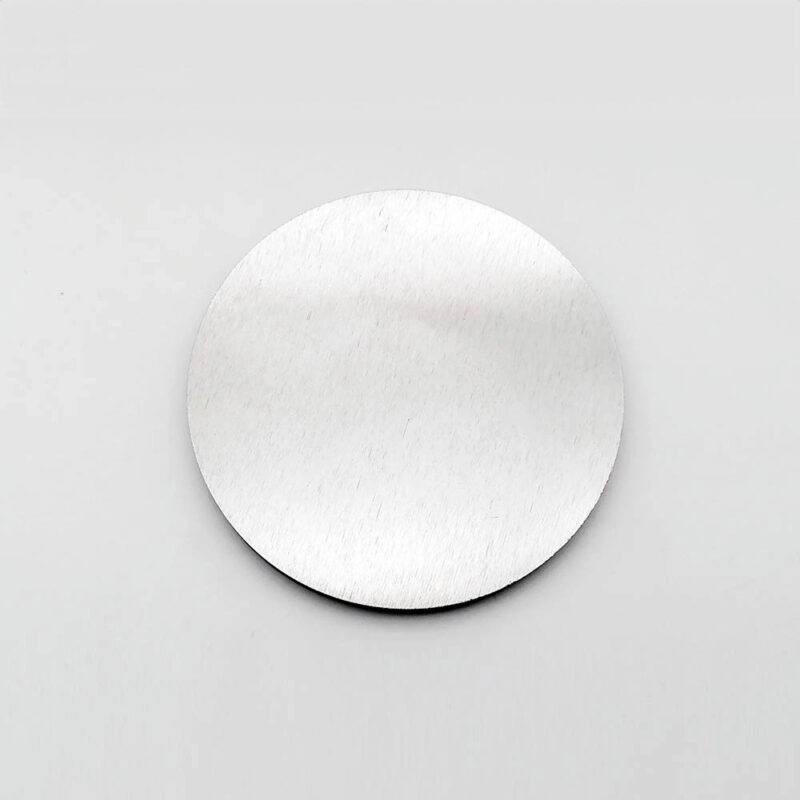
Tungsten sputtering targets are indispensable in industries that demand materials with high thermal and electrical conductivity, exceptional strength, and stability at extreme temperatures. These properties make tungsten a critical material in electronics, aerospace, energy, and medical applications.
-
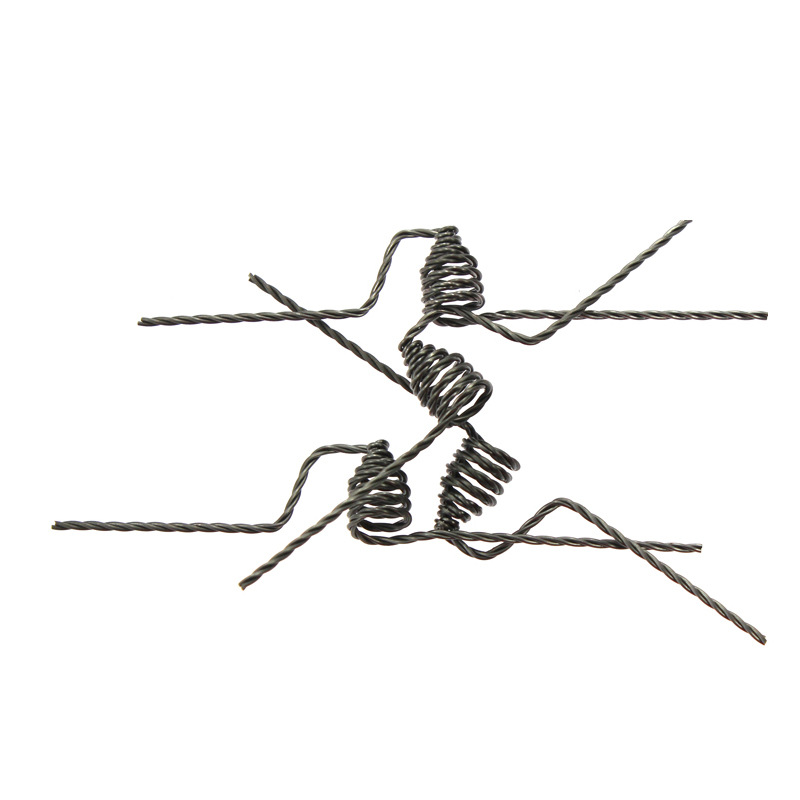
- High Melting Point: Tungsten has one of the highest melting points of any metal, at approximately 3,422°C (6,192°F). This property allows tungsten wire baskets to perform exceptionally well in high-temperature environments, such as in furnaces, aerospace applications, and high-energy industrial processes.
- Excellent Thermal Conductivity: Tungsten’s high thermal conductivity ensures that tungsten wire baskets distribute heat evenly, making them ideal for applications that require precise temperature control or rapid heat dissipation.
- Corrosion and Oxidation Resistance: Tungsten wire baskets exhibit excellent resistance to corrosion and oxidation, especially in environments with high temperatures and reactive gases. This makes them suitable for use in aggressive chemical environments where other metals may degrade.
- Mechanical Strength: Tungsten is known for its high mechanical strength and durability. Tungsten wire baskets can maintain structural integrity under high stress and heavy loads, making them suitable for industrial applications where strength and resilience are paramount.
- Density and Durability: Tungsten is a dense metal, which contributes to its durability and robustness. Tungsten wire baskets are strong yet stable, capable of supporting significant weights without deforming or losing their shape.
- Biocompatibility: Tungsten is biocompatible, making it suitable for use in medical applications. Although tungsten wire baskets are not commonly used in direct contact with biological tissues, their use in medical environments (e.g., sterilization or medical devices) requires biocompatibility.